Casting Sand for Metal An Essential Component in Metal Production
Casting is one of the oldest manufacturing processes known to humanity and continues to be a vital technique in producing metal components across various industries. Central to this process is casting sand, which serves as a mold material for shaping molten metal into desired forms. This article explores the importance, types, properties, and applications of casting sand in the metal foundry industry.
Importance of Casting Sand
Casting sand is crucial in metal casting as it provides the mold in which molten metal is poured and cooled to form solid objects. The quality of the casting sand directly affects the final product's accuracy, surface finish, and structural integrity. Therefore, selecting the appropriate type of sand and preparing it correctly is essential for achieving optimal results in metal casting.
Types of Casting Sand
There are several types of casting sand used in the industry, each with its unique properties and applications
1. Green Sand This is the most common type of casting sand, composed of silica sand, clay, and water. The moisture in green sand helps it bind together, creating a mold that can withstand the heat of molten metal. It's particularly popular for its excellent moldability and the ability to produce intricate details in castings.
2. Dry Sand Unlike green sand, dry sand contains little to no moisture. It is typically used for molds that require a faster drying process and improved dimensional accuracy. Dry sand molds are more rigid and can be used for larger castings.
3. Furan Sand This type of sand utilizes furan resin as a bonding agent, which can create high-strength molds suitable for casting complex shapes. Furan sand is valued for its durability and resistance to thermal shock, making it ideal for high-temperature casting processes.
4. Shell Sand Shell sand consists of a fine mixture of sand and resin, which is used to create a thin shell around a pattern. When heated, the resin hardens to form a rigid mold. This technique allows for better surface finishes and precise tolerances in cast metal parts.
Properties of Casting Sand
casting sand for metal
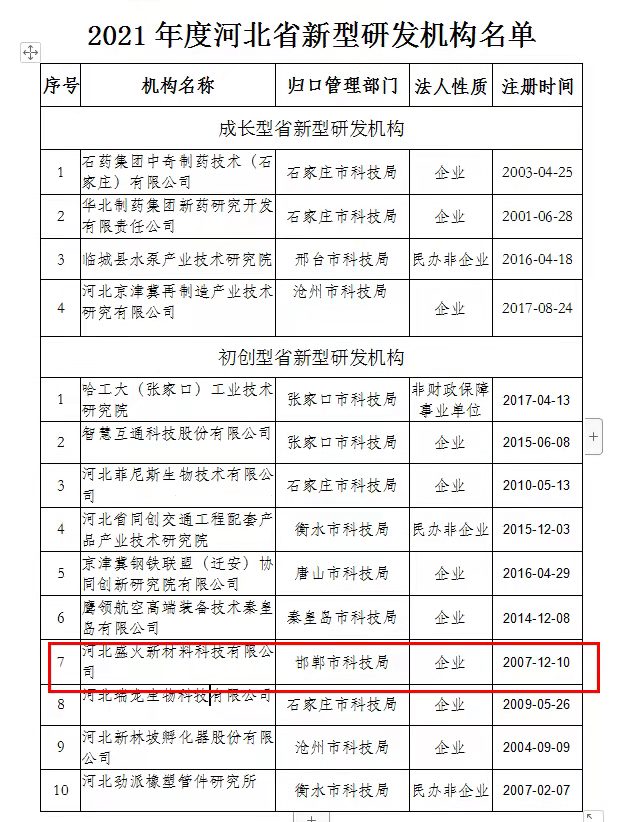
The effectiveness of casting sand is determined by several properties
- Grain Size The grain size of the sand affects the mold's ability to capture detail, determine surface finish, and influence the cooling rates of the molten metal. Finer sands provide better detailing but may lead to slower cooling, while coarser sands allow for quicker cooling but less detail.
- Strength The strength of the sand is essential to withstand the weight and pressure of the molten metal. A strong mold prevents deformation during the pouring process.
- Permeability This property indicates the ability of gases to escape from the mold during casting. Adequate permeability is crucial as it prevents the formation of gas pockets, which can weaken the casting.
- Thermal Stability Casting sand must withstand high temperatures without breaking down. Good thermal stability ensures that the mold maintains its shape and integrity during the pouring of molten metal.
Applications of Casting Sand
Casting sand is extensively employed in the metalworking industry, particularly in foundries to produce various metal components. These include automotive parts, aerospace components, industrial machinery, and artistic sculptures. The versatility of casting sand is evident in applications ranging from mass production to custom, low-volume manufacturing.
In recent years, advancements in technology have improved the quality and effectiveness of casting sands. Innovations such as synthetic sands and recycled materials are being explored to enhance sustainability in the casting process.
Conclusion
Casting sand plays a fundamental role in the metal casting industry. Its properties and types significantly influence the outcome of the casting process. Understanding the characteristics of different casting sands can help foundries optimize their production techniques, improve the quality of their products, and adapt to changing market demands. As industries continue to evolve, the significance of casting sand remains steadfast, demonstrating its enduring value in metal production.
Post time:ਨਵੰ. . 12, 2024 06:24
Next:cerabead