Lost Foam Casting Coating Enhancing Precision and Quality
Lost foam casting (LFC) is an innovative metal casting process that provides unparalleled precision and flexibility in creating complex geometries. Central to its success is the coating used during the process, which plays a crucial role in determining the final quality of the cast product. This article explores the significance of the coating in lost foam casting, its composition, application, and implications for various industries.
Understanding Lost Foam Casting
In lost foam casting, a foam pattern made of polystyrene is coated with a refractory material before being placed in a mold. The foam is then vaporized when molten metal is poured into the mold, leaving behind a precise replica of the original pattern. This process eliminates the traditional methods of creating metal forms, resulting in fewer steps and minimized material waste. The coating is an essential step that ensures the integrity and surface quality of the final product.
Function of the Coating
The primary function of the coating in lost foam casting is to provide a protective barrier that helps to retain the shape of the foam pattern while also facilitating the transition of molten metal. This coating must withstand high temperatures and prevent any chemical reactions between the molten metal and the foam. In addition to protecting the pattern, the coating aids in capturing fine details, thus enhancing the surface finish of the final product.
Common Coating Materials
The coatings used in lost foam casting are typically composed of various materials, including silica, alumina, and ceramic compounds. These materials are chosen for their thermal resistance, abrasion properties, and adhesion capabilities. A common formulation includes a mixture of fine sand and a bonding agent, which forms a robust layer around the foam pattern.
Moreover, coating materials can be tailored based on the specific requirements of the metal being cast, such as aluminum, iron, or steel. The composition can also be adjusted for special applications, such as high-strength automotive components or intricate industrial parts.
lost foam casting coating
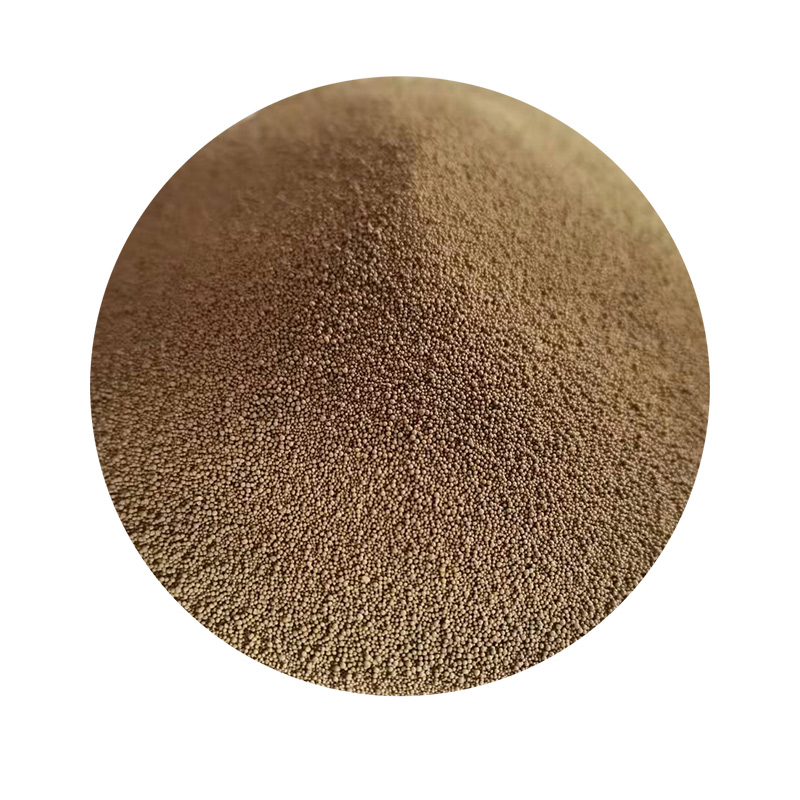
Application Techniques
The application of the coating can be achieved through several techniques, including dipping, spraying, or brushing. Each method has its advantages, depending on the complexity and size of the foam pattern. Dipping ensures an even coverage and is commonly used for smaller patterns, while spraying is more suitable for larger and more intricate geometries that require precision in coating thickness.
One emerging trend in the application of coatings is the use of advanced technologies like robotic spraying systems and automated dipping processes. These innovations help maximize efficiency and ensure uniform application, resulting in better quality control and reduced labor costs.
Implications for Industries
The advantages of high-quality lost foam casting coatings extend across various industries, including automotive, aerospace, and construction. The ability to produce complex shapes with smooth finishes reduces the need for secondary processing, leading to cost savings and shorter production times. Additionally, the lightweight components produced through this method contribute to improved fuel efficiency and performance in automotive and aerospace applications.
As industries move towards more sustainable practices, the lost foam casting process, coupled with advanced coatings, presents an eco-friendly alternative due to reduced material waste and energy consumption. The adoption of these techniques can significantly enhance the sustainability profile of manufacturing processes, addressing growing concerns regarding environmental impact.
Conclusion
In conclusion, the coating in lost foam casting is a critical element that significantly influences the precision, quality, and efficiency of the casting process. With advancements in coating materials and application techniques, the lost foam process is set to continue evolving, providing industries with innovative solutions for creating high-performance components. As demand for complex geometries and sustainable practices rises, the role of coatings in lost foam casting will become increasingly important in meeting the challenges of modern manufacturing.
Post time:ਨਵੰ. . 19, 2024 13:47
Next:Materials Employed in the Process of Sand Casting Techniques and Applications