Types of Sand in Foundry
In the realm of metal casting, sand plays a crucial role, serving as the primary molding material for foundries globally. Its versatility, availability, and cost-effectiveness make it a favored choice among manufacturers. However, not all sand is created equal; various types of sand are utilized in foundry applications, each offering its own characteristics and advantages. This article will explore the different types of sand found in a foundry setting.
1. Silica Sand
The most common type of sand used in foundries is silica sand, composed primarily of silicon dioxide (SiO2). It is prized for its high melting point, excellent moldability, and ability to withstand high temperatures without breaking down. Silica sand is typically used to create molds for casting metals like aluminum and iron. Its grains are well-rounded, which helps promote a smooth surface finish on castings. However, excessive inhalation of silica dust can pose health risks, necessitating proper ventilation and protective equipment for workers.
2. Green Sand
Green sand is a mixture of silica sand, clay, and water, and is popularly used in the foundry industry. The term green refers to the moisture content present in the sand, as it is not chemically cured when used to create molds. The clay acts as a binding agent, providing the necessary strength and malleability. Green sand molds are easy to produce, economical, and can effectively capture intricate details of the cast. Although effective, the handling and storage of green sand require careful management to prevent issues related to moisture loss or contamination.
types of sand in foundry
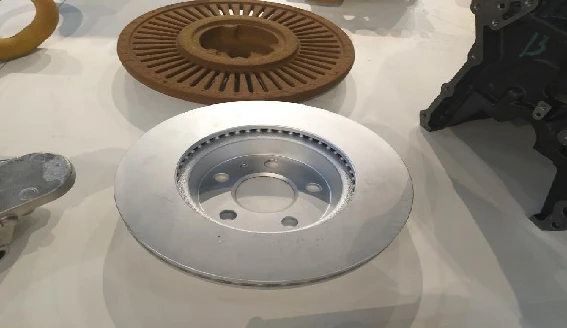
3. Resin-Bonded Sand
Resin-bonded sand employs a mixture of sand coated with synthetic resins. This type of sand provides superior strength and dimensional accuracy of molds compared to traditional green sand. The resins bond the sand particles together, resulting in molds that can be heated to cure the resin. This process generates molds that are highly detailed and can withstand the rigors of high-temperature metal casting. While resin-bonded sand offers excellent performance, it is typically more expensive and requires proper handling and disposal due to the chemical nature of the resins.
4. Other Specialized Sands
In addition to the common types mentioned, foundries may also employ specialized sands such as olivine sand, chromite sand, and zircon sand. Olivine sand, derived from the mineral olivine, offers good refractory qualities and is eco-friendly. Chromite sand provides excellent thermal resistance and is often used for casting high-temperature alloys. Zircon sand, known for its high melting point and low thermal expansion, is used for producing precision castings.
Conclusion
The selection of sand in foundry operations is vital to the quality and efficiency of metal casting processes. From the widely-used silica and green sands to specialized resin-bonded and mineral sands, each type offers distinct advantages tailored to specific casting needs. As the industry evolves, ongoing research and development in sand technology will continue to improve the performance of foundry materials, ultimately enriching the quality of cast products.
Post time:lis . 02, 2024 11:22
Next:steel sand casting suppliers