Advantages and Disadvantages of Sand Casting
Sand casting is one of the oldest and most versatile metal casting processes, widely used in various industries for producing complex shapes. This technique involves creating a mold from sand and pouring molten metal into this mold to form the desired object. While sand casting offers several advantages, it also comes with certain disadvantages that must be considered. This article will explore both the pros and cons of sand casting to provide a balanced view of this manufacturing process.
Advantages of Sand Casting
1. Cost-Effectiveness One of the primary advantages of sand casting is its cost-effectiveness. The materials used, such as sand and clay, are relatively inexpensive and readily available. This makes sand casting an ideal choice for producing large quantities of parts without incurring high material costs.
2. Complex Shapes and Sizes Sand casting allows for the production of intricate designs and large components that other casting methods may struggle to produce. The versatility of sand molds enables manufacturers to create complex geometries, which is particularly beneficial for industries like automotive and aerospace, where intricate designs are common.
3. Flexibility in Metal Choice Sand casting can be used with various metals, including aluminum, bronze, iron, and steel. This flexibility allows manufacturers to select the most appropriate material for their specific application, which can enhance the performance and durability of the final product.
4. Reusability of Molds Although the sand molds are destroyed in the process of removing the finished object, they can often be reused for subsequent castings after some reconditioning. This aspect helps to reduce waste and can lower production costs further, especially for high-volume runs.
5. Large Production Capabilities Sand casting is particularly well-suited for producing large parts. Industries that require components such as engine blocks, pump housings, and large brackets benefit from the capability of sand casting to handle significant weights and dimensions.
6. Simplicity of Equipment The equipment required for sand casting is relatively simple and requires less investment compared to other casting methods. This simplicity makes it accessible for small-scale operations and hobbyists, as well as large manufacturers.
advantages and disadvantages of sand casting
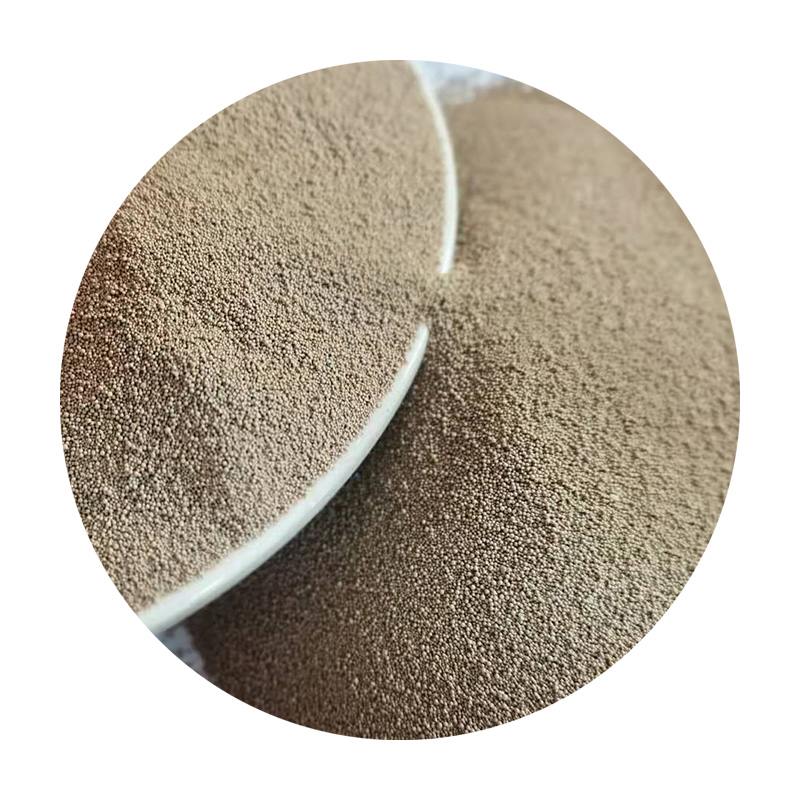
Disadvantages of Sand Casting
1. Surface Finish One of the notable disadvantages of sand casting is its rough surface finish compared to other casting methods like investment casting. Parts produced through sand casting may require additional machining or finishing processes to achieve a smoother surface, which can add to the overall production time and cost.
2. Dimensional Tolerances Sand casting typically has wider tolerances than other casting methods, which can affect the accuracy of the final product. While this may be acceptable for some applications, industries that demand precision engineering may find this limitation problematic.
3. Porosity Components produced through sand casting can sometimes exhibit porosity, which refers to small holes or voids within the metal. This can lead to potential weaknesses in the material and may require secondary processes to mitigate the issue, such as heat treatment or welding.
4. Labor-Intensive Process Preparing sand molds can be labor-intensive, requiring skilled workers to ensure the mold's quality. This reliance on manual labor can lead to inconsistencies in production and may result in longer lead times.
5. Environmental Concerns The sand casting process can have environmental impacts, particularly due to the use of binders and other additives that may not be eco-friendly. Additionally, the disposal of used sand can pose environmental challenges if not managed properly.
6. Limitations on Part Thickness The thickness of the parts produced through sand casting can be limited. Very thin sections can be difficult to cast effectively without risking defects such as warping or inadequate filling.
Conclusion
Sand casting is a time-honored manufacturing technique that has withstood the test of time due to its numerous advantages, such as cost-effectiveness, versatility, and the ability to produce large and complex parts. However, manufacturers must also consider its disadvantages, including surface finish issues, dimensional tolerances, and potential porosity. By weighing these factors, industries can better determine whether sand casting is the right choice for their specific needs and applications. Overall, understanding the pros and cons of sand casting can help businesses make informed decisions that align with their operational goals.
Post time:lis . 15, 2024 13:53
Next:lost foam casting coating