Types of Sand Casting
Sand casting is one of the oldest and most versatile metal casting processes in the manufacturing industry. It involves pouring molten metal into a sand mold to produce intricate parts and components. The process is favored for its ability to create complex shapes and its cost-effectiveness. Various types of sand casting techniques have been developed, each suited for different applications and materials. This article explores the major types of sand casting and their applications.
1. Green Sand Casting
Green sand casting is the most common type of sand casting process. It uses a mixture of sand, clay, and water to create a mold that is soft and permeable. The term green refers to the mold being in a damp state rather than the color. This technique allows for quick setup and production, making it ideal for high-volume manufacturing. Green sand molds can be reused multiple times, which contributes to its economic efficiency. Industries typically use this casting method for producing iron, aluminum, and steel parts.
2. Dry Sand Casting
Dry sand casting, as the name suggests, utilizes a mold that is made from sand mixed with a binder that hardens when heated. This method produces stronger molds compared to those used in green sand casting. The heated sand molds can withstand higher temperatures, making them suitable for casting metals with higher melting points. The dry sand process is particularly advantageous for producing intricate details and achieving tighter tolerances on cast components. This technique is often employed in applications such as automotive parts and heavy machinery components.
3. Sodium Silicate Sand Casting
types of sand casting
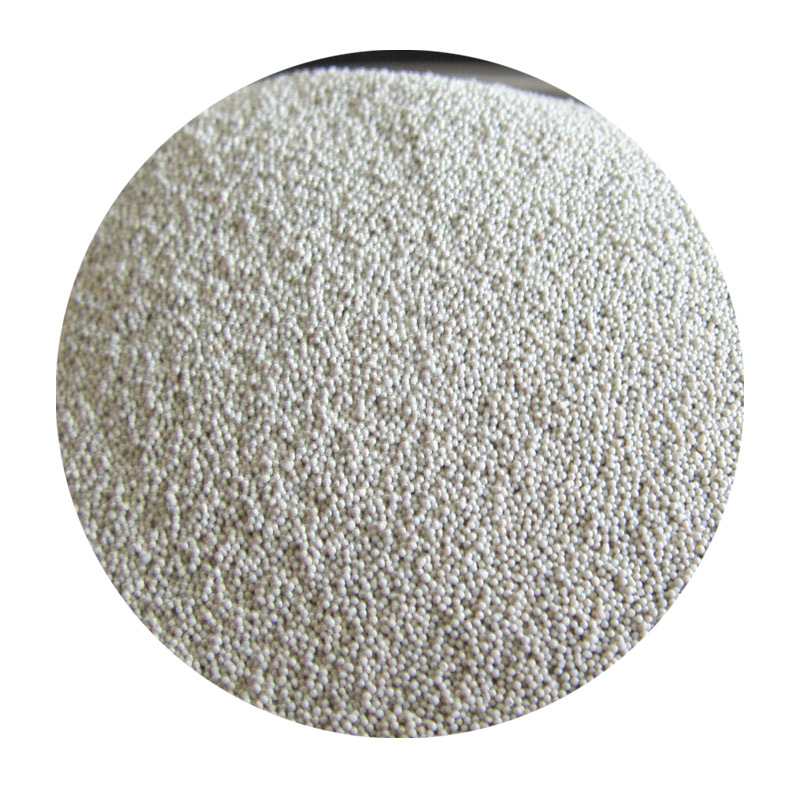
Sodium silicate sand casting, also known as water glass sand casting, utilizes a mixture of sand and sodium silicate as a binder. This process involves using CO2 gas to harden the mold, resulting in a very durable mold structure. Sodium silicate molds have low thermal expansion, which minimizes casting defects due to mold deformation. This method is suitable for producing high-precision parts that require a high surface finish. Sodium silicate sand casting is often used in industries like aerospace and electronics where precision is critical.
4. Shell Sand Casting
Shell sand casting is a process that involves creating thin molds made from a mixture of sand and thermosetting resin. This technique enables the production of thinner and more intricate molds compared to traditional sand casting methods. The molds are formed by heating a pattern covered with the sand-resin mixture, causing the resin to bond and solidify into a shell. Shell casting is highly suitable for producing complex shapes with excellent surface finishes. It is widely used in industries where detailed designs are essential, such as in the production of intricate automotive and appliance components.
5. C02 Sand Casting
C02 sand casting, similar to sodium silicate casting, uses a binder combined with sand. In this process, carbon dioxide gas is introduced to the sand mixture, causing it to harden. This method produces rigid molds that maintain high consistency and dimensional accuracy. CO2 sand casting is particularly effective for producing components that require high levels of precision and can effectively handle large production volumes. This technique is often used in manufacturing industrial valves and other critical mechanical components.
Conclusion
Sand casting is a pivotal technology in the manufacturing realm, with various methods catering to specific needs for versatility, precision, and efficiency. From the common green sand casting to more specialized techniques like shell sand casting and sodium silicate casting, each type has its unique advantages and applications. As industries continue to evolve, advancements in sand casting processes are likely to enhance production capabilities, improve quality, and reduce costs. Understanding the types of sand casting allows manufacturers to choose the appropriate method for their specific projects, leading to better outcomes in product design and manufacturing efficiency.
Post time:ਨਵੰ. . 05, 2024 19:50
Next:cerabead