Coated Sand Innovations in Sand Casting and Beyond
Sand casting is one of the oldest and most widely used manufacturing processes in the world, enabling the production of intricate metal parts with relative ease and efficiency. However, the quality and surface finish of cast products can sometimes fall short of modern standards. This is where coated sand comes into play. Coated sand, a refined version of traditional sand, is gaining traction in the manufacturing sector for its ability to enhance the casting process, improve product quality, and reduce defects.
Coated sand typically consists of silica sand particles that are treated with a polymer binder or coating. This coating creates a durable barrier around each sand grain, which significantly improves the sand's performance during the casting process. The primary benefits of using coated sand in foundries include enhanced mold strength, reduced gas emissions, and improved surface finish of the final product.
One of the most significant advantages of coated sand is its ability to increase the strength of molds and cores
. The polymer coating helps the sand grains to stick together more effectively, resulting in a stronger mold that can withstand the stresses of pouring molten metal. This increased mold strength reduces the likelihood of defects such as sand inclusion and deformation during the casting process, ultimately leading to higher-quality finished products.coated sand
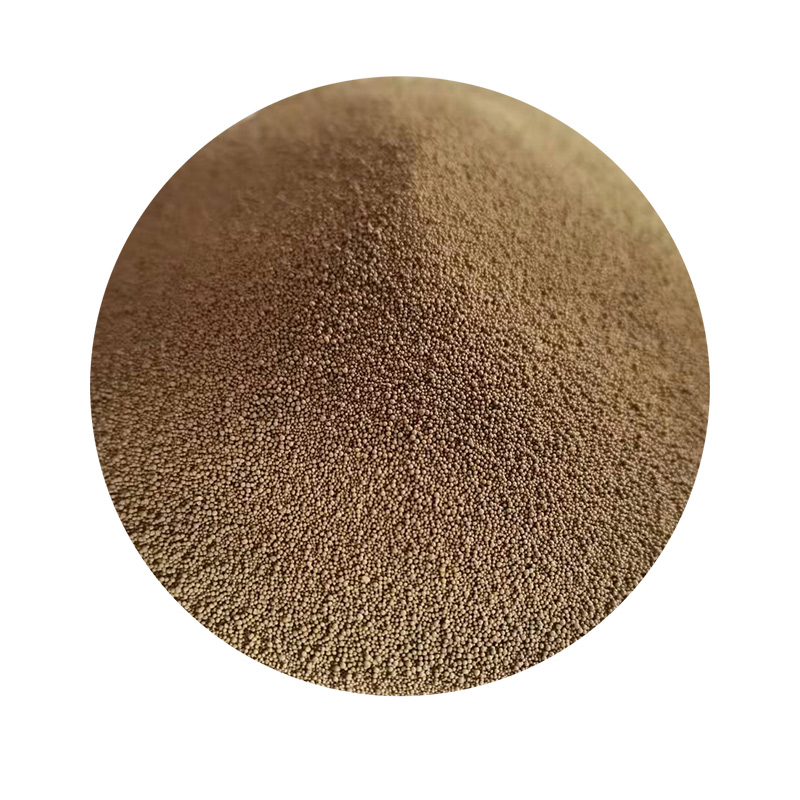
Another critical benefit of coated sand is its role in minimizing gas emissions. When heated, traditional sand can release harmful gases that can negatively impact both the casting quality and the working environment. Coated sand minimizes this problem because the polymer coating reduces the sand's ability to absorb moisture. Consequently, there is less gas generation during the melting and pouring processes, which leads to a safer and more efficient work environment.
Moreover, coated sand significantly enhances the surface finish of cast products. The smooth surface of coated sand reduces the roughness typically associated with cast metals, allowing for better dimensional accuracy and a more aesthetically pleasing finish. This characteristic is particularly valuable in industries where surface quality is paramount, such as in the automotive and aerospace sectors. With coated sand, manufacturers can meet stringent quality standards while reducing the need for extensive post-casting machining processes.
The application of coated sand is not limited to traditional metal casting. Its versatility extends to various industries, including the production of ceramics, composite materials, and even some forms of 3D printing. In ceramics, coated sand can be used to create molds with intricate designs, while in composite manufacturing, it can provide improved performance characteristics. The emergence of 3D printing technologies has also seen coated sand being utilized as a printing medium, demonstrating its adaptability across various processes.
In conclusion, coated sand serves as a valuable innovation in the field of casting and manufacturing. By enhancing mold strength, reducing gas emissions, and improving surface finishes, coated sand addresses several critical challenges faced by industries relying on traditional sand casting methods. As manufacturers continue to seek ways to improve their processes and products, the adoption of coated sand is likely to grow, paving the way for higher quality, more efficient, and safer manufacturing practices. The future of manufacturing will undoubtedly benefit from the continued development and integration of coated sand technologies, making it an essential component of modern production methodologies.
Post time:ਦਸੰ. . 04, 2024 19:39
Next:foundry sand in concrete