The Steel Sand Casting Process A Comprehensive Overview
Steel sand casting is a widely used manufacturing process that involves pouring molten steel into a mold made from sand. This method is favored for its ability to create complex shapes with high precision and is commonly employed in the production of various components such as engine blocks, machine parts, and structural components. Understanding the steel sand casting process involves examining several key stages, from mold preparation to finishing treatments.
Mold Preparation
The first step in the steel sand casting process is the preparation of the mold. Traditionally, molds are made using a mixture of sand, clay, and water. This mixture is compacted around a pattern – a replica of the object to be cast. The pattern can be made of metal, wood, or plastic and is designed to withstand the heat of the molten steel. Once the sand is compacted around the pattern, it forms a cavity in the shape of the desired part. The mold halves are then joined together, and any necessary gating systems, which allow the molten steel to flow into the mold, are incorporated.
Melting Steel
The next critical stage is the melting of the steel. Steel is typically melted in electric arc furnaces or induction furnaces, where it reaches temperatures over 1,500 degrees Celsius. This molten steel is carefully monitored to maintain the correct temperature and composition, ensuring that it meets the specifications required for the final product. The quality of the steel used is crucial, as impurities can lead to defects in the finished casting.
Pouring and Solidification
steel sand casting process
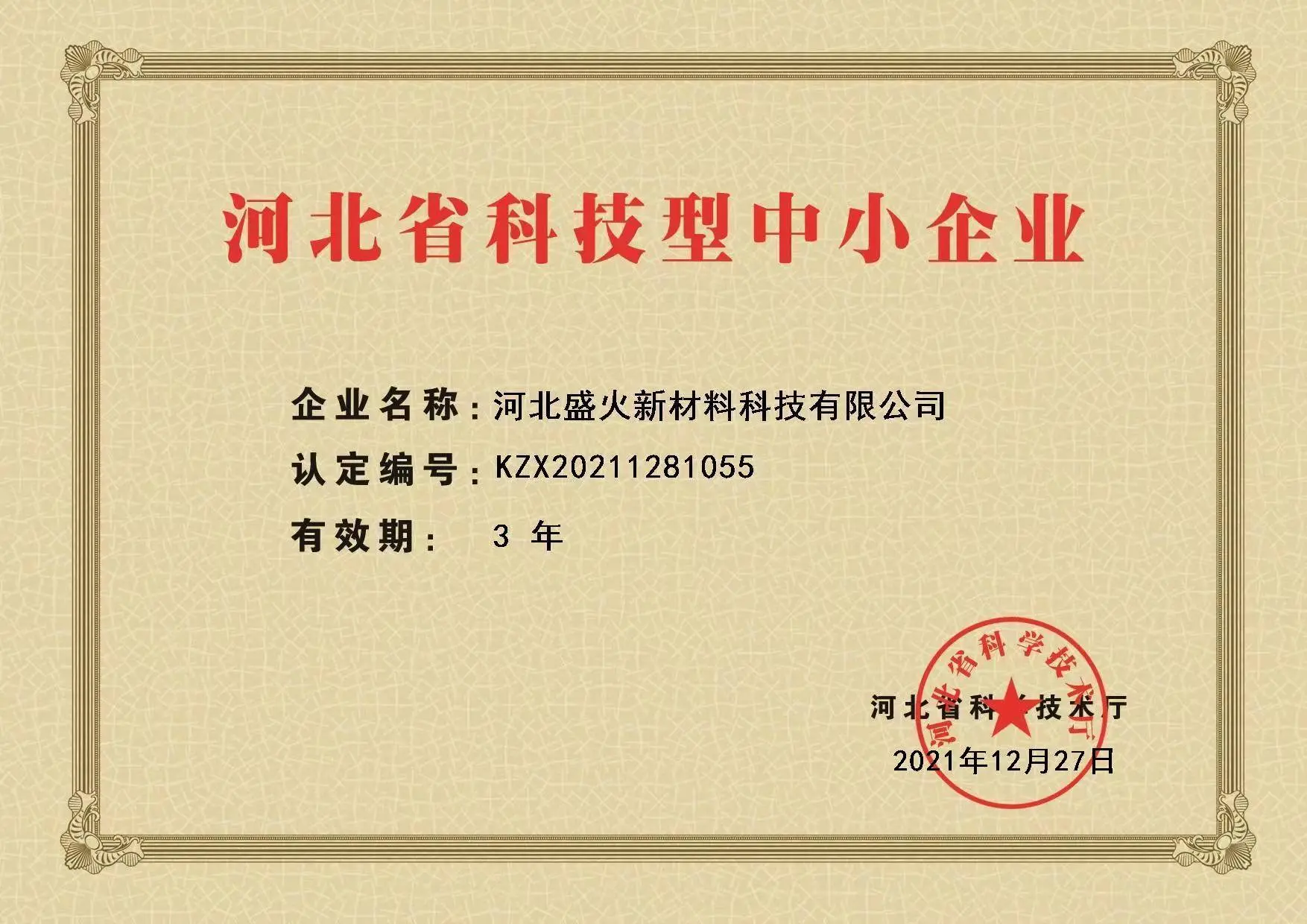
Once the steel has reached the desired temperature, it is poured into the mold through the gating system. This process requires precision; any turbulence in the flow can lead to defects such as inclusions or air pockets. After pouring, the molten steel begins to cool and solidify, taking on the shape of the mold. The cooling process can be influenced by various factors, including the thickness of the casting and the ambient temperature. Controlled cooling is essential to avoid stress concentrations that could lead to warping or cracking.
Mold Removal and Finishing
After the steel has solidified, the mold is broken away, a process known as shakeout. The cast steel component is then cleaned, which often involves sandblasting or other methods to remove any residual sand. Following cleaning, the castings may undergo various finishing processes, such as machining, heat treatment, or surface treatment, to achieve the desired dimensions and surface quality. These steps are vital for ensuring the part meets the necessary functional and aesthetic requirements.
Advantages and Applications
Steel sand casting offers several advantages, including the ability to produce large components and intricate designs at relatively lower costs compared to other casting methods. Its versatility makes it applicable in various industries, from automotive to aerospace, where robust and reliable components are essential.
In conclusion, the steel sand casting process is a valuable manufacturing technique that combines traditional methods with modern technology. Understanding this process helps manufacturers produce high-quality steel components efficiently, meeting the diverse needs of various industries. As technology advances, the steel sand casting process will continue to evolve, unlocking new possibilities for innovation in manufacturing.
Post time:paź . 31, 2024 09:48
Next:types of foundry sand