Understanding Foundry Sand Properties
Foundry sand is a critical component in the metal casting process and plays a significant role in determining the quality and precision of cast metal components. As the demand for high-performance castings rises in various industries, understanding the properties of foundry sand becomes increasingly important. In this article, we will explore the various properties of foundry sand, how they affect casting performance, and the considerations necessary for optimal use.
Types of Foundry Sand
The most commonly used type of foundry sand is silica sand, particularly because of its excellent thermal properties and ability to withstand high temperatures. Other types of foundry sands include zircon sand, chromite sand, and olivine sand, each offering unique characteristics suitable for specific applications. The choice of sand largely impacts the mold's permeability, strength, and overall integrity during the casting process.
Key Properties of Foundry Sand
1. Grain Size and Distribution The grain size of foundry sand significantly influences the mold's surface finish and dimensional accuracy of the cast component. Fine grains provide a smoother finish but may reduce permeability, while coarser grains enhance sand strength but can lead to a rougher finish. A well-graded distribution of sand grains is critical to optimize these opposing effects.
2. Permeability Permeability refers to the ability of the sand mold to allow gases and air to escape during the casting process. High permeability is essential in preventing defects such as blowholes, which occur when gases cannot escape from the mold. However, too much permeability can compromise mold strength. Hence, foundry operators aim for a balance that achieves both adequate gas escape and sufficient mold strength.
foundry sand properties
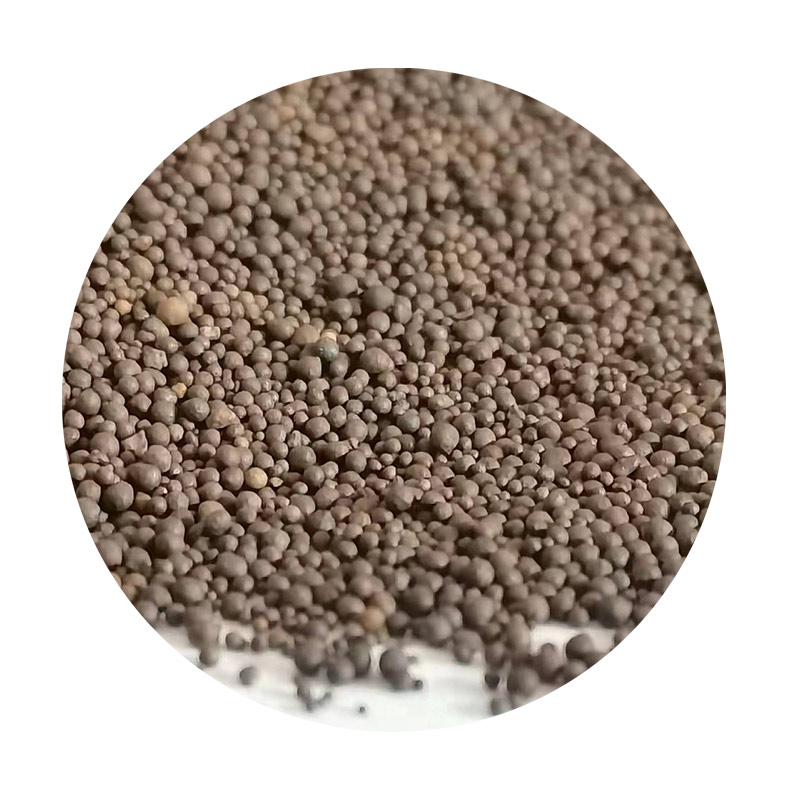
3. Moisture Content The moisture content in foundry sand affects its bonding ability and strength. Properly controlled moisture ensures that the sand grains adequately bond together, providing mechanical strength and preventing cracking during the casting process. Typically, moisture content is kept around 2-5%, depending on the specific sand type and mix used.
4. Strength The strength of foundry sand is crucial to maintain the structural integrity of the mold during the pour. There are different types of strength to consider, including green strength (the strength of the mold just after forming) and dry strength (the strength of the mold after being dried). High green strength is particularly important to support the weight of the molten metal.
5. Thermal Conductivity Foundry sand needs to withstand high temperatures, which makes thermal conductivity an important property. Ideal foundry sands should have low thermal expansion and high thermal stability to prevent deformation during casting. Silica sand, for instance, has a high melting point that suits the rigorous demands of metal casting.
Environmental and Economic Considerations
In addition to the physical properties of foundry sand, environmental and economic factors must also be taken into account. For instance, the recycling of sand can significantly reduce costs and minimize environmental impact. Used sand can often be cleaned and reused, which lessens the need for new material and reduces waste.
Conclusion
In summary, the properties of foundry sand significantly influence the quality and characteristics of cast products. Grain size, permeability, moisture content, strength, and thermal conductivity are key factors that must be carefully controlled during the casting process. As industries continue to evolve and demand greater precision and efficiency, a thorough understanding of foundry sand properties will remain essential for foundries aiming to produce superior castings while meeting environmental and economic considerations. Continuous research and development in this area can lead to innovative solutions that further enhance the casting processes and materials used in various applications.
Post time:ਨਵੰ. . 07, 2024 16:23
Next:عملية صب الرمل في المسبك خطوات أساسية وتقنيات متقدمة