How Sand Casting is Done
Sand casting, a widely used metal casting process, is celebrated for its versatility, cost-effectiveness, and ability to produce complex shapes. This process is suitable for various metals, including iron, aluminum, and bronze. The sand casting technique involves several steps, each critical to ensuring a successful casting.
1. Pattern Making
The first step in sand casting is the creation of a pattern, which is a replica of the desired final product. Patterns can be made from various materials such as wood, metal, or plastic, depending on the intricacy and requirements of the casting. The pattern must account for shrinkage that occurs during cooling, and it is often oversized to compensate for this. Patterns can be of different types solid, split, or shell, depending on the complexity of the shape.
2. Creating the Sand Mold
Once the pattern is prepared, the next step is to create the mold. A mixture of sand, clay, and water is commonly used to create the mold. The sand provides strength, while the clay acts as a binder, giving the mixture ideal properties for casting. The pattern is embedded into the sand mixture, forming the mold cavity through which molten metal will be poured.
To make the mold, the sand mixture is compacted around the pattern, ensuring that the details are preserved. Once the sand has settled, the pattern is removed, leaving an impression. In the case of complex patterns, molds may be created in two halves, allowing for easier removal of the pattern.
3. Core Making (if necessary)
For castings with hollow sections, cores are created using a similar sand mixture. Cores are placed within the mold to define internal shapes. Like patterns, cores are also removed after the mold is prepared. Care must be taken to ensure they are sturdy enough to withstand the molten metal’s pressure.
how sand casting is done
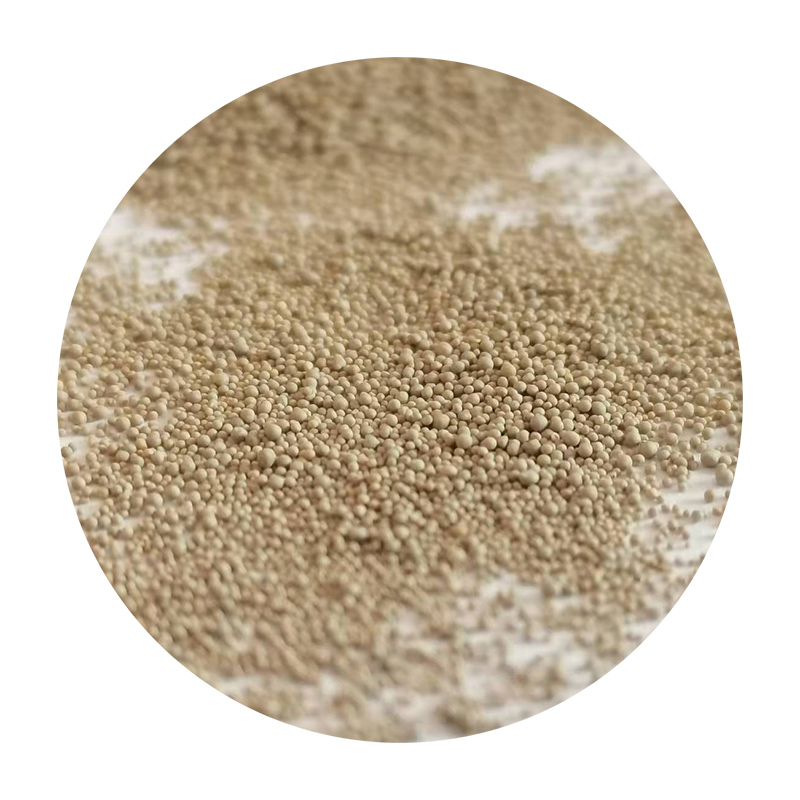
The next step is the pouring of the molten metal into the mold. The metal is heated until it reaches a liquid state and is then carefully poured into the mold cavity. This step must be done with precision to prevent defects such as excessive turbulence or air entrapment. The pouring temperature, as well as the speed of pouring, significantly impact the quality of the final casting.
5. Cooling and Solidification
After pouring, the molten metal needs time to cool and solidify. The duration of cooling depends on the material being cast and the thickness of the metal. Cooling must be controlled, as rapid cooling can lead to defects such as cracking or distortion.
6. Mold Removal and Cleaning
Once the metal has fully solidified, the sand mold is broken away to reveal the casting. The casting is then cleaned to remove any sand and other residues. This is often done through sandblasting or chemical cleaning processes.
7. Finishing Touches
After cleaning, additional finishing processes may be required. This can include machining to achieve precise dimensions, surface finishing, or surface treatments to enhance properties like corrosion resistance.
In conclusion, sand casting is an efficient and adaptable method for producing metal parts and components. By understanding and executing each step—from pattern making to final finishing—manufacturers can create high-quality castings that meet diverse industry needs. The simplicity and effectiveness of sand casting continue to make it a favored choice in metalworking.
Post time:ਨਵੰ. . 25, 2024 04:50
Next:foundry sand price