Open Sand Casting An Art and Science of Metalworking
Open sand casting, a traditional manufacturing process, has been integral to various industries for centuries. This method of casting involves pouring molten metal into a sand mold to create intricate shapes and components. Its versatility and effectiveness make it a favored technique for producing everything from small, intricate parts to large industrial components. In this article, we will explore the fundamentals of open sand casting, its advantages, applications, and some challenges faced in the process.
Understanding the Process
The open sand casting process begins with creating a mold from a mixture of sand, clay, and water. The sand particles are typically finer, allowing for better detail and surface finish. The mold consists of two halves the cope (top half) and the drag (bottom half). Once the mold is prepared, a pattern, usually made of metal, wood, or plastic, is placed in the sand to create a cavity for the molten metal.
After the pattern is removed, the two halves of the mold are assembled, and molten metal, often made from alloys such as aluminum, brass, or iron, is poured into the cavity. The metal is allowed to cool and solidify, after which the mold is broken away to reveal the cast component. The process's simplicity allows for rapid production and easy modifications for different designs.
Advantages of Open Sand Casting
One of the key advantages of open sand casting is its cost-effectiveness. Creating molds from sand is relatively inexpensive compared to other molding materials like metal. This economical aspect is particularly beneficial for low-volume production runs or one-off custom components. Moreover, the open nature of the process allows for easy access to the mold, which alleviates some complexities associated with mold removal seen in closed casting processes.
Additionally, the flexibility in design is remarkable. This method accommodates intricate shapes, large parts, and various sizes without requiring complex tooling modifications. The ability to create large components that would be challenging to manufacture with other casting methods makes open sand casting a go-to choice for industries like construction, automotive, and aerospace.
open sand casting
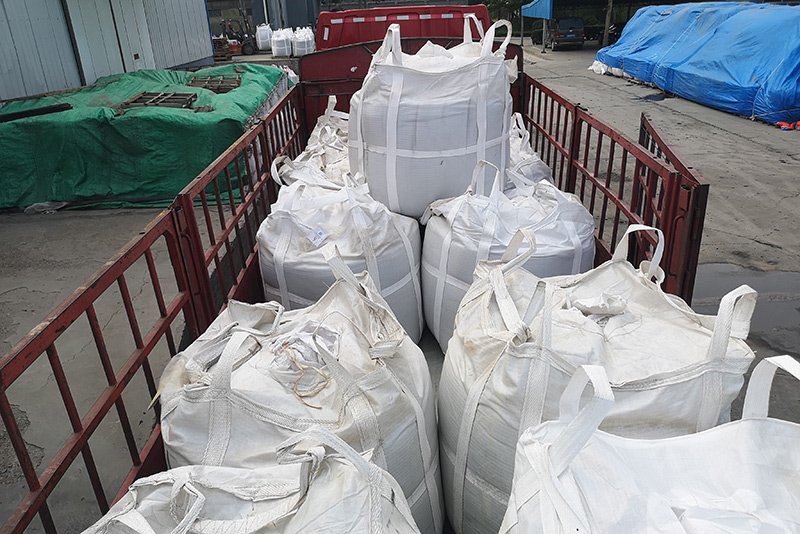
Applications of Open Sand Casting
Open sand casting finds applications across a myriad of industries. In the automotive sector, complex engine components, transmission casings, and various housings are often produced using this method. The aerospace industry also benefits from open sand casting techniques to fabricate parts that withstand high stress and temperature variations.
Moreover, traditional crafts and artisanal applications such as sculptures and decorative metalwork leverage sand casting as a means to realize unique artistic designs. Due to its adaptability, the method is often utilized in small foundries for prototypes or low-volume production where precision is key.
Challenges of Open Sand Casting
While there are many benefits to open sand casting, it is not without challenges. Surface finish often requires further refinement, as the sand may leave a rough texture on the final product. Furthermore, controlling the cooling rate of the molten metal is crucial to avoid defects like porosity and shrinkage, which can compromise the integrity of the cast part.
Another challenge is the environmental concern related to sand disposal and the use of binders, which can generate waste and contribute to pollution if not managed properly. As industries move toward sustainability, developing eco-friendly sand casting materials is becoming increasingly important.
Conclusion
Open sand casting stands as a testament to the enduring relevance of traditional manufacturing methods in a modern, technology-driven world. Despite its challenges, the process offers unmatched flexibility, cost-efficiency, and applicability across diverse industries. As advancements continue to shape the foundry landscape, open sand casting will undoubtedly remain a critical component in the evolution of metalworking, blending art and science to produce functional and aesthetic creations.
Post time:paź . 14, 2024 13:16
Next:wet sanding 3d prints