Types of Sand Used in Sand Casting
Sand casting is one of the oldest and most widely used metal casting processes. It involves creating a mold from a mixture of sand and a binding agent, into which molten metal is poured to create a desired shape. The type of sand used in this process plays a crucial role in determining the quality and characteristics of the final product. In this article, we will explore the various types of sand used in sand casting, their properties, and their applications.
Types of Sand Used in Sand Casting
Another type of sand used in sand casting is green sand, which is a mixture of silica sand, clay, water, and other additives. Green sand is called so because it is used in its moist state, and it requires no additional curing before pouring the metal. The clay in green sand acts as a binder, giving the mold strength and plasticity. Green sand is known for its excellent ability to capture fine details and is commonly used in the production of ferrous and non-ferrous castings. The moisture in green sand also helps to prevent the formation of cracks during the casting process.
types of sand used in sand casting
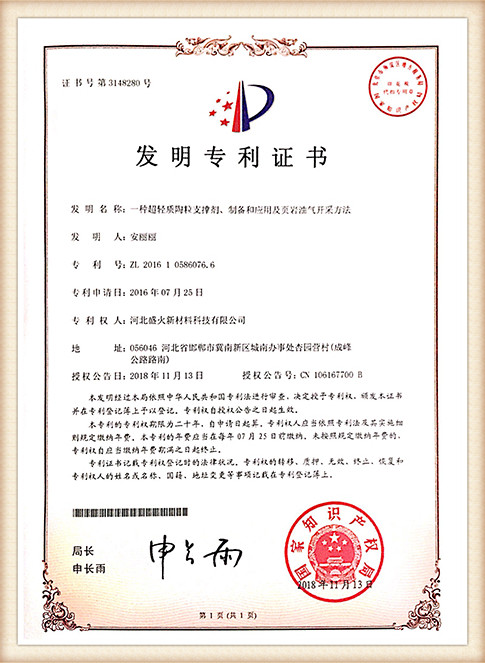
Resin sand is another popular choice in the casting industry. This type of sand uses a resin binder instead of clay, providing superior strength and stability. Resin sand molds can be created with a higher density, allowing for more precise casting with thinner walls and better surface finishes. Additionally, resin sand can be reused multiple times, making it a cost-effective option for high-volume production runs. Its ability to work with complex geometries and intricate designs makes resin sand favored in various industries, including automotive and aerospace.
Another specialized type of sand is oil sand, which incorporates the use of oil as a binder. The oil provides additional strength and flexibility to the mold, allowing for better reproduction of intricate details. Oil sand is particularly useful for creating larger castings or those that require extended mold life. However, the use of oil can complicate the cleaning process and may introduce environmental concerns.
Lastly, there are specialty sands such as zircon sand, chromite sand, and olivine sand, which are chosen for specific applications based on their unique properties. Zircon sand, for instance, has a high melting point and is often used in casting high-temperature alloys. Chromite sand offers resistance to metal contamination and is beneficial in the casting of ferrous alloys. Olivine sand, while less common, is valued for its thermal stability and ability to produce high-quality castings.
In conclusion, the choice of sand in the sand casting process is paramount to achieving the desired casting properties. From silica sand and green sand to resin sand and specialized variants, each type has its advantages and is suited for specific applications. Understanding these different types of sand helps manufacturers optimize their casting processes and produce high-quality metal components.
Post time:wrz . 09, 2024 11:48
Next:标题TitleΡητίνηΕπικαλυμμένοςΆμμος-ΥψηλήςΠοιότηταςΣαπούνιακαιΛύσεις