Low Pressure Sand Casting An Innovative Approach for Precision Casting
Low pressure sand casting is a remarkable advancement in the foundry industry, combining traditional sand casting methods with innovative technology to produce high-quality metal components with enhanced precision and reduced defects. This casting technique has gained popularity in various industries, particularly in automotive, aerospace, and machinery, where the demand for lightweight, complex parts is ever-increasing.
The Process of Low Pressure Sand Casting
The low pressure sand casting process begins with the creation of a pattern, typically made of metal or other durable materials, which reflects the final dimensions of the desired part. This pattern is then covered with a mixture of sand and a bonding agent. The sand is compacted to form a mold, which can withstand the pressure exerted during casting. Unlike traditional sand casting, where gravity is the primary force for metal flow, low pressure sand casting employs a controlled low-pressure environment, usually ranging from 0.1 to 0.5 bar (approximately 1.5 to 7 psi).
In this method, molten metal is introduced into the mold at low pressure, allowing it to flow into intricate sections and fill cavities that might be challenging to achieve with standard methods. Once the mold is filled, the pressure ensures that the metal solidifies uniformly, reducing the likelihood of defects, such as porosity, shrinkage, and inclusions. After cooling, the sand is removed, revealing a finished cast that often requires minimal machining.
Advantages of Low Pressure Sand Casting
1. Enhanced Quality The primary advantage of low pressure sand casting is the production of components with superior mechanical properties. The controlled pressure helps in achieving a denser casting with fewer voids and better surface finishes, resulting in parts that are more durable and reliable.
2. Complex Geometries This method excels at creating complex and intricate shapes that would be difficult to fabricate using other casting techniques. The ability to produce detailed designs opens new avenues for engineering innovations, particularly in lightweight high-performance components.
low pressure sand casting
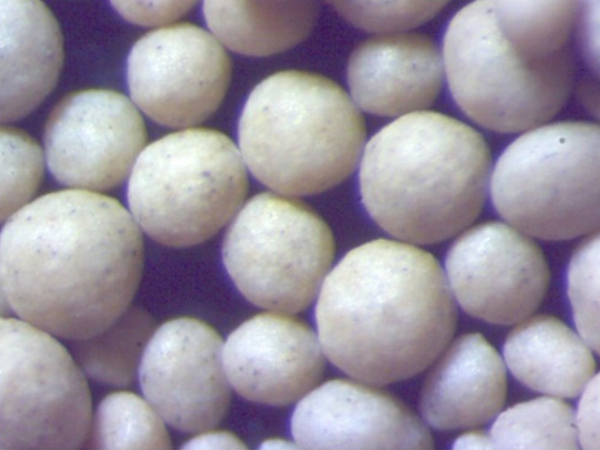
3. Cost-Effective Although initial setup costs can be higher compared to traditional methods, low pressure sand casting can lead to significant savings in the long run. The reduction in scrap rates, combined with the ability to use recycled sand, contributes to lower production costs.
4. Flexibility in Production Low pressure sand casting is suitable for both small and large production runs. It enables manufacturers to switch between different designs and patterns with relative ease, making it an attractive option for businesses looking for versatility in their manufacturing processes.
5. Environmentally Friendly This process often utilizes eco-friendly materials, including recycled sand. The lower energy consumption associated with the casting process also contributes to a smaller carbon footprint, aligning with current industry trends focused on sustainability and reducing waste.
Applications and Future Trends
Low pressure sand casting is widely used in sectors that require high-strength and lightweight components — particularly in automotive parts like engine blocks, transmission cases, and structural components. In aerospace, it is increasingly utilized for creating intricate turbine parts and structural elements that must withstand extreme conditions.
As industries continue to evolve, the future of low pressure sand casting looks promising. Advancements in materials science and automation technology are likely to further enhance production efficiency and quality. Additionally, the integration of digital technologies in mold design and simulation may soon allow for even greater optimizations in the casting process.
In conclusion, low pressure sand casting represents a pivotal shift in manufacturing, offering numerous benefits that cater to the modern demands of high-performance, precision engineering. Its blend of tradition and innovation positions it as a key player in the ongoing evolution of casting technologies.
Post time:ਨਵੰ. . 04, 2024 21:36
Next:sand cast