The Role of Sand in Sand Casting Types, Characteristics, and Applications
Sand casting is one of the oldest and most widely used manufacturing processes, apt for producing complex metal components. At its core, the effectiveness and quality of this method heavily rely on the type of sand used in the molding process. In this article, we explore the significance of sand in sand casting, the various types of sand utilized, and their characteristics that contribute to high-quality castings.
Understanding Sand Casting
Sand casting involves creating a mold from sand, into which molten metal is poured to form various shapes. The process allows for the production of intricate designs and large parts with relative ease. The main elements of sand casting include the mold, core, and the pouring of molten metal. Each of these components plays a crucial role in ensuring the final product meets quality standards.
Types of Sand Used in Sand Casting
1. Silica Sand This is the most commonly used sand in sand casting due to its high melting point, durability, and ability to create fine molds. Silica sand is composed primarily of silicon dioxide (SiO2), making it excellent for high-temperature applications. Its grains are relatively uniform, ensuring a smooth surface finish for the casting.
2. Green Sand Unlike traditional dry sands, green sand is a mixture of silica sand, clay, and moisture. The clay binds the sand grains together, and the moisture helps in the mold's integrity. Green sand is popular for its ease of use and adaptability, making it a preferred choice for many foundries. It allows for excellent detail and dimensional accuracy in casted parts.
3. Resin-Bonded Sand This type of sand uses resin as a binding agent to create molds with superior strength and finish. The resin-bonded sand is typically more expensive than traditional sand mixtures but significantly enhances the surface smoothness, reduces casting defects, and allows for greater production rates. This makes it ideal for high-precision applications.
4. Shell Sand Comprising a mixture of fine sand and thermosetting resins, shell sand molds are formed by heating a pattern, causing the resin to cure and harden. This creates a durable mold that can withstand higher temperatures. Its use is notable in industries looking for a fine surface finish and minimal dimensional tolerance.
sand used for sand casting
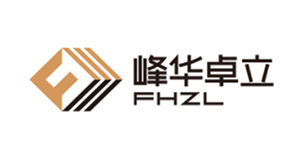
5. Chromite Sand Known for its high thermal conductivity and melting point, chromite sand is often used in high-temperature applications. Its resilience against thermal shock and excellent casting properties make it a good choice for producing steel and iron components. However, it is more expensive than silica, resulting in its limited use.
Characteristics of Sand in Casting
The performance of sand in the casting process is evaluated based on several characteristics
- Grain Size Finer sands produce smoother surface finishes, while coarser sands allow for better airflow and reduce the risk of casting defects. - Shape The shape of the sand grains affects the mold's cohesiveness and strength. Round grains typically provide better flowability and compaction than angular grains.
- Moisture Content The right moisture levels ensure optimal mold strength and prevent cracking during the casting process.
- Refractoriness The ability of the sand to resist heat is critical, especially when working with high-temperature metals.
Conclusion
The choice of sand significantly impacts the efficiency and quality of the casting process. Understanding the different types of sand and their characteristics allows manufacturers to select the most suitable material for their specific applications. With ongoing advancements in casting technologies and materials, the role of sand will remain essential in shaping the future of metal fabrication. As industries continue to innovate, the development and selection of superior sand types will undoubtedly play a pivotal role in improving casting quality and efficiency.
Post time:gru . 07, 2024 11:50
Next:sand casting tolerances