Foundry Sand Casting Process An Overview
Foundry sand casting is a widely used manufacturing process that involves creating metal castings by pouring molten metal into a mold made of sand. This technique has been utilized for centuries, owing to its simplicity, versatility, and cost-effectiveness. The process is essential in producing a diverse range of metal parts and components used in various industries, including automotive, aerospace, machinery, and more.
The sand casting process begins with the design and production of a pattern, which acts as a replica of the final product. The pattern is typically made of materials such as wood, metal, or plastic and is designed with tolerances and allowances to account for shrinkage as the metal cools. Once the pattern is complete, it is used to create a mold.
Foundry Sand Casting Process An Overview
After the mold is formed, the pattern is removed, leaving a cavity that matches the shape of the pattern. The next step is the preparation of the molten metal, which can be made from various alloys including iron, aluminum, and bronze. The metal is typically melted in a furnace, such as an induction or electric arc furnace, depending on the type of metal and the desired properties.
foundry sand casting process
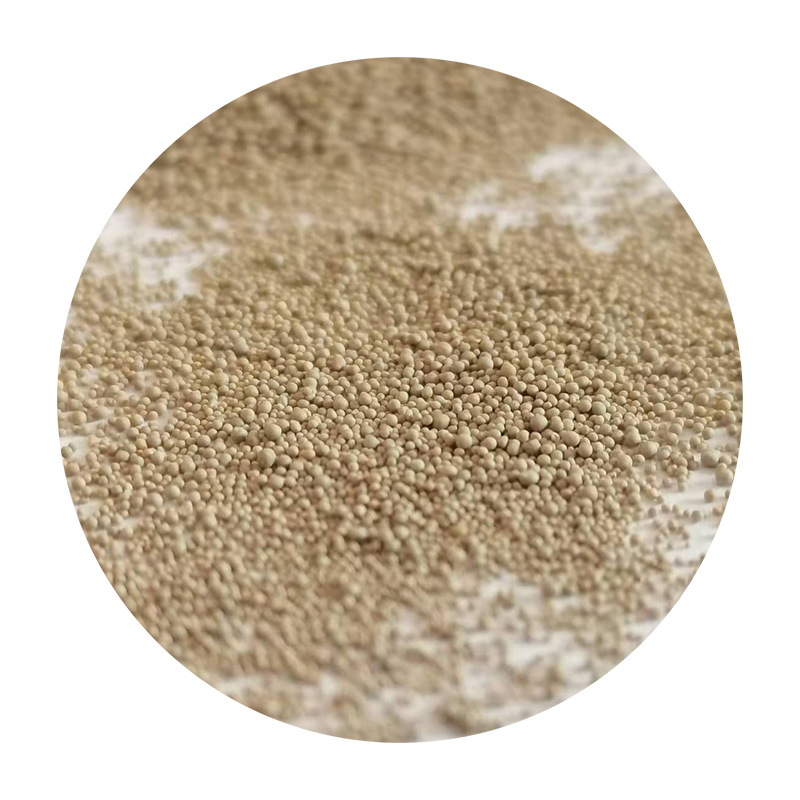
Once the metal reaches the appropriate temperature, it is poured into the mold cavity. This step requires precision, as the flow of molten metal must be controlled to prevent defects such as air pockets or cold shuts. The metal is allowed to cool and solidify in the mold, a process that can take from a few minutes to several hours depending on the size and thickness of the casting.
After the metal has cooled, the mold is broken away to reveal the casting. The casting often requires further processing, such as trimming, grinding, and surface finishing, to achieve the desired specifications. This secondary processing is crucial, as it enhances the casting’s dimensional accuracy, surface quality, and mechanical properties.
One of the key advantages of the sand casting process is its ability to produce complex shapes that may be challenging or cost-prohibitive to achieve through other manufacturing methods. Additionally, sand casting can accommodate a range of metal types and is suitable for both small and large production runs.
However, sand casting is not without its challenges. It often results in a surface finish that may require additional machining, and there can be issues related to dimensional accuracy when compared to more modern techniques like investment casting. Despite these disadvantages, the process remains a popular choice in foundries worldwide due to its flexibility and the wide array of materials that can be utilized.
In conclusion, the foundry sand casting process is a fundamental manufacturing technique that plays a vital role in producing metal components across various industries. Its advantages, including cost-effectiveness and the capability to cast complex shapes, ensure that it remains an essential part of the metalworking landscape. As technology advances, innovations in sand casting continue to make it a relevant and valuable option for manufacturers.
Post time:ਨਵੰ. . 12, 2024 07:59
Next:metal casting sand for sale