What is Sand Casting in Engineering?
Sand casting is one of the oldest and most widely used metal casting processes in manufacturing. It involves creating a mold from a mixture of sand and a bonding agent, which is then used to pour molten metal to create various shapes and structures. This method is particularly popular due to its versatility, ease of use, and cost-effectiveness. In this article, we will explore the principles of sand casting, its advantages and disadvantages, and its applications in engineering.
The Sand Casting Process
The sand casting process consists of several key steps
1. Pattern Creation The first step involves creating a pattern of the object that needs to be cast. This pattern is usually made from a material such as wood, plastic, or metal and is a replica of the final product. Patterns can be made in different types, such as solid, split, or cope-and-drag patterns, depending on the complexity of the design.
2. Mold Making After the pattern is created, the next step is to make the mold. This involves placing the pattern into a prepared box known as a flask, which is then filled with a mixture of sand and a binder (commonly clay or resin). The sand is compacted around the pattern to form a mold cavity. Once the sand has set, the pattern is removed, leaving a hollow impression that mirrors the shape of the original object.
3. Core Making (if required) For hollow parts, additional cores made of sand are often used. Cores are placed inside the mold cavity to create internal features. The cores must also be made and dried before the set of the mold is prepared.
4. Melting and Pouring After the mold is prepared, the next step involves melting the metal to be cast—often aluminum, steel, or iron—at high temperatures. Once the metal is molten, it is poured into the mold cavity. Careful attention is needed during this step to avoid defects such as air pockets or spills.
5. Cooling After the molten metal is poured into the mold, it is allowed to cool and solidify. The cooling time depends on the metal type and the thickness of the casting.
6. Mold Removal Once the metal has cooled and solidified, the mold is broken away to reveal the cast part. Excess sand is removed, and the cast object is cleaned and finished as required.
Advantages of Sand Casting
Sand casting has several advantages that make it a popular choice among engineers and manufacturers
what is sand casting in engineering
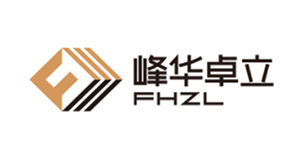
- Versatility This method can be used to cast a wide variety of materials and complex shapes, making it suitable for different engineering applications
.- Cost-Effectiveness The materials needed for sand casting are relatively inexpensive, and the process can be carried out without the need for extensive, high-cost equipment, making it ideal for small and large production runs.
- Scale Production Sand casting is effective for both small-scale projects and mass production, as patterns can be reused multiple times.
- Tolerance and Surface Finish While some sanding and finishing may be required, the cast parts can have favorable tolerances and surface finishes when done correctly.
Disadvantages of Sand Casting
Despite its many advantages, sand casting does have its limitations
- Surface Finish The surface finish of sand cast parts may not be as smooth as those produced by other methods (e.g., investment casting). Additional finishing operations may be required.
- Defect Risk Common casting defects, such as shrinkage cavities and gas porosity, can occur if the process is not carefully controlled.
- Labor-Intensive Some steps of the process may require significant manual labor, which can impact production times and labor costs.
Applications in Engineering
Sand casting is widely used in various engineering fields, including automotive, aerospace, heavy machinery, and construction. Examples of components that are often produced using sand casting include engine blocks, transmission cases, and various structural components. The ability to create complex shapes and the adaptability of the process to different metals makes sand casting a fundamental technique in engineering.
In conclusion, sand casting remains an essential technique in the realm of engineering and manufacturing. Its blend of cost-effectiveness, versatility, and capability to produce intricate shapes makes it invaluable in producing critical components across many industries. Understanding the principles and processes behind sand casting can lead to further innovations and improvements within the field, guiding future advancements in manufacturing technologies.
Post time:ਨਵੰ. . 19, 2024 04:59
Next:Innovative Techniques in 3D Printing with Sand for Advanced Manufacturing