Understanding Sand Casting A Fundamental Foundry Process
Sand casting, a pivotal process in metalworking, is known for its versatility, cost-effectiveness, and ability to produce intricate shapes. This age-old technique, dating back to ancient times, forms the backbone of modern foundry practices and continues to play a crucial role in various industries, from automotive to aerospace.
The Basics of Sand Casting
The sand casting process involves creating a mold from sand to form metal parts
. The essential steps of sand casting include pattern making, molding, pouring, and finishing.1. Pattern Making The process begins with the creation of a pattern, which is a replica of the desired part. Patterns are typically made from materials like wood, metal, or plastic. They must accurately represent the dimensions of the final product, accounting for shrinkage that occurs when metal cools.
2. Molding Once the pattern is ready, it is placed in a mixture of sand and a binder. The mixture is compacted around the pattern to form a mold. A common type of sand used is silica sand, due to its heat resistance and ability to hold its shape. The mold is then split into two halves, known as cope (top) and drag (bottom), allowing for easy removal of the pattern.
3. Pouring After the mold is prepared and the pattern removed, molten metal is poured into the mold cavity. The choice of metal depends on the application and can include aluminum, iron, or bronze. The pouring process must be carefully controlled to avoid defects such as air pockets or misruns.
4. Cooling and Finishing Once the molten metal has cooled and solidified, the sand mold is broken away, revealing the cast part. The finishing process may include grinding, machining, or surface treatment to achieve the desired surface finish and dimensions.
sand casting foundry process
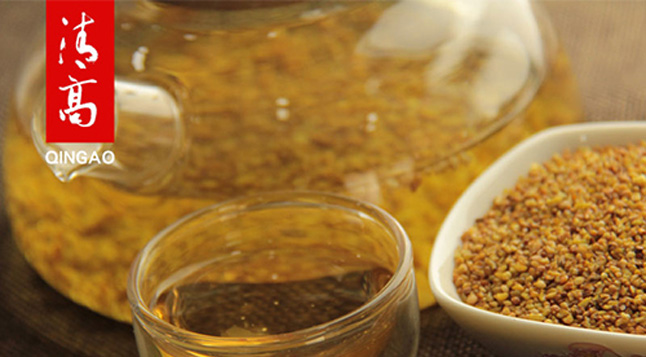
Advantages of Sand Casting
One of the main advantages of sand casting is its ability to produce large parts and complex geometries at a relatively low cost. The flexibility of sand as a material allows for the creation of smooth contours and fine details. Additionally, the process is suitable for a variety of metals and can be adapted for small-scale crafts as well as large industrial applications.
Another significant benefit is the reusability of sand. After being used, the sand can be cleaned and reprocessed for future molds, making the process more sustainable. This aspect is particularly important in today’s environmentally-conscious landscape, where minimizing waste is paramount.
Applications of Sand Casting
Sand casting finds application in various sectors. The automotive industry predominantly utilizes sand casting for engine blocks, transmission housings, and other components. Aerospace manufacturers also rely on sand-cast parts for their lightweight and strength characteristics. Moreover, the process is important in creating hardware, plumbing fittings, and artistic sculptures.
Challenges and Considerations
While sand casting is a robust method, it is not without its challenges. The smoothness of the mold affects the quality of the final part; therefore, excessive surface roughness can lead to additional machining costs. Controlling the pouring temperature and minimizing gas entrainment are also critical to achieving high-quality castings.
In conclusion, sand casting is an integral component of the foundry process that combines traditional craftsmanship with modern manufacturing techniques. Its ability to produce diverse and intricate components at a low cost continues to make it a favored choice across numerous industries. As technology progresses, innovations in sand casting are likely to enhance its efficiency and effectiveness, ensuring that it remains relevant in the evolving landscape of metal production.
Post time:ਨਵੰ. . 20, 2024 14:44
Next:why is sand casting used