Metal Sand Casting An Overview
Metal sand casting is a traditional and widely utilized method for producing metal parts and components through the process of casting. This approach is characterized by its use of sand as the mold material, making it versatile and adaptable for various metal types, including iron, aluminum, brass, and steel. With a history that spans thousands of years, sand casting remains popular due to its cost-effectiveness and ability to create intricate shapes with relative ease.
The Basics of Sand Casting
The sand casting process begins with creating a mold from a pattern, which is typically a replica of the desired final product. The pattern can be made from wood, metal, or plastic, and it is designed to allow for a slight contraction of the metal as it cools. Once the pattern is prepared, it is embedded in a mixture of sand and a bonding agent, often clay. This sand mixture is packed around the pattern to form the mold. The bonding agent helps the sand grains to stick together, maintaining the mold's shape during the casting process.
After the mold is created, it is separated from the pattern, producing a negative impression of the desired part. The mold is then assembled and prepped for pouring. In many cases, cores made of sand are added to create internal features or hollow sections in the cast part.
Pouring the Metal
The next step in the sand casting process is to heat the chosen metal until it reaches a molten state. The molten metal is then carefully poured into the mold through a runner system, which directs the flow of metal and helps to minimize air pockets. One of the advantages of sand casting is its ability to handle large volumes of metal, making it suitable for both small batch production and large casting runs.
As the metal fills the mold, it begins to cool and solidify. The cooling process varies depending on the type of metal involved and the design of the mold. Once the metal has completely solidified, the mold is broken apart to reveal the finished casting.
Finishing Processes
metal sand casting
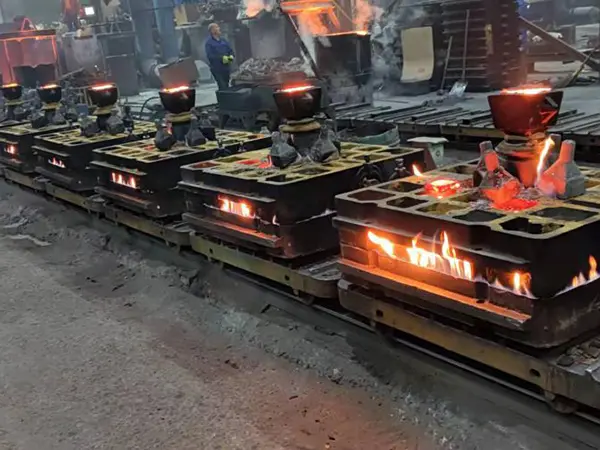
Although sand casting can produce complex shapes and good dimensional accuracy, the resulting castings often require additional finishing. Common finishing processes include grinding, sanding, and machining to achieve the desired surface finish and tolerances. Occasionally, heat treatment may also be applied to enhance the mechanical properties of the metal.
Advantages of Sand Casting
One of the primary advantages of metal sand casting is its cost-effectiveness, especially for low to medium production runs. The materials used in sand casting are relatively inexpensive, and the process does not require advanced machinery. This makes sand casting an attractive option for small businesses and workshops.
Moreover, sand casting is highly versatile, capable of producing intricate shapes and a wide range of sizes—from small components to large industrial parts. It is also suitable for a variety of metals, which allows manufacturers to tailor their casting processes based on specific industry demands.
Challenges and Considerations
Despite its benefits, sand casting also has its challenges. The quality of the mold can significantly impact the final product, with factors such as mold material and packing density affecting the casting's precision and surface finish. Additionally, the sand mold can be less durable compared to other mold types, leading to potential issues with repeatability and consistency in mass production scenarios.
Environmental considerations have also come into play, with various regulations emerging regarding the types of binders and additives used in sand casting. Manufacturers need to adapt their processes to comply with environmental standards while maintaining production efficiency.
Conclusion
In summary, metal sand casting is a time-honored manufacturing process that continues to thrive in modern industries. Its flexibility, cost-effectiveness, and ability to produce complex geometries ensure its relevance in today’s manufacturing landscape. As technology advances and environmental considerations grow, the sand casting industry will likely evolve, incorporating new materials and techniques to enhance the process further. Whether for small workshops or large industrial facilities, sand casting remains a vital resource for producing high-quality metal parts.
Post time:ਅਕਤੂਃ . 12, 2024 16:09
Next:supersand