Casting Sand The Unsung Hero of Metalworking
In the world of metalworking, the term casting evokes images of molten metal poured into intricate molds, resulting in components that are both functional and aesthetically pleasing. Yet, behind this age-old practice lies an unsung hero casting sand. Often underappreciated, casting sand is essential in the foundry industry, playing a crucial role in the production process of metallic goods.
Casting sand, primarily made up of silica, serves as a molding material that can withstand high temperatures and pressures. Its primary characteristic is its ability to hold the shape of the mold, which is vital when molten metal is introduced. Various types of sand, such as green sand, resin sand, and lost foam sand, are employed depending on the specific requirements of the casting process. Each type has its own properties, benefits, and applications, making casting sand a versatile material in metal foundries.
Green Sand The Foundation of Metalcasting
Green sand is the most commonly used casting sand, composed of silica sand, clay, and water
. The clay serves as a binder, allowing the sand to retain its shape. This combination creates a mold that can be easily formed and compacted around a pattern, providing excellent dimensional accuracy and surface finish. Additionally, green sand molds can be reused multiple times, which makes it an economical choice for foundries focused on sustainability.The handling and preparation of green sand are essential for optimal casting results. Factors such as moisture content, grain size, and clay percentage can significantly influence the final product. Foundries often conduct tests to ensure the quality of the sand mixture, reflecting the importance of this material in achieving desired casting outcomes.
Resin Sand Precision and Efficiency
casting sand
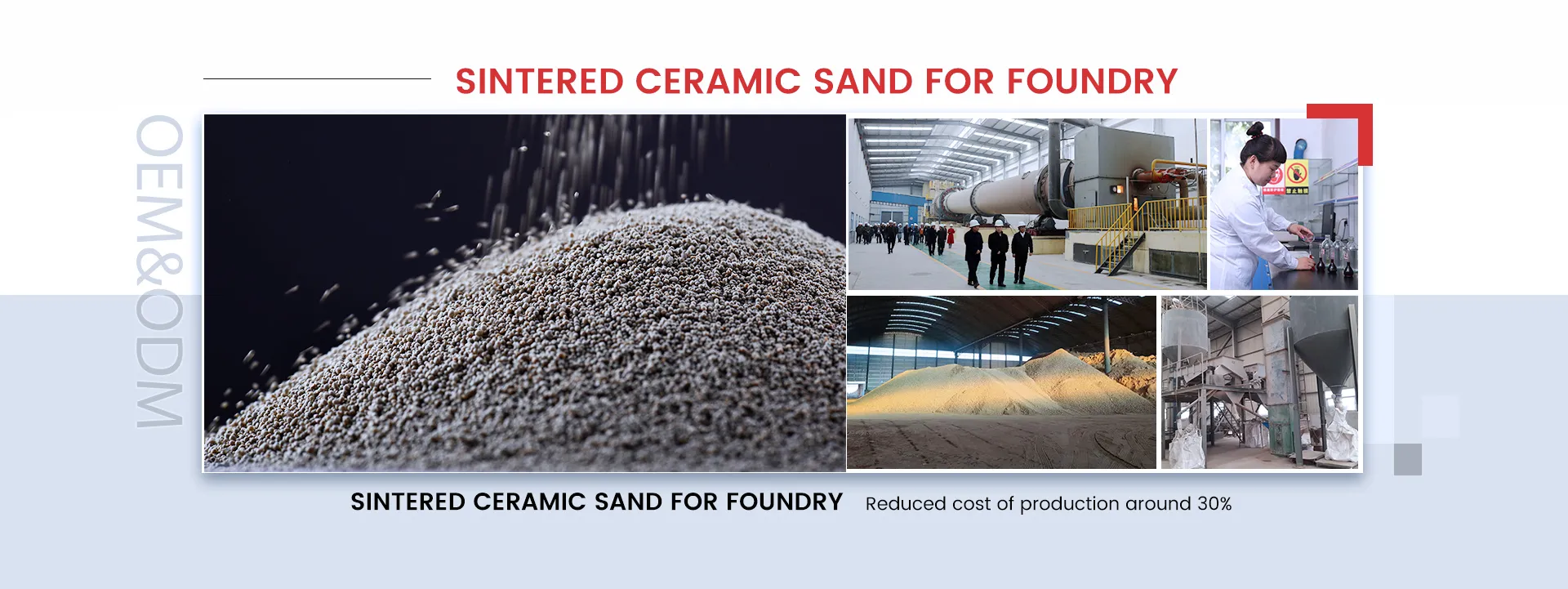
In contrast to green sand, resin sand is a chemically bonded material that offers heightened precision and strength. The use of resin as a binding agent allows for the creation of more detailed and intricate molds, making it ideal for specialized applications in aerospace, automotive, and artistic industries. This type of sand provides consistent quality and is less susceptible to environmental variations, making it a preferred choice for high-production environments.
Despite its advantages, resin sand is more expensive than green sand, which may deter some foundries from adopting it. However, for businesses that prioritize quality and efficiency, the investment often pays off in reduced scrap rates and improved product reliability.
Lost Foam Sand An Innovative Approach
Lost foam casting is a relatively modern technique that involves the use of a foam pattern instead of traditional solid patterns. This method allows for more complex shapes and reduced machining costs. The foam pattern is coated with a layer of sand, which is then allowed to harden. When molten metal is poured into the mold, it evaporates the foam, leaving a cavity into which the metal flows. This innovative application of casting sand streamlines the process and minimizes waste, appealing to environmentally conscious manufacturers.
Conclusion The Integral Role of Casting Sand
In conclusion, casting sand is a vital component of the metalworking industry, often overlooked but essential for producing high-quality metal products. From green sand’s versatility to resin sand’s precision and lost foam’s innovation, the various types of casting sand each bring unique benefits to the table. As the industry continues to evolve and innovate, the importance of casting sand remains steadfast. For those looking to create intricate designs and reliable components, recognizing the value of casting sand is the first step towards achieving excellence in metalcasting.
Post time:ਨਵੰ. . 24, 2024 20:42
Next:Innovative Techniques in Lost Foam Metal Casting for Enhanced Precision and Efficiency