Lost Foam Casting Revolutionizing Foundry Processes
Lost foam casting (LFC) is an innovative method that has significantly transformed traditional foundry practices. This casting process combines modern techniques with the age-old art of metallurgy, offering numerous advantages over conventional methods. By understanding the principles and benefits of lost foam casting, we can appreciate its role in the present-day foundry landscape.
At the heart of lost foam casting is the use of a foam pattern, typically made from expanded polystyrene (EPS). This pattern is designed to replicate the exact shape of the final cast product. During the casting process, the foam pattern is coated with a layer of sand, followed by the pouring of molten metal. As the metal fills the mold, it vaporizes the foam, leaving an empty cavity that takes on the shape of the original pattern. This lost foam method is where the process derives its name.
Lost Foam Casting Revolutionizing Foundry Processes
Moreover, the lost foam process excels in producing thin-walled components, making it ideal for industries like aerospace and automotive, where weight reduction is paramount. The lightweight nature of components made through LFC can lead to improved performance and fuel efficiency. Additionally, the method allows for the use of various metals and alloys, further enhancing its versatility and applicability across different industries.
lost foam casting foundry
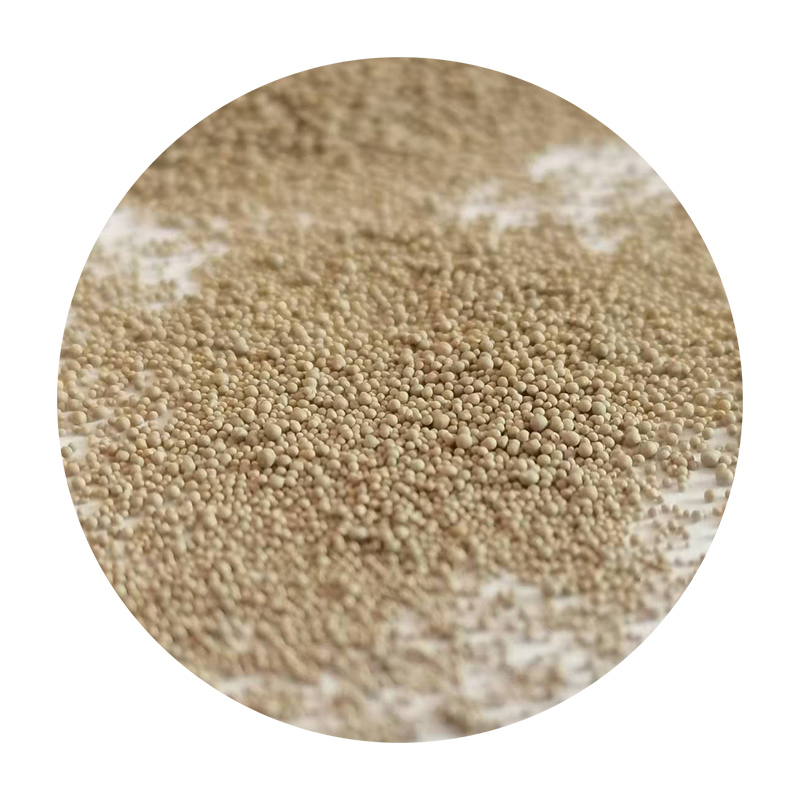
Another crucial advantage is cost-efficiency. While the initial investment in foam patterns and special machinery may be higher than traditional methods, the reduction in labor costs and waste material can significantly offset these expenses. The ability to cast multiple pieces in one cycle also contributes to overall operational efficiency, thereby lowering the cost per unit in mass production scenarios.
Despite its numerous advantages, the lost foam casting process is not without its challenges. Maintaining appropriate temperature control and ensuring proper vaporization of the foam are critical for achieving high-quality castings. Defects such as surface roughness or incomplete fill can occur if these parameters are not meticulously managed. However, advancements in technology and control systems are continuously improving the reliability and quality of LFC.
The growing acceptance of lost foam casting is a testament to its effectiveness and innovation. Industries that demand precision and efficiency are increasingly adopting this method, fostering advancements in design and manufacturing techniques. As we move toward a future where sustainability and efficiency are paramount, lost foam casting stands out as a promising solution in the foundry sector.
In conclusion, lost foam casting represents a significant advancement in foundry technology, offering unparalleled advantages in terms of precision, complexity, and cost-effectiveness. As industries continue to evolve, embracing cutting-edge manufacturing techniques like LFC will be essential for meeting the demands of modern production while minimizing environmental impact. With its unique attributes and growing application, lost foam casting is poised to reshape the foundry landscape for years to come.
Post time:ਸਤੰ. . 04, 2024 23:08
Next:sand casting history