Sand Casting Procedure A Comprehensive Overview
Sand casting, one of the oldest and most versatile manufacturing processes, allows manufacturers to create complex metal parts with high precision. This procedure is widely used in foundries due to its flexibility, cost-effectiveness, and capacity for producing large components. In this article, we will delve into the sand casting procedure, breaking it down into its essential stages and discussing the materials and techniques involved.
1. Designing the Pattern
The first step in the sand casting process is designing a pattern, which is a replica of the final product to be cast. Patterns can be made from various materials, including wood, metal, or plastic, depending on the complexity, size, and the number of pieces required. The choice of material greatly influences the lifespan of the pattern and the intricacy of the design. The pattern is often made slightly larger than the final product to account for shrinkage during solidification.
Once the pattern is ready, the next step is to create a mold. Sand is the primary material used in this process, typically mixed with binders to help hold its shape. The most common molding sands are silica sand, clay, and sometimes olivine. The process involves placing the pattern in a molding box, sand is then packed around it, and a release agent is applied to prevent the sand from sticking to the pattern.
After packing, the sand mixture is compacted using a machine or manually to ensure it maintains the shape of the pattern. Once the mold is formed, the pattern is carefully removed, leaving a cavity in the sand that reflects the shape of the final casting. This process may produce two halves, or halves can be combined for more intricate shapes.
3. Pouring Molten Metal
sand casting procedure
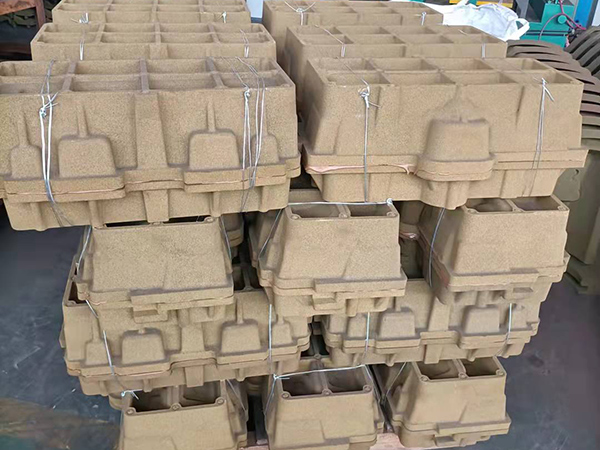
With the mold prepared and the pattern removed, the next step is pouring molten metal into the mold. The choice of metal depends on the specific requirements of the casting, with common types including aluminum, bronze, iron, and steel. The metal is heated in a furnace until it reaches a molten state.
Once at the appropriate temperature, the molten metal is carefully poured into the mold cavity through a gating system, which directs the flow of metal and helps minimize turbulence. Care must be taken to avoid inclusions and irregularities, ensuring that the casting is of high quality.
4. Cooling and Solidification
After pouring, the metal must cool and solidify. The cooling time can vary based on the size of the casting, the type of metal used, and the ambient conditions. During cooling, it is critical to monitor the temperature to prevent defects such as cracking or warping. Once solidification is complete, the sand mold is typically broken apart to reveal the cast component.
5. Finishing Processes
Following demolding, the cast part often requires additional finishing processes. This may include cleaning, grinding, and removing any excess material, known as flash. Surface treatments or coatings may also be applied to enhance the corrosion resistance and appearance of the finished product.
Conclusion
Sand casting is a pivotal technique in the manufacturing industry, noted for its flexibility in producing complex shapes and large components at a relatively low cost. The procedure encompasses several critical steps, from designing patterns to finishing the cast parts. Although modern technologies have introduced more advanced casting methods, sand casting remains a favored choice for many applications, owing to its unique advantages and capabilities. Understanding this process is essential for anyone involved in metalworking or manufacturing, as it lays the foundation for creating custom metal parts that meet a diverse range of industrial needs.
Post time:paź . 13, 2024 16:38
Next:resin bound sand