How Long Does Sand Casting Take?
Sand casting is a versatile and widely-used manufacturing process for creating metal parts. This technique is employed across various industries, including automotive, aerospace, and machinery, to produce everything from small components to large and complex shapes. However, a common question that arises among those new to the process is how long does sand casting take? The answer can vary significantly based on several factors, including the complexity of the part, the size of the production run, and the specific materials used.
Overview of the Sand Casting Process
Before delving into timing, it is essential to understand the basic steps involved in sand casting. The process generally includes
1. Pattern Making The first step involves creating a mold pattern, typically made from a stable material like wood, metal, or plastic, that replicates the final product's shape. 2. Mold Preparation The pattern is then buried in sand mixed with a binding agent to create a mold that can withstand the casting process. The sand is compacted around the pattern, and once it is removed, it leaves a cavity that resembles the desired part.
3. Pouring Molten metal is poured into the prepared mold cavity. The temperature and type of metal can influence the pouring time and cooling process.
4. Cooling After pouring, the metal must cool and solidify, which can take a few minutes to several hours, depending on the part's size and material characteristics.
5. Mold Removal Once the metal has solidified, the sand mold is broken away to reveal the cast part.
Time Considerations
The time it takes to complete a sand casting project can be broken down into several segments
how long does sand casting take
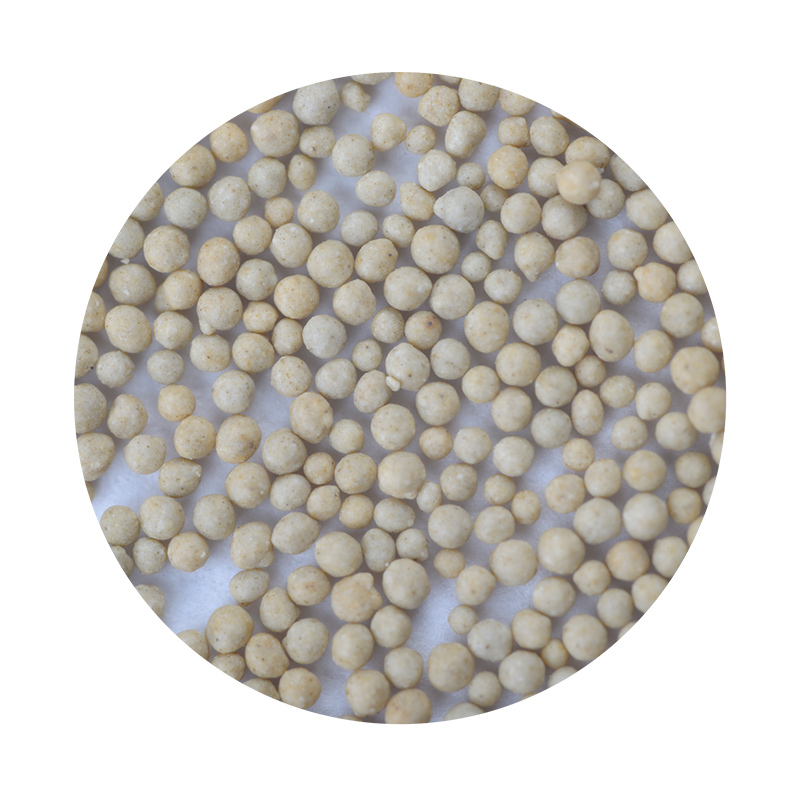
1. Pattern Creation Developing a pattern can be time-consuming, particularly for complex shapes. This process can take anywhere from a few days to several weeks. The investment in time here is crucial as it directly affects the overall efficiency of the casting process.
2. Mold Preparation and Pouring Once a pattern is ready, preparing the mold and pouring the metal can be relatively quick. Typically, this phase may take a few hours. For small-scale production runs, the setup time can be longer relative to the actual pouring time.
3. Cooling Time The cooling time varies significantly based on the size and thickness of the cast part and the type of metal being used. Thin-walled parts may cool in just a few minutes, while larger components might require several hours.
4. Post-Casting Operations After the metal has cooled, the process of breaking the mold and finishing the part can take anywhere from a few hours to a couple of days, depending on the complexity of the item and the post-processing requirements.
5. Total Turnaround In short-run casting, where a limited number of parts are produced, the entire process from pattern making to completion might take a couple of weeks. However, for high-volume production runs, efficiency can significantly reduce lead times per part, often allowing businesses to achieve their objectives faster.
Contributing Factors to Lead Time
Several factors can influence lead times in sand casting, including
- Complexity of Design Intricate designs require more elaborate patterns and longer mold preparation times. - Material Choices Different metals have specific cooling and solidification times that can impact the overall schedule. - Production Volume Higher production runs may justify faster tooling processes, shortening overall timeframes. - Available Technology Advances in technology, such as 3D printing patterns, can drastically reduce pattern creation times.
Conclusion
Understanding the time frame involved in sand casting is vital for effective project planning and management. While basic operations can be completed fairly quickly, factors like pattern complexity, cooling times, and finishing requirements can extensively vary lead times. For manufacturers, an efficient workflow and strategic planning can help optimize the sand casting process, enhancing both productivity and quality of the final products. Thus, anyone considering sand casting should evaluate these variables meticulously to ensure successful outcomes.
Post time:ਅਕਤੂਃ . 22, 2024 06:44
Next:Understanding the Expenses Involved in Sand Casting Processes and Techniques