Different Types of Foundry Sand An Overview
Foundry sand is a vital component in the metal casting industry, primarily used to create molds for a wide variety of metal products. This type of sand must possess specific characteristics to ensure high-quality mold formation and casting processes. Here, we’ll explore the different types of foundry sand, their properties, and their applications.
1. Silica Sand
Silica sand, primarily composed of silicon dioxide (SiO2), is the most commonly used type of foundry sand. It has excellent thermal conductivity, which is crucial for heat diffusion during the casting process. Silica sand’s angular particles provide good mold strength and permeability, which allows gases generated during pouring to escape easily, preventing defects in the casting. Its ability to withstand high temperatures makes it ideal for iron and steel castings. Moreover, silica sand is relatively inexpensive, contributing to its widespread use in the industry.
2. Green Sand
Green sand is a mixture of silica sand, clay (often bentonite), water, and various additives. It is known as green due to the moisture content, which distinguishes it from dried sands. Green sand molds are characterized by their excellent collapsibility, enabling quick pattern removal without damaging the mold. This type of sand is widely used for ferrous and non-ferrous metal casting, especially in the production of automotive parts. The clay content in green sand provides binding properties, enhancing the strength and integrity of the mold.
3. Resin Sand
different types of foundry sand
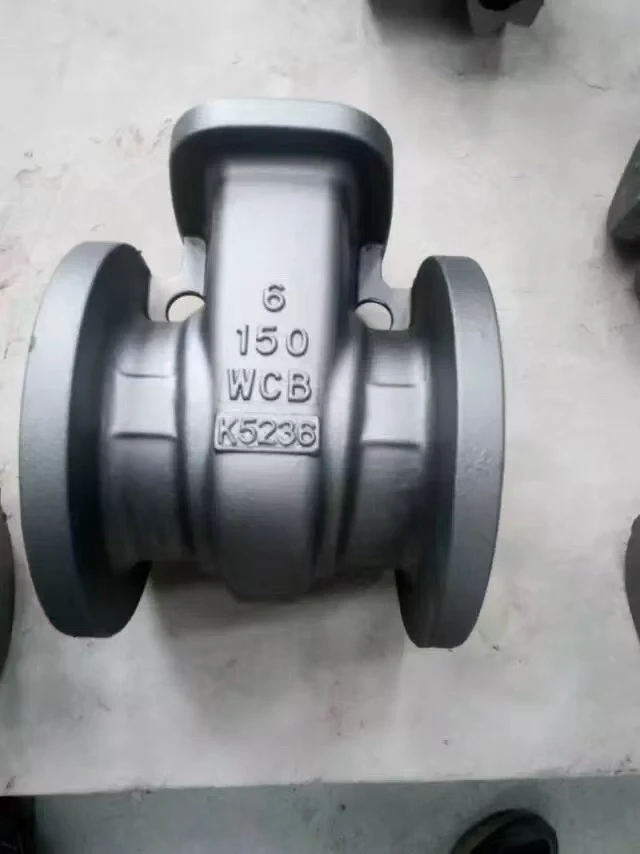
Resin sand utilizes a synthetic resin as a bonding agent, offering several advantages over traditional green sand. The most significant benefit is the ability to create molds with finer detail and smoother surfaces. This makes resin sand particularly suitable for precision casting applications where dimensional accuracy is critical. Furthermore, resin sand molds can be cured using heat or chemical reactions, resulting in high-strength molds that can withstand high pouring temperatures. However, the cost of resin sand is typically higher than that of traditional sand, which may limit its use in some applications.
4. Investment Casting Sand
Investment casting, also known as lost-wax casting, is another method that utilizes a specific type of sand. In this process, a wax pattern is coated with a ceramic shell, which is then filled with metal. The sand used in this method tends to be finer and provides a smooth surface finish to the final product. The investment casting process allows for the creation of complex shapes with tight tolerances, making it ideal for industries such as aerospace and medical devices.
5. Chromite Sand
Chromite sand, derived from the mineral chromite, is often used in high-temperature applications due to its excellent thermal resistance. Unlike silica sand, which can produce toxic fumes at high temperatures, chromite sand remains stable, making it suitable for steel and iron casting. It provides exceptional mold strength and is commonly employed in applications where stability and durability are paramount, such as in the production of heavy machinery parts.
Conclusion
In summary, the choice of foundry sand significantly impacts the quality and efficiency of the casting process. Whether it’s silica sand for its cost-effectiveness, green sand for its flexibility, resin sand for precision, investment casting sand for detailed work, or chromite sand for high-temperature stability, each type serves a unique purpose in the industry. Understanding the characteristics and applications of these sands is essential for foundry engineers and manufacturers aiming to optimize their casting processes and meet the demands of their markets. As technology advances, the development of new types of foundry sand may also emerge, further improving casting efficiency and product quality.
Post time:ਦਸੰ. . 10, 2024 23:40
Next:Advancements in Sand Casting Technology for Enhanced Manufacturing Processes and Applications