The Art and Science of Sand Casting
Sand casting, one of the oldest metal casting techniques, continues to play a vital role in various manufacturing processes today. This method is characterized by its versatility, cost-effectiveness, and ability to create intricate shapes that would be challenging to achieve using other methods. This article delves into the details of sand casting, exploring its process, advantages, applications, and some considerations for those interested in this craft.
The Sand Casting Process
The sand casting process begins with the creation of a mold. The primary material used for the mold is sand, typically mixed with a binding agent such as clay and water. The mixture is packed around a pattern, which is a replica of the object that needs to be cast. The pattern is usually made from metal, wood, or plastic and is designed to be removed from the mold once it has been formed.
After the pattern is removed, the mold is ready for the pouring process. Molten metal is carefully poured into the cavity of the mold. The metal can be anything from aluminum and bronze to iron, depending on the desired properties of the final product. Once the metal cools and solidifies, the mold is broken apart to reveal the casting.
Finishing processes may follow, including machining, to refine the dimensions and surface finish of the final product. These steps ensure that the casting meets the required specifications and quality standards.
Advantages of Sand Casting
One of the most significant advantages of sand casting is its ability to produce large and complex parts. The flexibility of sand molds allows for the creation of intricate shapes, which can be advantageous in industries such as automotive and aerospace. Additionally, the process can handle various metal types, making it suitable for many applications.
describe sand casting
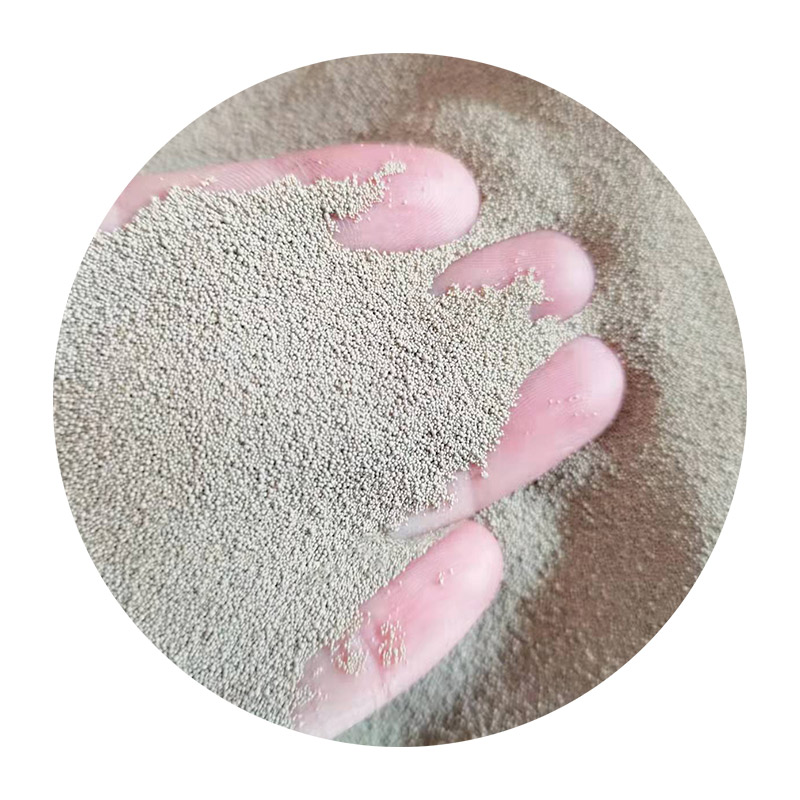
Moreover, sand casting is cost-effective for small production runs. The materials used are relatively inexpensive, and the process does not require expensive machinery compared to other casting methods, such as die casting or investment casting. This makes it an excellent choice for prototype development or small-scale production.
Applications of Sand Casting
The applications of sand casting are vast and diverse. It is widely utilized in industries such as automotive, where components like engine blocks, gearboxes, and other structural parts are commonly produced. Additionally, the aerospace sector benefits from this technique, as it allows for the creation of lightweight yet strong components.
Other applications include machinery parts, pipes, and even artistic sculptures. The versatility of sand casting enables it to be employed in various fields, including construction, manufacturing, and art.
Considerations in Sand Casting
While sand casting has numerous advantages, there are also some factors to consider. The surface finish of sand-cast products is typically rougher compared to other casting methods. This might necessitate additional finishing processes to achieve the desired surface quality. Furthermore, the dimensional accuracy may be less precise than other techniques, which can impact the performance of the final product.
In conclusion, sand casting remains a foundational technique in manufacturing, offering a unique blend of versatility, cost-effectiveness, and the ability to create complex shapes. Whether for industrial applications or artistic endeavors, the principles of sand casting continue to evolve, ensuring its relevance in modern manufacturing practices. For those interested in exploring this age-old method, understanding its processes and applications is the first step toward mastering the art and science of sand casting.
Post time:gru . 02, 2024 04:52
Next:Innovative Solutions for Fine Casting Sand in Modern Manufacturing Applications