Sand Casting Definition and Overview
Sand casting, also known as sand mold casting, is one of the oldest and most versatile metal casting processes. This method uses a sand-based mold to shape molten metal into the desired form. It is a widely employed technique in manufacturing industries due to its cost-effectiveness, suitability for complex shapes, and ability to produce large components.
The Process of Sand Casting
The sand casting process begins with the creation of a pattern, which is a replica of the final product. Patterns are typically made from materials such as wood, metal, or plastic. Once the pattern is completed, it is positioned within a sand mixture, known as mold sand. This mixture primarily consists of silica sand, clay, and water, which work together to bind the particles.
The sand is compacted around the pattern to create a mold. In most cases, two halves, or cope and drag, are made to form a complete mold. After the sand is compacted, the pattern is removed, leaving a cavity that reflects the shape of the component to be cast. To prevent the molten metal from sticking to the sand, the interior surface of the mold is typically coated with a release agent.
Following the mold preparation, the next step involves melting the metal. Common metals used in sand casting include aluminum, bronze, iron, and various alloys, each chosen based on the mechanical properties required for the final product. The molten metal is then poured into the mold cavity through a pouring system, often designed to minimize turbulence, which could lead to defects.
Once the metal has cooled and solidified, the mold is broken apart to reveal the cast part. This process typically involves hand tools or mechanical devices to separate the sand from the metal. The resulting component is now a solid metal object, but it usually requires further finishing processes to achieve the desired surface quality and dimensional accuracy.
Advantages of Sand Casting
sand casting definition
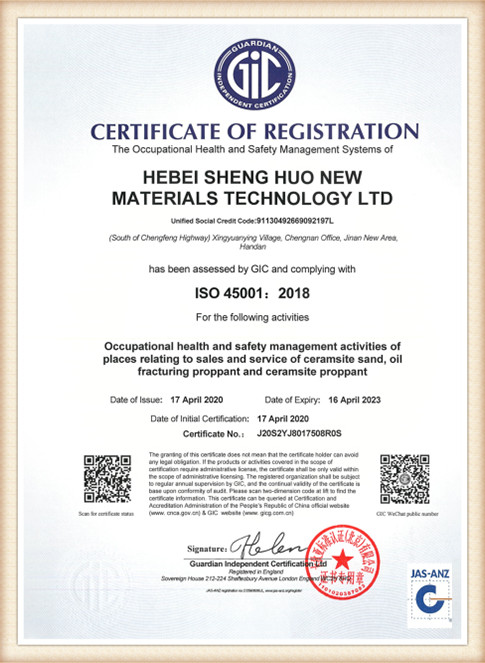
One of the most significant advantages of sand casting is its flexibility in producing parts of various sizes and complexities. It can accommodate intricate designs, making it suitable for a broad range of applications from artistic sculptures to automotive and aerospace components. Additionally, the sand used in the process is relatively inexpensive, which helps reduce production costs, especially for large batches.
Another benefit is the ability to easily modify patterns and molds. Changes can be made without significant alterations in tooling, allowing for quick adaptations to design changes or prototypes. Furthermore, the sand casting process is highly scalable, permitting both small-scale and large-scale production runs.
Considerations and Limitations
Despite its advantages, sand casting does have some limitations. The surface finish of sand cast parts may not be as smooth as those produced by other methods, such as investment casting. This can necessitate additional finishing treatments, which can add to production time and costs. Additionally, the dimensional tolerances achievable with sand casting may not be as tight as those achieved through other processes.
Another challenge is related to the quality of the sand used. Contaminants or variations in sand composition can lead to defects such as inclusions or porosity in the final product. Therefore, meticulous attention must be given to material selection and mold preparation.
Conclusion
In conclusion, sand casting remains a prominent method in manufacturing due to its unique advantages, including cost-effectiveness and design flexibility. While it does have some limitations, the versatility and wide applicability of sand casting in various industries make it an invaluable process for producing metal components, continuing to hold its ground even in the face of advanced casting technologies.
Post time:ਦਸੰ. . 02, 2024 00:08
Next:golden sanda