Lost Foam Casting Method An Innovative Approach to Metal Casting
Lost foam casting is a revolutionary method in the field of metal casting, gaining popularity due to its efficiency, precision, and ability to produce complex shapes. This technique involves creating a foam pattern that is encased in a refractory material, which is subsequently filled with molten metal. The foam evaporates during the casting process, leaving behind a precise metal replica of the original pattern. This article explores the intricacies of the lost foam casting method, its advantages, applications, and future prospects.
At the heart of the lost foam casting process lies the foam pattern, typically made from polystyrene or other similar materials. The process begins with shaping the foam into the desired component using various fabrication techniques. Once the pattern is created, it is coated with a fine layer of a refractory material, often a mixture of sand and resin. This coating serves as a mold, providing the necessary strength and thermal insulation to withstand the molten metal.
One of the most significant advantages of lost foam casting is its ability to produce intricate designs that traditional casting methods struggle to replicate. The foam patterns can be easily shaped into complex geometries, allowing for the production of parts with elaborate features, such as internal passages and undercuts. This capability reduces the need for additional machining and tooling, leading to cost savings and shorter lead times.
Another remarkable benefit of the lost foam casting method is its high dimensional accuracy. As the molten metal fills the mold, it conforms closely to the foam pattern, resulting in minimal shrinkage and a superior surface finish. This accuracy not only enhances product quality but also reduces material waste, making the process environmentally friendly. Furthermore, because the foam evaporates rather than being removed, there’s no need for secondary operations typically required in conventional casting.
lost foam casting method
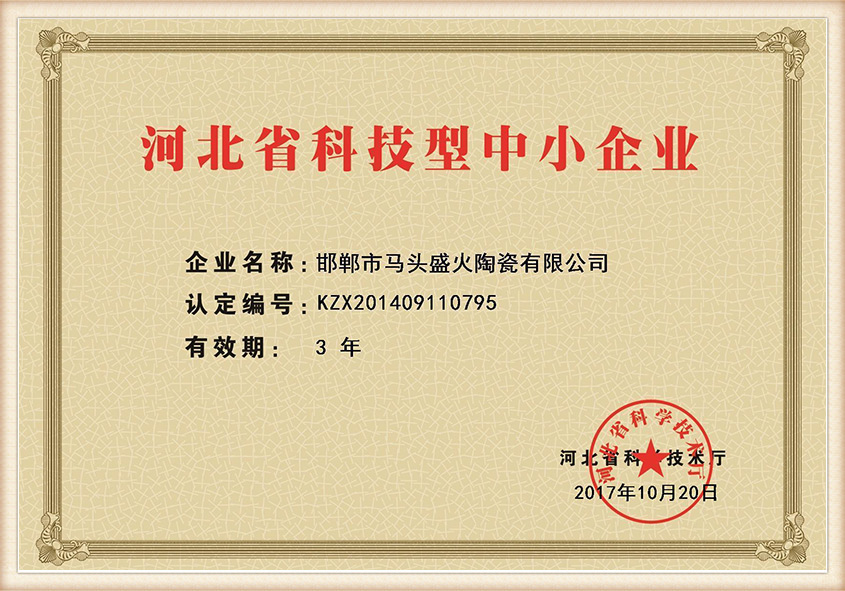
Lost foam casting finds its applications across various industries. It is particularly popular in the automotive sector for producing engine blocks, cylinder heads, and intricate components that demand high precision. The aerospace industry also benefits from this method, utilizing it for components that require lightweight yet durable materials. Additionally, lost foam casting is utilized in manufacturing artistic sculptures and architectural elements where detail is paramount.
Despite its numerous advantages, the lost foam casting process is not without challenges. Control over the expansion and contraction of foam patterns during heating is critical, as any failure in this regard can lead to defects in the final casting. Moreover, the initial investment in equipment and the production of foam patterns may be higher compared to traditional methods. However, as technology advances, solutions to these challenges are continually being developed.
Looking ahead, the future of lost foam casting appears promising. Innovations in materials and automation technology are likely to enhance the efficiency and scalability of the process. Additionally, as industries increasingly prioritize sustainability, the reduced material waste and energy efficiency of lost foam casting will make it an attractive option.
In conclusion, the lost foam casting method represents a significant advancement in the metal casting industry. Its ability to produce complex shapes with high precision and minimal waste positions it as a pragmatic choice for various applications. As the demand for intricate and lightweight components continues to grow, lost foam casting is poised to play an increasingly vital role in the manufacturing landscape.
Post time:ਅਕਤੂਃ . 31, 2024 10:31
Next:sanding resin