Understanding Sand Casting Definition and Process
Sand casting, a widely utilized metal casting process, involves the use of sand as the primary mold material. This method has stood the test of time, being one of the oldest and most versatile forms of metal casting available. The significant advantages of sand casting, including its cost-effectiveness and adaptability for various metal alloys, have made it a preferred choice in many industrial applications.
Definition of Sand Casting
At its core, sand casting is a process where molten metal is poured into a mold formed from sand to create a desired shape. The mold is created by compacting sand around a pattern, which serves as a replica of the final product. Typically, this pattern is made from metal, plastic, or wood and is designed to exact specifications. After the mold is formed, the pattern is removed, leaving a hollow cavity into which molten metal is introduced. Once the metal cools and solidifies, the mold is dismantled to reveal the finished product.
The Sand Casting Process
The sand casting process can be broken down into several key steps
1. Pattern Making The first step involves creating a pattern that represents the object being cast. The pattern must include allowances for shrinkage, machining, and surface finish. Accurate patterns are crucial as they directly affect the quality of the final casting.
2. Mold Creation The pattern is placed in a molding box, and sand mixed with a binding agent is compacted around it. This process can be accomplished either by hand (for smaller or more intricate molds) or using machines (for larger scale productions). After the sand has been compacted, the pattern is removed, leaving behind a cavity that will receive the molten metal.
3. Metal Melting The next step is melting the metal to be cast. Depending on the desired material properties, various metals can be used, including iron, aluminum, bronze, and magnesium. The metal is heated in a furnace until it reaches a liquid state, ensuring it is at the appropriate temperature to fill the mold correctly.
sand casting definition
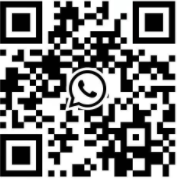
4. Pouring the Metal Once the metal is molten, it is carefully poured into the prepared mold cavity. This stage needs to be controlled to prevent defects such as air pockets, which can compromise the integrity of the casting.
5. Cooling and Solidification After pouring, the molten metal is allowed to cool and solidify within the mold. The cooling rate can significantly affect the properties of the metal, such as strength and grain structure.
6. Mold Removal After the metal has fully cooled, the sand mold is broken away to reveal the cast object. This step is often referred to as shakeout. Depending on the complexity of the casting, this might require additional equipment or labor.
7. Finishing The final step involves cleaning and finishing the castings. This can include removing any excess sand, trimming, machining, or applying surface treatments to enhance the appearance and performance of the casting.
Advantages of Sand Casting
One of the primary benefits of sand casting is its flexibility. It can accommodate virtually any geometric shape, which makes it ideal for creating intricate designs and large components. Moreover, sand casting is suitable for a variety of metals, allowing manufacturers to choose the best material for their specific needs. Other advantages include relatively low costs compared to other casting methods, ease of setup, and a high level of customization.
Conclusion
In summary, sand casting is a vital process in metalworking that combines simplicity, versatility, and cost-effectiveness. It allows for the production of complex shapes and is adaptable to various metals, making it indispensable in industries ranging from automotive to aerospace. Understanding the fundamentals of sand casting is crucial for anyone involved in metallurgy or manufacturing, providing insight into one of the foundational techniques of metal fabrication.
Post time:ਅਕਤੂਃ . 20, 2024 02:00
Next:sanding ceramic mug