Advantages and Disadvantages of Sand Casting
Sand casting is one of the oldest and most widely used metal casting processes. It involves the use of sand as the main material to create the mold into which molten metal is poured. This traditional method has several advantages and disadvantages that affect its applicability in various industries. Understanding both sides can help manufacturers choose the best casting process for their specific needs.
Advantages of Sand Casting
1. Cost-Effectiveness One of the primary advantages of sand casting is its cost-effectiveness. The materials used, predominantly sand, are relatively inexpensive and easily available. Additionally, the process does not require elaborate machinery or tools, which further reduces production costs.
2. Flexibility in Design Sand casting allows for a high degree of design flexibility. Almost any shape can be produced, including complex geometries that might be difficult or impossible to achieve with other casting methods. The use of sand molds means that intricate details can be incorporated into the final product.
3. Large Part Production This casting technique can accommodate large components, making it suitable for industries that require heavy and oversized parts, such as automotive and aerospace. The size of the molds can be adjusted easily, facilitating the production of both small and large casting runs.
4. Variety of Metals Sand casting can be used with a wide range of metals, including aluminum, bronze, iron, and magnesium. This versatility allows manufacturers to select materials based on the performance requirements of the application, without being limited by the casting method.
5. No Need for High Production Volumes Unlike some other casting methods that require high production volumes to be cost-effective, sand casting is viable even for small production runs. This is particularly advantageous for artisans and companies that require customized or prototype parts.
6. Environmentally Friendly Sand can be reused multiple times in the sand casting process, minimizing waste. Additionally, modern sand casting techniques utilize environmentally friendly processes and materials. The possibility of recycling used sand reduces the environmental footprint of this casting method.
advantages and disadvantages of sand casting
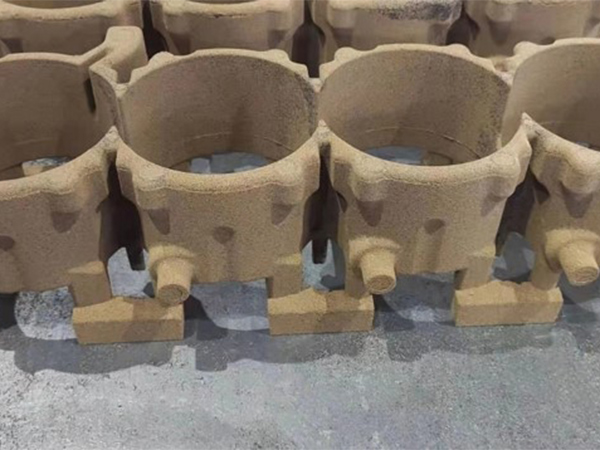
Disadvantages of Sand Casting
1. Surface Finish and Tolerance One of the notable drawbacks of sand casting is the quality of the surface finish. The rough texture of sand molds can result in a final product that requires additional finishing processes to achieve a smoother surface. Furthermore, sand casting typically does not offer the tight tolerances that some applications demand, which can lead to operational inefficiencies.
2. Labor-Intensive The process of making molds from sand often requires significant manual labor, which can lead to higher labor costs and increased production times. This labor intensity can also introduce variability and errors into the process, impacting the consistency of the final product.
3. Limited Geometric Complexity While sand casting offers considerable design flexibility, there are still limitations when it comes to achieving extremely fine detail or very complex features. Deep cavities, narrow sections, and undercuts can pose challenges that may not be feasible without additional processes.
4. Solidification Issues During solidification, molten metal can experience shrinkage and porosity, leading to structural weaknesses in the final product. These defects can necessitate further testing and inspection to identify and rectify, adding time and costs to the production cycle.
5. Production Speed Compared to other methods such as die casting or investment casting, sand casting may be slower. The time taken to prepare molds, cool the metal, and extract the finished products can slow down the overall production process, which is a crucial consideration for high-demand applications.
6. Temperature Variation The sand used in the casting process can have varying thermal properties, leading to uneven cooling rates. This can cause problems such as warping or cracking, particularly in larger castings, necessitating careful control of the casting environment.
Conclusion
Sand casting remains a popular choice in various manufacturing sectors due to its cost advantages, design flexibility, and adaptability to large components. However, it also presents challenges such as poor surface quality, labor intensity, and production speed. Manufacturers must weigh these advantages and disadvantages carefully to determine if sand casting aligns with their production goals. By considering the specific requirements of their projects, businesses can leverage the benefits of sand casting while managing its limitations effectively.
Post time:ਦਸੰ. . 05, 2024 15:33
Next:rapid sand casting