Lost Foam Sand Casting A Revolutionary Approach to Metal Casting
Lost foam sand casting is a highly efficient and innovative manufacturing process that has gained prominence in various industrial applications. This technique, which combines elements of traditional sand casting and foam pattern technology, offers significant advantages in terms of precision, complexity, and cost-effectiveness.
At its core, lost foam casting involves the creation of a foam pattern that is coated with a thin layer of sand. The foam pattern is made from polystyrene, which is lightweight and can be easily shaped into complex geometries. Once the pattern is created, it is coated with a sand mixture that typically consists of silica sand and a bonding agent. This forms a mold that can withstand the pouring of molten metal.
One of the most notable benefits of lost foam sand casting is its ability to produce intricate designs with minimal machining. Traditional casting methods often require extensive machining to achieve the desired final shape, but with lost foam, the foam pattern dissolves in the molten metal, leaving behind a smooth and precise casting. This significantly reduces the lead time and costs associated with post-casting processes, making it an attractive option for manufacturers.
Additionally, lost foam casting allows for the production of complex internal features that would be difficult or impossible to achieve using traditional methods. The foam pattern can be designed with various internal passages, cavities, and shapes that enhance the functionality of the final product. This is particularly beneficial in industries such as automotive and aerospace, where lightweight and intricate components are often required.
lost foam sand casting
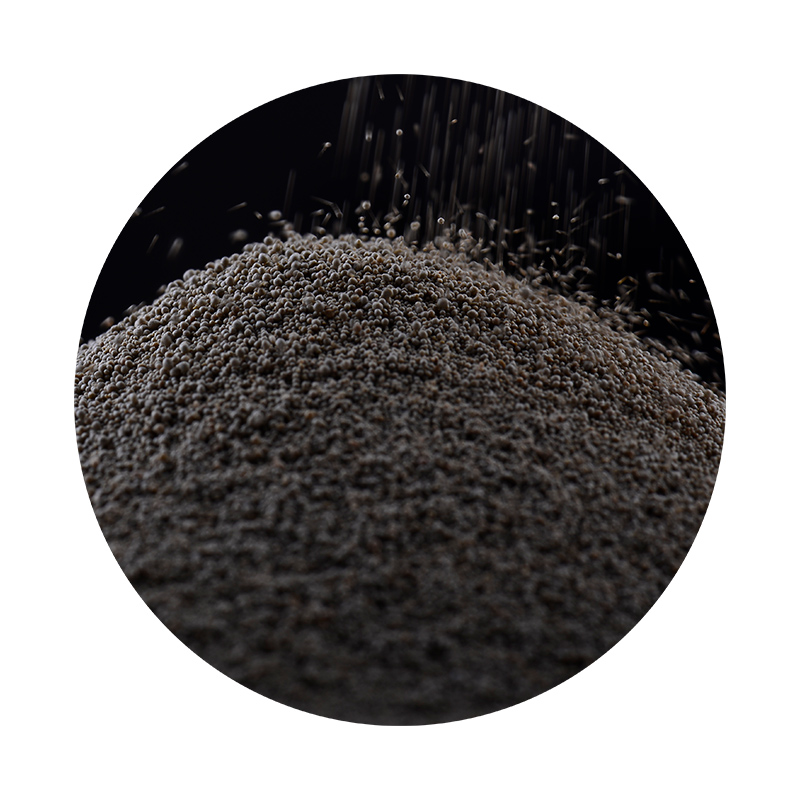
Moreover, the lost foam process is highly flexible when it comes to material selection. It can accommodate a wide range of metals, including aluminum, iron, and various alloys. This versatility enables manufacturers to choose the most suitable materials for their specific applications, further enhancing the process's efficiency and effectiveness.
In terms of environmental impact, lost foam sand casting offers several advantages. The foam pattern is typically made from recyclable materials, and the process generates less waste compared to traditional casting methods. Additionally, the elimination of cores used in traditional sand casting reduces the overall material consumption and energy used in production.
Despite its numerous advantages, lost foam casting does come with a few challenges. The process requires specialized equipment and skilled labor to ensure that the foam patterns are accurately created and properly placed in the mold. Furthermore, controlling the pouring process is crucial to prevent defects such as gas entrapment or incomplete filling.
In conclusion, lost foam sand casting represents a significant advancement in the field of metal manufacturing. Its ability to produce complex shapes with high precision and reduced lead times makes it a compelling choice for many industries. As technology continues to evolve, it is likely that lost foam casting will become even more prevalent, paving the way for the creation of innovative products that meet the demands of an increasingly competitive market. By embracing this cutting-edge process, manufacturers can enhance their production capabilities and contribute to a more sustainable future.
Post time:ਸਤੰ. . 14, 2024 05:20
Next:Historie písečného lití