The Art and Science of Sand Casting
Sand casting is one of the oldest and most versatile manufacturing processes used to produce metal parts. With roots tracing back thousands of years, this method has undergone significant evolution while maintaining its fundamental principles. Whether it’s for crafting intricate jewelry or large industrial components, sand casting remains a foundational technique in metallurgy.
Understanding the Basics of Sand Casting
Sand casting involves creating a mold from sand and then pouring molten metal into the mold cavity. The sand mixture typically consists of silica sand, clay, and water, which help bind the sand grains together and provide the necessary strength and porosity. The process begins with the creation of a pattern, a replica of the object to be cast. This pattern is usually made from materials such as wood, metal, or plastic and is used to shape the sand into the desired form.
Once the pattern is created, it is placed in a flask—a container that holds the sand mixture. The flask is then filled with the sand and compacted around the pattern to create a mold. After the sand has solidified sufficiently, the pattern is removed, leaving a cavity in the shape of the desired part. The two halves of the mold are then reassembled, and molten metal is poured into the cavity through a sprue—a channel that allows the metal to enter.
Advantages of Sand Casting
One of the primary advantages of sand casting is its cost-effectiveness, particularly for small production runs. The materials used in sand casting are readily available and inexpensive. Additionally, the sand mold is relatively easy to create and modify, allowing for quick adjustments and prototyping.
Sand casting is also highly versatile. It can accommodate a wide range of metals, including aluminum, bronze, iron, and steel. This flexibility makes it suitable for various applications, from artistic sculptures to complex machinery parts. Moreover, sand casting can achieve complex geometries and intricate details, which may be challenging for other manufacturing processes.
Environmental Considerations
sand caste
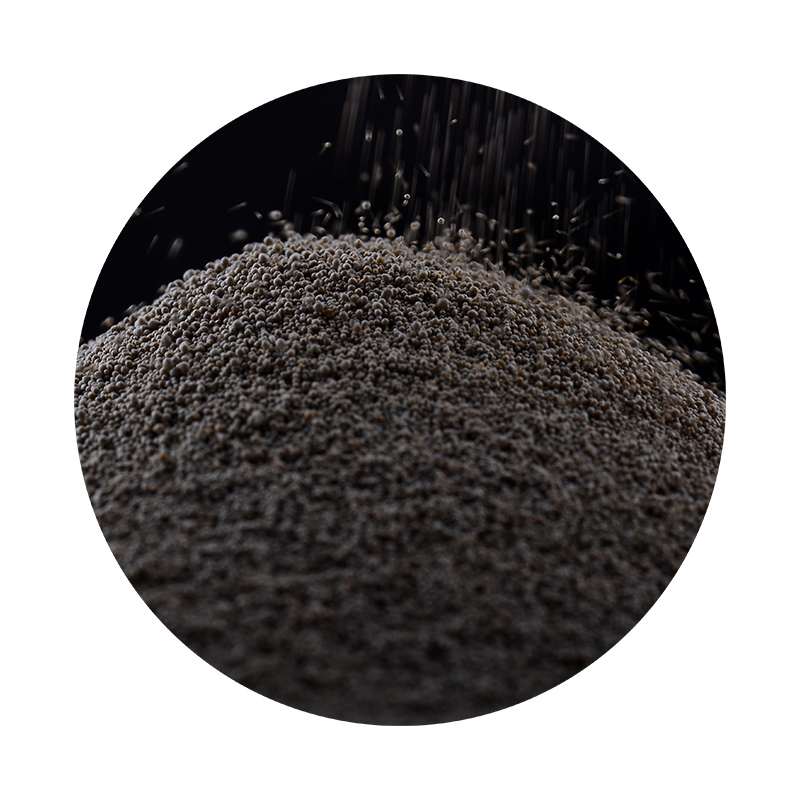
While sand casting offers numerous benefits, it is essential to address its environmental impact. The process generates waste material, particularly in the form of sand and scrap metal. However, many foundries now recycle sand and metal, reducing waste and promoting sustainability. Advances in technology have also contributed to minimizing emissions and improving the overall efficiency of the process.
The use of environmentally friendly binders and additives has been increasingly adopted to mitigate the environmental footprint of sand casting. Furthermore, the industry is exploring innovations such as 3D printing for mold creation, which can lead to enhanced precision and reduced material waste.
Innovations and Future Trends
As technology continues to evolve, so does the field of sand casting. Traditional methods are being complemented by advances in computer-aided design (CAD) and computer-aided manufacturing (CAM). These technologies allow for precise modeling and simulation of the casting process, which leads to better quality control and reduced defects.
Additive manufacturing (3D printing) is perhaps one of the most exciting developments in sand casting. By creating molds directly from digital files, manufacturers can significantly shorten lead times and lower costs. This innovation is especially beneficial for low-volume production, where traditional methods may not be economically viable.
The incorporation of smart technology, such as sensors and data analytics, is also transforming the industry. By monitoring various parameters during the casting process, manufacturers can optimize production conditions, resulting in higher-quality castings and improved operational efficiency.
Conclusion
Sand casting is a time-honored technique that has adapted to the changing needs of the manufacturing landscape. With its ability to produce complex parts at relatively low costs, it remains a vital part of modern metalworking. As the industry embraces new technologies and sustainable practices, sand casting is poised to continue thriving in a competitive global market. Whether for artistic expression or industrial production, the art and science of sand casting will undoubtedly play a crucial role in shaping the future of manufacturing.
Post time:paź . 17, 2024 12:17
Next:how much does sand casting cost