Why Sand Casting is Preferred An In-Depth Look at Its Advantages
Sand casting, a process that dates back thousands of years, has stood the test of time as one of the most popular methods for metal casting around the globe. It involves creating a mold from a mixture of sand and a binding agent and then pouring molten metal into the mold to create a desired shape. While various casting methods exist, sand casting remains a prevalent choice in both industrial and artisanal settings. So, why is sand casting preferred by so many manufacturers and metalworkers? Let’s explore the numerous advantages that contribute to its popularity.
1. Versatility in Applications
One of the foremost reasons sand casting is preferred is its versatility. The process can be used to produce a wide range of items, from large components such as engine blocks and heavy machinery parts to intricate designs for decorative items. Sand casting accommodates various metals, including aluminum, iron, and bronze, making it suitable for diverse industries such as automotive, aerospace, and art.
2. Cost-Effectiveness
Sand casting methods are often more cost-effective than other casting processes, especially for small to medium-sized production runs. The materials used for sand cores and molds are relatively inexpensive, and the equipment required is generally less complex. This makes it an appealing option for startups and small businesses that may not have substantial capital to invest in more expensive manufacturing processes.
3. Simplicity and Accessibility
The process of sand casting is relatively straightforward, making it accessible to engineers and artisans alike. With minimal technological requirements, small foundries can produce quality castings without the need for highly specialized machinery. This simplicity leads to reduced production times and makes it easier for businesses to enter the market and start producing their products quickly.
In sand casting, creating molds can sometimes be done on-site, which significantly reduces lead times. Traditional methods may require longer schedules due to the extensive tooling and setup processes, whereas sand molds can be quickly formed and ready for casting. This responsiveness is increasingly valuable in today’s fast-paced market, where demand can change rapidly.
why sand casting is preferred
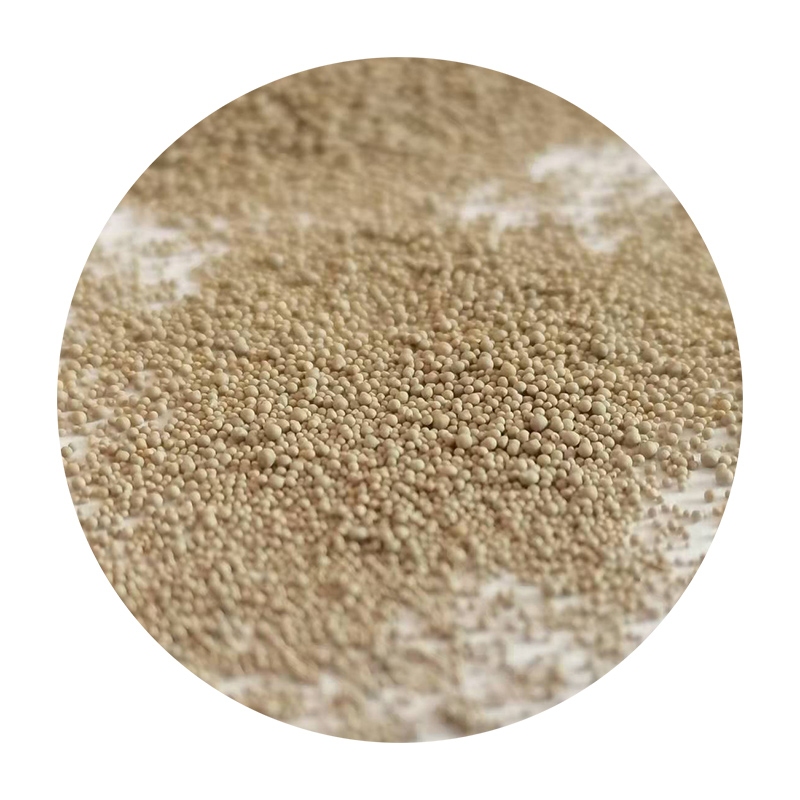
5. Tolerance and Surface Finish
Modern sand casting techniques have evolved to provide improved tolerances and surface finishes. While traditionally known for rougher textures, advancements in sand casting machinery and methods have led to enhanced dimensional accuracy and finer surface finishes. This ability to meet tighter tolerances can reduce the need for expensive secondary machining processes, further decreasing production costs.
6. Environmentally Friendly Options
Sand casting can also be an environmentally friendly manufacturing option. Many foundries now use reclaimed sand, reducing waste and the need for new raw materials. Additionally, the energy consumption during the sand casting process is generally lower compared to other methods like die casting or investment casting, making it a more sustainable choice in an era increasingly concerned with ecological impacts.
7. Ability to Produce Complex Shapes
One of the highlights of sand casting is its capability to create complex shapes and geometries. The pliability of the sand allows for intricate designs that might be challenging or impossible to achieve with other casting processes. This process can accommodate undercuts and other detailed features that enhance a product's aesthetics and functionality.
8. Localized Production
Sand casting promotes localized production, which can be beneficial from both economic and environmental perspectives. By establishing foundries close to where the components are needed, companies can minimize transportation costs and carbon footprints. This localized approach can also foster regional economies and provide job opportunities.
Conclusion
With its myriad advantages, sand casting has proven to be an indispensable process in metalworking. Its versatility, cost-effectiveness, simplicity, and ability to produce intricate designs make it a go-to method for many manufacturers and artisans. Moreover, its evolving technologies and improved efficiencies coupled with environmentally friendly practices position sand casting favorably in a modern context. As industries continue to seek reliable and efficient manufacturing solutions, sand casting remains a preferred choice that balances tradition with innovation.
Post time:ਅਕਤੂਃ . 02, 2024 04:04
Next:Achieving a Smooth Finish on Ceramic Surfaces through Effective Sanding Techniques