Stainless Steel Sand Casting A Comprehensive Overview of a Modern Foundry Technique
In the realm of manufacturing and engineering, stainless steel sand casting has emerged as a pivotal process for producing intricate and durable metal components. This contemporary technique combines traditional practices with modern advancements, creating a robust method adopted across various industries, including automotive, aerospace, and industrial machinery.
What is Stainless Steel Sand Casting?
At its core, stainless steel sand casting is a process in which molten stainless steel is poured into a sand mold to create the desired shape. This method is characterized by several advantages, including its ability to produce high-quality and intricate shapes with excellent dimensional accuracy. Unlike other casting methods, sand casting allows for the production of large and heavy components while maintaining reasonable costs.
The Sand Casting Process
The sand casting process can be broken down into several key steps, namely pattern creation, mold preparation, pouring, and finishing.
1. Pattern Creation The first step involves creating a pattern that mirrors the final product. Patterns are typically made from high-strength materials such as metal or plastic and are designed to compensate for shrinkage that occurs during cooling.
2. Mold Preparation Once the pattern is ready, it is placed within a frame filled with a mixture of sand and bonding agents. The sand is compacted around the pattern to create a mold. After compacting, the pattern is removed, leaving a cavity in the shape of the desired part.
3. Pouring With the mold established, molten stainless steel is then poured into the cavity. The pouring must be executed with precision to ensure that the mold is filled adequately, preventing defects like cold shuts or misruns.
4. Cooling and Finishing After pouring, the molten metal cools and solidifies. Once fully cooled, the sand mold is broken away, revealing the cast stainless steel part. Final finishing processes such as machining, surface treatment, and inspection are often applied to ensure the part meets the stringent industry standards.
stainless steel sand casting foundry
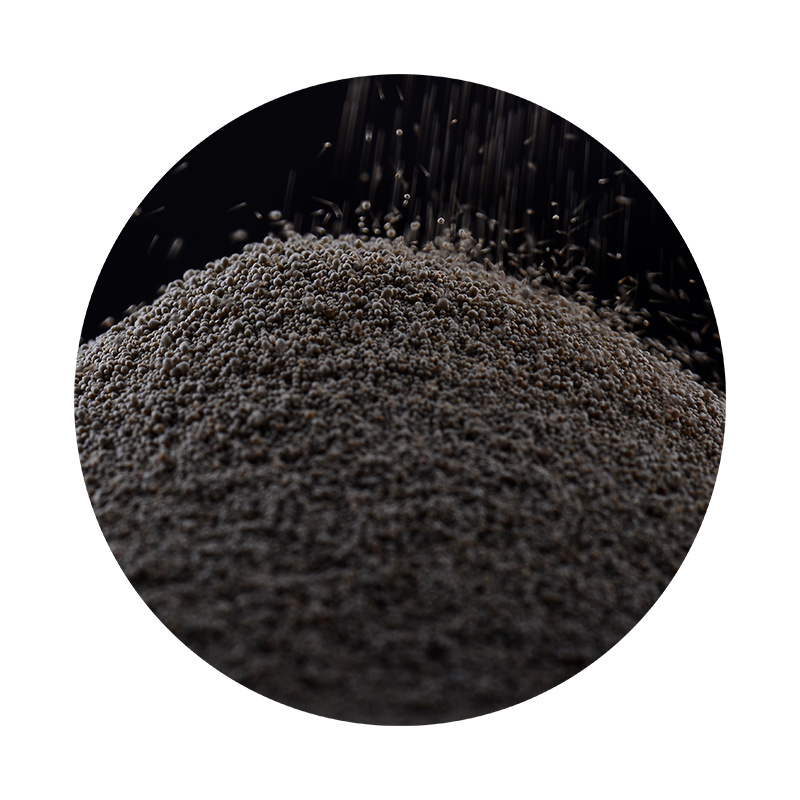
Advantages of Stainless Steel Sand Casting
1. Versatility One of the standout features of stainless steel sand casting is its versatility. It can be used to manufacture a wide range of parts, including complex geometries that would be challenging with other methods. This adaptability makes it a preferred choice for many industries.
2. Cost-Effectiveness The sand casting process is relatively cost-effective, especially for medium to large production runs. The reusable nature of sand molds reduces the overall material costs, and the reduced need for extensive machining minimizes labor costs.
3. Quality and Durability Stainless steel is renowned for its resistance to corrosion and oxidation, making it an excellent material choice for components that are exposed to harsh environments. Additionally, the sand casting process can produce high-quality parts with excellent mechanical properties.
4. Reduction of Waste As the process allows for the reuse of sand, it significantly reduces waste compared to other casting methods. This eco-friendly approach aligns with modern manufacturing's sustainability goals.
Applications of Stainless Steel Sand Casting
The applications of stainless steel sand casting are vast. Industries such as automotive rely on cast steel components for exhaust systems, brackets, and housing. In aerospace, lightweight yet strong components are critical for performance and safety; hence, stainless steel castings are commonly utilized. Furthermore, industrial machinery often incorporates cast parts due to their ability to endure high pressures and extreme conditions.
Conclusion
Stainless steel sand casting is a technological marvel that combines age-old casting techniques with modern ingenuity, producing essential components across various sectors. Its versatility, cost-effectiveness, and ability to deliver durable parts make it a cornerstone of modern manufacturing. As industries continue to evolve, so too will the techniques and technologies surrounding stainless steel sand casting, ensuring it remains relevant and effective for years to come. The ongoing innovation within foundries will likely lead to advancements that enhance precision, reduce environmental impact, and improve overall production efficiency. Whether for intricate aerospace parts or sturdy industrial components, stainless steel sand casting will undoubtedly play an integral role in shaping the future of manufacturing.
Post time:ਨਵੰ. . 18, 2024 21:44
Next:Incorporating Sand into Resin for Enhanced Aesthetic and Structural Properties