Understanding Sand Castings A Comprehensive Overview
Sand casting is one of the oldest and most widely used metal casting processes in the manufacturing industry. It is a versatile method that enables the production of intricate shapes and large components with a relatively low cost, making it an attractive option for many applications. In this article, we will delve into the sand casting process, its advantages, challenges, and applications.
The sand casting process begins with the creation of a mold. This is typically done by packing sand around a pattern that represents the end product. The pattern is usually made from a durable material such as metal or plastic and is designed to withstand the pressure of the sand. After the sand is packed firmly around the pattern, the two halves of the mold are separated, and the pattern is removed, leaving a cavity that corresponds to the desired part shape.
Understanding Sand Castings A Comprehensive Overview
Once the mold is prepared, molten metal is poured into the cavity. The metal is usually heated to a specific temperature to ensure it flows smoothly and fills the mold completely. Common metals used in sand casting include aluminum, iron, and bronze. After the metal has cooled and solidified, the mold is broken open, and the cast part is removed. This is followed by various finishing processes, which may include sandblasting, machining, or heat treatment to achieve the required dimensional accuracy and surface finish.
sand castings
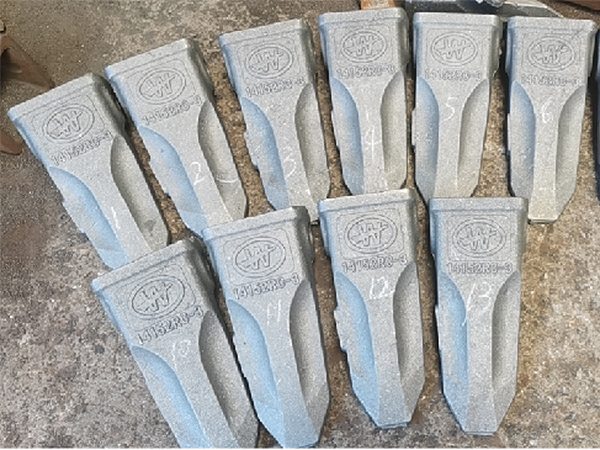
One of the most significant advantages of sand casting is its flexibility. It can accommodate a wide range of sizes—from small intricate components to large heavy parts, making it suitable for various industries, including automotive, aerospace, and construction. Furthermore, sand casting molds can be easily modified to produce different designs without significant changes in tooling.
However, sand casting also comes with its challenges. One major concern is the permeability of sand molds, which can lead to defects such as gas porosity if the sand does not allow trapped gases to escape during solidification. Additionally, the finish quality of sand castings may not be as smooth as that of other casting techniques, necessitating additional finishing processes to meet specific standards.
Despite these challenges, sand casting remains a popular choice due to its affordability and the ability to create complex shapes. The process is continually evolving, with advancements in technology improving the accuracy and efficiency of sand casting operations. Innovations such as 3D printing of patterns are starting to change the landscape of sand casting, allowing for even more intricate designs with reduced lead times.
In conclusion, sand casting is a time-honored technique that continues to play a vital role in modern manufacturing. Its unique combination of versatility, cost-effectiveness, and the ability to produce complex shapes makes it an indispensable method for various applications. As technology progresses, the sand casting process will likely see further improvements, securing its place in the future of metal manufacturing.
Post time:ਨਵੰ. . 08, 2024 18:14
Next:fine casting sand