Types of Sand Casting Processes
Sand casting, one of the oldest and most versatile manufacturing processes, involves forming an object by pouring molten metal into a mold made from sand. This method is widely used for producing intricate shapes and components in various materials, particularly metals. The process can be broken down into several types based on various criteria such as the type of sand used, the molding technique, and the application. Here, we explore the most common types of sand casting processes.
1. Green Sand Casting
Green sand casting is perhaps the most traditional and widely used type of sand casting. This process utilizes a mixture of silica sand, clay, and water, creating a mold that retains moisture and is soft enough for easy manipulation. The term green refers to the moist state of the sand, not the color. The advantages of green sand casting include low cost, good flowability, and relatively easy reclamation of sand after use.
In this process, patterns made from various materials, such as metal or plastic, are pressed into the green sand to form molds. Once the mold is prepared, molten metal is poured in and allowed to solidify. After cooling, the mold is broken to retrieve the cast object. Green sand casting is especially popular in the production of automotive components, machinery parts, and artworks due to its flexibility and low setup cost.
Unlike green sand casting, dry sand casting uses a mold made from sand that has been mixed with a binder and cured to create a hard mold. This type of casting is particularly beneficial for parts that require a high degree of dimensional accuracy and a smooth surface finish.
The dry sand mold is produced by drying the sand mixture, which hardens it, allowing for finer details and better surface quality. Dry sand casting is often used for applications in architectural elements, precision components in machinery, and decorative items. While more expensive and time-consuming than green sand casting, its advantages make it suitable for high-quality production.
3. No-Bake Sand Casting
types of sand casting process
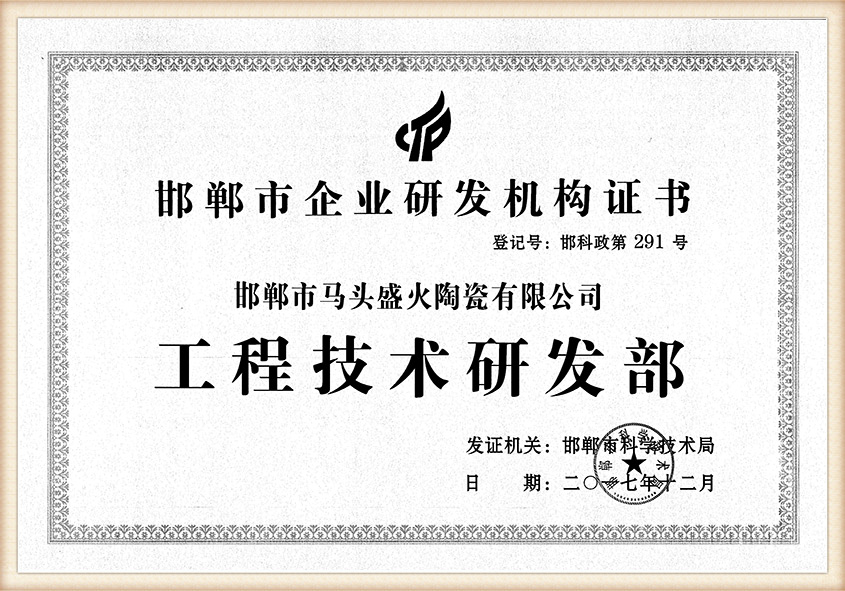
No-bake sand casting, also known as air-set or chemical-cured sand casting, employs a mixture of sand with a chemical binder that sets at room temperature without the need for heating. This technique allows for the creation of highly intricate molds that do not collapse under the weight of the molten metal, making it ideal for larger castings.
In no-bake sand casting, the pattern is removed and the two halves of the mold are assembled without the use of high heat, which means that the casting can be produced in complex shapes with excellent surface finishes. This method is particularly effective for making heavy machinery parts and large components, often found in construction or automotive industries.
4. Lost Foam Casting
Lost foam casting, while not a traditional sand casting method, incorporates sand casting principles with a unique approach. In this process, a foam pattern is coated with a sand mixture, and the entire setup is then heated. The heat vaporizes the foam, leaving a mold cavity that can be filled with molten metal.
This method allows for complex shapes and reduces the need for additional machining, as the surface finish is smoother and the dimensional accuracy is enhanced. Lost foam casting is widely used for making intricate components in aerospace and automotive applications.
5. Precision Sand Casting
Precision sand casting encompasses various techniques that aim to improve the precision and surface finish of cast components. Techniques like investment casting or the use of high-grade sand are employed to achieve tighter tolerances and better surface quality. This type is particularly beneficial for industries requiring strict compliance with tolerances and surface finishes, such as medical devices and high-performance automotive parts.
Conclusion
The versatility and adaptability of sand casting processes make them a fundamental part of modern manufacturing. Each type of sand casting process has its own advantages and is suitable for various applications depending on the requirements of size, detail, and surface finish. As technology advances, the methods of sand casting continue to evolve, providing better capabilities and efficiencies for manufacturers across different industries.
Post time:ਨਵੰ. . 09, 2024 08:51
Next:Is it possible to send a 3D print through the mail?