The Sand Foundry A Cornerstone of Modern Manufacturing
The sand foundry, a pivotal element of modern manufacturing, is a fascinating realm where raw materials are transformed into intricate metal components. This process, steeped in tradition, combines art and science, resulting in products that serve countless industries, from automotive to aerospace and beyond.
At the heart of sand foundry operations lies the use of sand as the primary molding material. Foundries utilize various types of sand, with silica sand being the most prevalent due to its desirable properties, such as durability and fine grain. The molding process begins with the creation of a mold, which is composed of two halves that encase a pattern of the desired object, typically made from metal or plastic. The sand is mixed with a binding agent, such as resin or clay, to ensure that it retains its shape once compacted around the pattern.
One of the most significant advantages of sand casting is its versatility. Foundries can produce components of varying shapes and sizes, ranging from small parts to large castings weighing several tons. This adaptability makes sand casting an attractive option for manufacturers, allowing for low production costs and minimal waste. Furthermore, the process can accommodate a wide array of metals, including aluminum, iron, and bronze, enhancing its usability across different sectors.
sand foundry
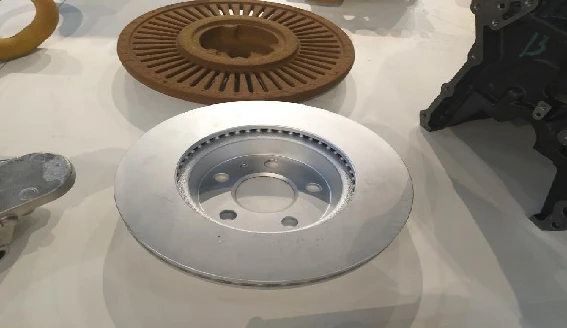
The sand foundry process begins with the design and fabrication of a mold. Once the pattern is placed in the sand, it is compacted to create a negative impression. After both halves of the mold are prepared, the casting material, typically molten metal, is poured into the cavity. The heat from the molten metal causes the sand to solidify around it as it cools. Once the metal has set, the mold is broken apart to unveil the finished cast. This method, while simple in concept, requires precision and expertise to ensure the quality and integrity of the final product.
Safety and environmental considerations are also critical in modern sand foundry operations. With advancements in technology, foundries have developed systems to mitigate the release of pollutants and to recycle spent sand. Additionally, the implementation of automation and digital technologies has enhanced efficiencies, ensuring that foundries remain competitive in the ever-evolving manufacturing landscape.
As industries increasingly demand customized solutions and rapid production cycles, the sand foundry continues to evolve. Innovations such as 3D printing of sand molds and the use of advanced materials are paving the way for faster, more accurate, and environmentally-friendly production processes.
In conclusion, the sand foundry remains a cornerstone of modern manufacturing, presenting a blend of traditional craftsmanship and modern technology. As the world continues to advance, the foundry's ability to adapt and innovate will be critical in meeting the growing demands of various industries, securing its relevance in the manufacturing landscape for years to come. The future of sand foundries holds great promise, ensuring that they will continue to shape the world, one cast at a time.
Post time:ਅਕਤੂਃ . 04, 2024 22:08
Next:Sanding Techniques for Achieving Smooth Finishes on Glazed Ceramics