Lost Foam Metal Casting An Innovative Approach to Precision Casting
Lost foam metal casting is a sophisticated and innovative manufacturing process that has gained significant traction in recent years, particularly in industries requiring high precision and complex geometries. It combines traditional sand casting techniques with modern advancements, providing manufacturers with a highly efficient method for producing intricate components with excellent surface finishes.
At its core, lost foam casting involves the creation of a foam pattern that serves as a mold for the final metal product. This method is noteworthy because, rather than using a solid mold, the foam pattern is placed directly into the casting material, which is typically a mixture of sand and binder. When molten metal is poured into the mold, it vaporizes the foam, leaving behind a cavity that precisely replicates the foam pattern. The end result is a metal casting that perfectly captures the design of the original pattern.
One of the distinct advantages of lost foam casting is its ability to produce complex shapes with minimal machining. The process allows for the production of intricate designs that would be difficult or impossible to achieve using traditional casting methods. This capability significantly reduces the need for post-casting machining, ultimately lowering production costs and time. Industries such as aerospace, automotive, and even art, have embraced lost foam casting for these reasons.
Another significant benefit of this casting method is its excellent dimensional accuracy. Because the foam pattern is designed to fit the exact specifications required for the final product, there is a high degree of certainty that the resulting metal casting will match these specifications closely. This precision is critical in applications where components must fit together perfectly, such as in engine parts or architectural elements.
lost foam metal casting
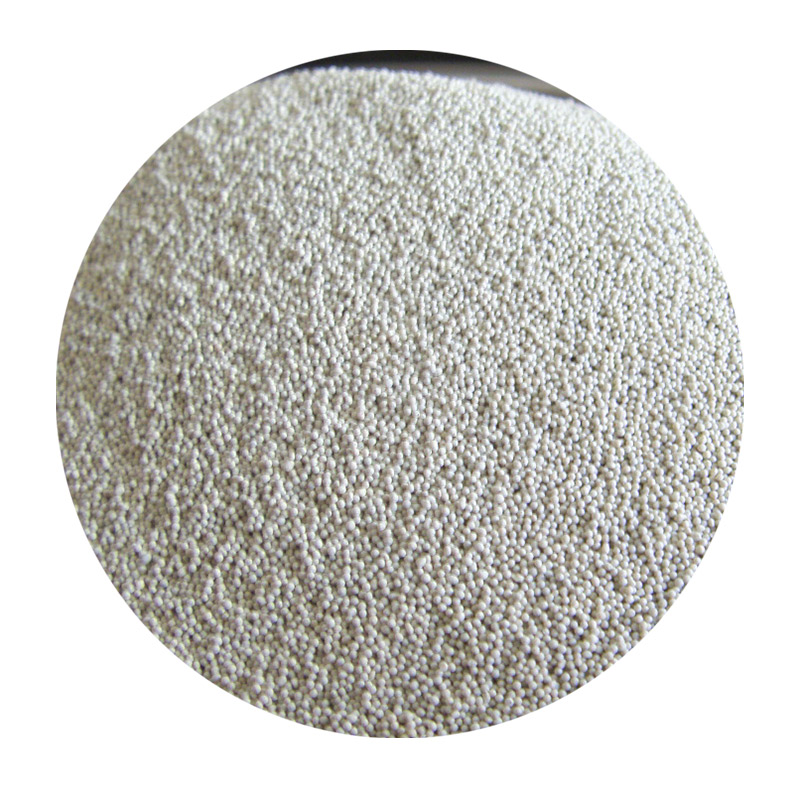
In addition to precision, lost foam casting also provides a superior surface finish compared to traditional sand casting methods. The smooth surface of the foam pattern is transferred to the final metal component, requiring less post-processing to achieve a high-quality finish. This not only saves time and resources but also enhances the aesthetic appearance of the finished product.
Sustainability is another aspect where lost foam casting shines. The process typically uses polystyrene or other eco-friendly materials that can be recycled or repurposed. Furthermore, because the foam is vaporized during casting, there are fewer waste materials resulting from the process. Manufacturers are increasingly recognizing the importance of sustainable practices, and lost foam casting aligns well with these goals.
However, the lost foam casting process is not without its challenges. One of the primary issues that can arise is the control of the vaporization process. If the molten metal is poured too quickly, it can create turbulence, leading to defects in the final casting. Therefore, careful control over the pouring speed and temperature is crucial to ensure a successful outcome. Additionally, the choice of materials, both for the foam pattern and the casting medium, can significantly impact the quality of the final product.
Despite these challenges, ongoing research and development are addressing these issues, leading to advancements in lost foam technology. Improvements in materials and techniques are continually enhancing the reliability and effectiveness of the process. As industries seek to produce more complex, precise, and aesthetically pleasing components, lost foam metal casting is poised to grow in popularity.
In summary, lost foam metal casting represents a cutting-edge solution for manufacturers seeking high precision and efficiency in their production processes. With its ability to produce complex geometries, excellent surface finishes, and reduced waste, it meets the demands of modern manufacturing while aligning with sustainability goals. As advancements continue to emerge, it is likely that lost foam casting will play an increasingly critical role in the future of metal casting and manufacturing overall. For businesses aiming to stay competitive in an increasingly complex market, embracing techniques like lost foam casting may very well be the key to achieving innovation and success.
Post time:ਨਵੰ. . 08, 2024 10:50
Next:Benefits of Lost Foam Casting in Modern Manufacturing Processes