Advantages of Lost Foam Casting
Lost foam casting (LFC) is an advanced metal casting process that offers numerous benefits over traditional casting methods. This technique, which involves creating a foam pattern that is coated with a ceramic shell, is particularly popular in industries that require high precision and complex geometries. Here, we’ll discuss the key advantages of lost foam casting that make it a preferred choice for manufacturers.
1. High Precision and Complex Shapes
One of the most significant advantages of lost foam casting is its ability to produce intricate designs with tight tolerances. The foam patterns can be sculpted to achieve complex shapes that would be difficult, if not impossible, to create using other methods like sand casting. This allows for the production of components with reduced weight and increased performance, making it ideal for applications in aerospace, automotive, and other high-tech industries.
2. Elimination of Draft Angles
In traditional casting processes, patterns must be designed with draft angles to facilitate their removal from molds. However, lost foam casting eliminates this requirement, as the foam pattern vaporizes during the casting process, leaving behind a mold cavity that precisely matches the desired shape. This not only simplifies the design process but also maximizes the material's usable volume, contributing to better yield and less waste.
3. Cost-Effectiveness
While the initial setup costs for lost foam casting may be higher compared to some conventional methods, its overall cost-effectiveness often surpasses initial concerns. This efficiency stems from several factors reduced material waste, minimized machining requirements, and the potential for shorter cycle times. Due to the high precision of the finished product, post-casting operations can be significantly reduced, which further drives down costs.
4. Reduced Material Waste
advantages of lost foam casting
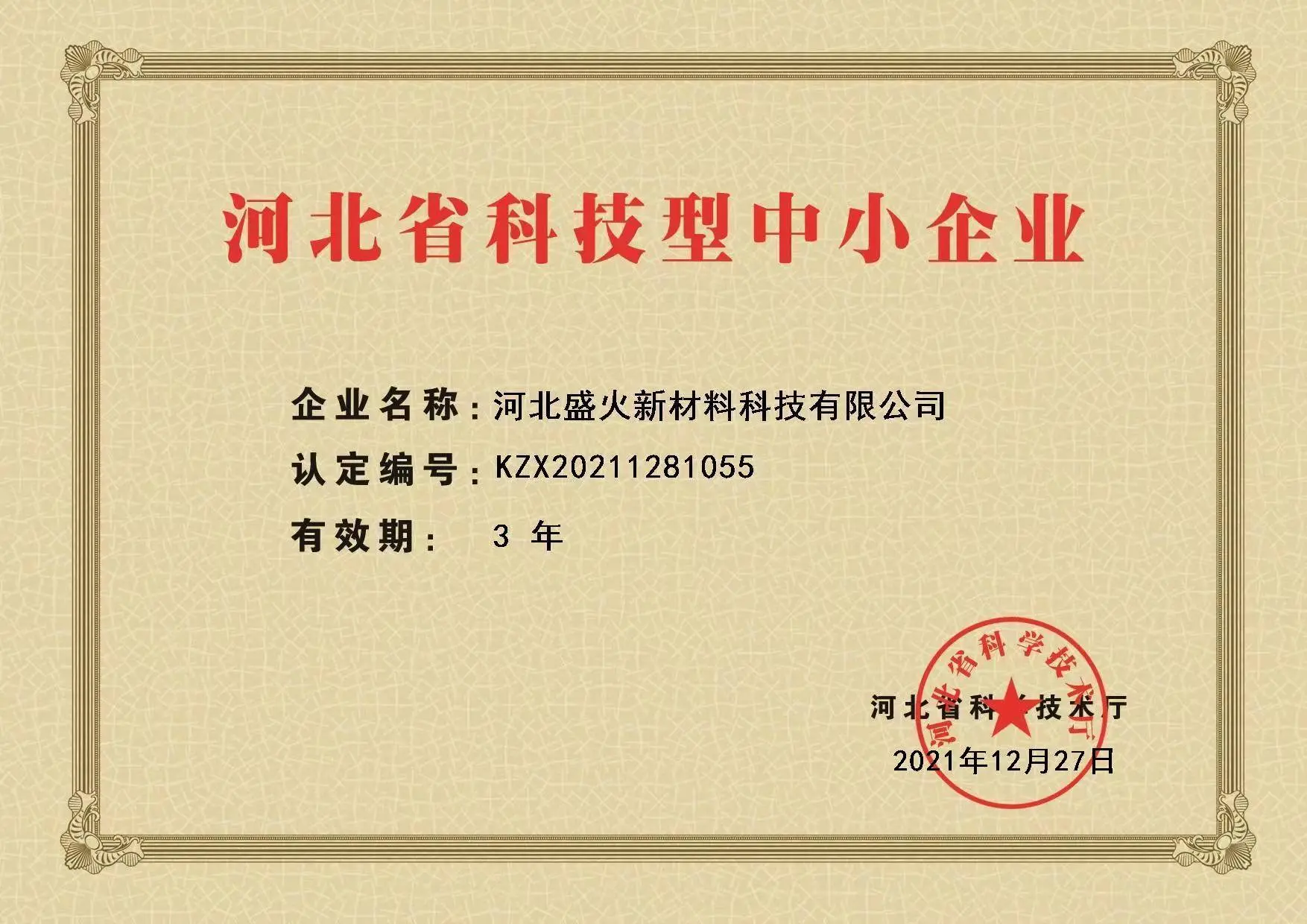
Lost foam casting contributes to more sustainable manufacturing by minimizing material waste. In traditional processes, large amounts of metal can be wasted during the machining stage. In contrast, LFC allows for the metal to be poured directly into a near-net shape cavity, resulting in less scrap material. Additionally, because the foam pattern is composed of polystyrene, which can be recycled, the entire process is more environmentally friendly.
5. Improved Surface Finish
The surface finish of cast parts produced through the lost foam process is often superior to that of parts produced through sand casting. The smoothness of the original foam pattern translates to a finer surface on the final metal product. This is particularly beneficial in applications where aesthetics are essential or where surface imperfections can affect performance.
6. Versatility in Materials
Lost foam casting is compatible with a wide variety of metals, including aluminum, iron, and various alloys. This versatility allows manufacturers to select materials that best meet the specific requirements of their applications, whether they demand high strength, lightweight characteristics, or resistance to corrosion. This adaptability makes LFC suitable for a wide range of industries, from heavy machinery to intricate artistic designs.
7. Simplified Process Flow
The lost foam casting process simplifies the manufacturing flow. The creation of foam patterns can often be done quickly, and the direct pouring of material into the mold reduces the steps typically associated with mold preparation. This streamlined process can lead to shorter lead times and increased production rates, allowing companies to respond more rapidly to market demands.
Conclusion
In summary, lost foam casting presents a multitude of advantages that make it an attractive option for modern manufacturing. High precision, the ability to create complex shapes, reduced waste, and improved surface finishes are just a few of the benefits that set this process apart from traditional methods. As industries continue to seek out innovative and efficient production techniques, lost foam casting stands out as a valuable manufacturing solution that can meet the challenges of contemporary demands.
Post time:paź . 21, 2024 07:38
Next:Leading Manufacturer of High-Quality Resin Coated Sand Solutions for Various Applications