The Evolution and Advantages of Cast Iron Sand Casting
Cast iron sand casting is a significant manufacturing process that has been utilized for centuries, stemming from ancient techniques of metalworking. It involves pouring molten cast iron into a sand mold to produce a wide range of components, from intricate machinery parts to heavy-duty industrial components. This article explores the evolution, advantages, and applications of cast iron sand casting.
Historical Background
The origins of sand casting can be traced back to ancient civilizations, including the Chinese, Egyptians, and Greeks, who used sand molds to create bronze and iron artifacts. With the advent of iron smelting, the process evolved to incorporate iron, leading to the development of cast iron as a robust material known for its durability and resistance to deformation. The unique properties of cast iron, such as high wear resistance, excellent machinability, and good fluidity when molten, made it an ideal candidate for sand casting.
With the industrial revolution in the 18th and 19th centuries, sand casting for cast iron took off. The demand for machinery and infrastructure led to significant advancements in the techniques and technology used in sand casting, making it a cornerstone of modern manufacturing.
The Sand Casting Process
The sand casting process typically involves several steps
1. Pattern Making A pattern, usually made of wood, metal, or plastic, is created to form the mold cavity. The pattern is a replica of the final product.
2. Mold Preparation The pattern is placed in a molding box, and sand mixed with a binder is packed around it. Once the sand hardens, the pattern is removed, leaving a cavity that matches the shape of the pattern.
3. Melting and Pouring Cast iron is melted in a furnace and then poured into the mold cavity. The molten metal takes the shape of the mold as it cools and solidifies.
4. Cooling and Cleaning After cooling, the mold is broken apart, and the cast iron part is removed. The component may require further processing, such as machining and surface finishing.
cast iron sand casting
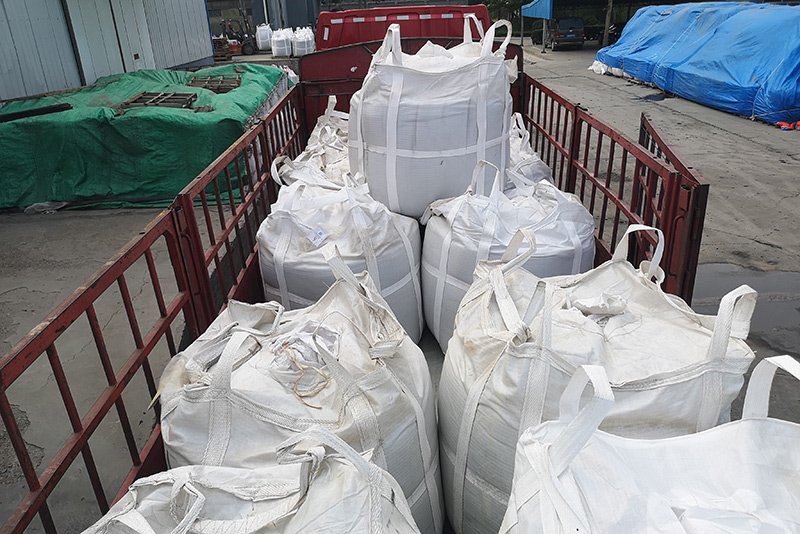
Advantages of Sand Casting for Cast Iron
1. Versatility Sand casting can produce a wide variety of shapes and sizes, making it suitable for industries ranging from automotive to aerospace. Complex geometries can be achieved with relative ease, allowing for intricate designs that meet specific engineering requirements.
2. Cost-Effectiveness The materials used in sand casting, primarily sand and binders, are inexpensive and widely available. This makes sand casting an economical choice, especially for large-scale production runs or custom components.
3. High Tolerance Levels Cast iron exhibits excellent dimensional stability. As a result, sand casting often results in components that can hold tight tolerances, reducing the need for extensive finishing work.
4. Durability Cast iron parts produced through sand casting are well-regarded for their strength and durability. They are able to withstand high levels of stress and wear, making them ideal for heavy-duty applications.
5. Recyclability The sand used in the casting process can often be reclaimed and reused, making sand casting a more sustainable option compared to other casting methods.
Applications
Cast iron sand castings find applications in various sectors, including automotive components like engine blocks and cylinder heads, industrial machinery, construction equipment, and even decorative items. Their robustness and ability to be molded into complex shapes make them indispensable in many high-performance environments.
Conclusion
Cast iron sand casting is a time-honored manufacturing process that continues to evolve with advancements in technology and materials. Its versatility, cost-effectiveness, and durability make it a preferred method for producing a wide range of high-quality components across diverse industries. As industries continue to innovate, the role of cast iron sand casting remains crucial in meeting modern engineering challenges while honoring traditional craftsmanship.
Post time:ਨਵੰ. . 08, 2024 12:48
Next:similar sand g2 design for enhanced performance and versatility in various applications