Making Sand Castings A Comprehensive Guide
Sand casting, one of the oldest and most versatile metal casting processes, plays a crucial role in the manufacturing industry. It is a method where molten metal is poured into a sand mold to create complex shapes. This article will explore the intricacies of sand casting, covering its materials, processes, and applications.
What is Sand Casting?
Sand casting, also known as sand mold casting, involves creating molds from sand particles bonded together with clay, moisture, or chemical binders. The process can accommodate a wide variety of metals, including aluminum, iron, bronze, and brass, making it an ideal choice for producing metal parts of various shapes and sizes.
The Process of Sand Casting
The sand casting process can be broken down into several key steps
1. Pattern Making The first step involves creating a pattern, which serves as a replica of the final product. Patterns are typically made from materials such as wood, metal, or plastic. They are designed slightly larger than the actual size of the finished part to account for shrinkage that occurs when metal cools and solidifies.
2. Mold Preparation The next step is to prepare the sand mold. The sand mixture is composed of silica sand, clay, and water. The mixture is packed around the pattern to form a mold. Care needs to be taken to ensure that the mold is sufficiently compact and free of defects.
3. Core Creation For hollow components, cores made of sand are often required. Cores are inserted into the mold to create internal cavities, which are essential for certain designs. Similar to the mold, cores are also created using sand mixtures and are positioned within the mold before the metal is poured.
4. Pouring the Metal Once the mold is prepared and cores are in place, it’s time to pour the molten metal. The metal is heated to its melting point, often in a furnace, and then carefully poured into the mold through a sprue or pouring cup. This step demands precision to avoid defects such as cold shuts or misruns.
make sand casting
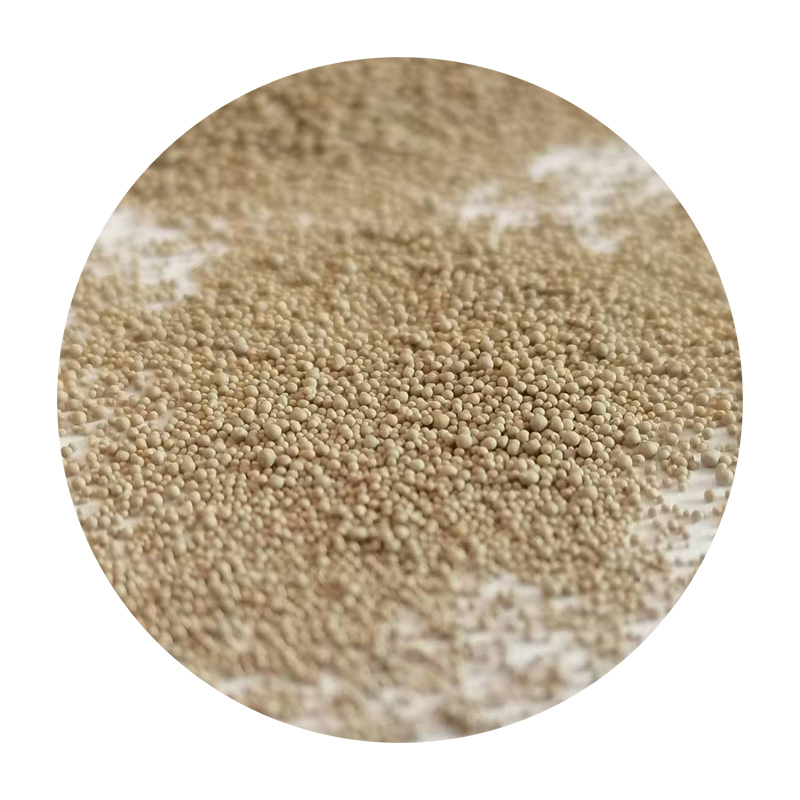
5. Cooling and Solidification After the metal is poured, it takes some time to cool and solidify within the mold. The cooling time depends on the size and thickness of the casting. Once the metal has completely solidified, the mold is broken apart to reveal the casting.
6. Finishing Operations The final step involves cleaning the casting. This includes removing sand from the surface, trimming excess material, and conducting any additional machining processes required to achieve the desired finish and tolerances.
Advantages of Sand Casting
Sand casting offers several benefits that make it a preferred manufacturing technique
- Versatility It can accommodate large and complex shapes, with relatively low tooling costs. - Material Variety A wide range of metals and alloys can be used, allowing for flexibility in design and application. - Cost-Effectiveness Especially for low to medium production volumes, sand casting is often less expensive than other casting methods.
Applications of Sand Casting
Sand casting is widely used across various industries for producing components like automotive parts, machinery, and industrial equipment. Due to its ability to produce intricate designs, it is also favored in artistic applications, where detailed metalwork is required.
Conclusion
Making sand castings is a fascinating blend of art and engineering, rooted in centuries of tradition. The process requires skill, precision, and an understanding of materials. As industries continue to evolve, sand casting remains a relevant and valuable technique, proving essential for both mass production and unique, custom projects. Whether in a modern factory or a traditional workshop, the fundamental principles of sand casting continue to shape the way metal parts are made today.
Post time:ਦਸੰ. . 17, 2024 03:39
Next:Exploring the Timeless Elegance of Heath Ceramics Sand Collection for Modern Interiors