3D Printing for Sand Casting Revolutionizing the Foundry Industry
The advent of 3D printing technology has paved the way for significant advancements in various industries, and sand casting is no exception. Traditionally, sand casting has been a labor-intensive process that involves creating molds from patterns made of metal, wood, or plastic. However, the integration of 3D printing into the sand casting process offers a more efficient and innovative approach, drastically changing the landscape of foundry operations.
What is Sand Casting?
Sand casting is one of the oldest and most widely used metal casting techniques. The process begins with the creation of a sand mold that is shaped according to the desired object. Once the mold is ready, molten metal is poured into it, allowing it to cool and solidify, after which the mold is broken away to reveal the final product. This method is popular due to its versatility and capability to produce complex shapes, but it has its limitations, including long lead times and the need for skilled labor to produce patterns and molds.
The Role of 3D Printing in Sand Casting
3D printing, or additive manufacturing, utilizes computer-generated designs to create objects layer by layer. In the context of sand casting, 3D printing technology can be used to produce molds and cores directly from digital files. This process offers several advantages over traditional methods
1. Reduced Lead Times Creating patterns for sand molds traditionally takes time, often requiring several weeks for fabrication. With 3D printing, molds can be produced in a matter of hours or even days, significantly speeding up the production process.
2. Cost-Efficiency The elimination of the need for physical patterns can lead to substantial cost savings. 3D printing allows for the production of complex designs without the need for expensive tooling, especially beneficial for low-volume production runs.
3. Design Flexibility 3D printing enables the creation of complex geometries that can improve the functionality of the final product. Designers can experiment with intricate designs that were previously impossible to achieve with traditional methods, thus enhancing product performance and innovation.
3d printing for sand casting
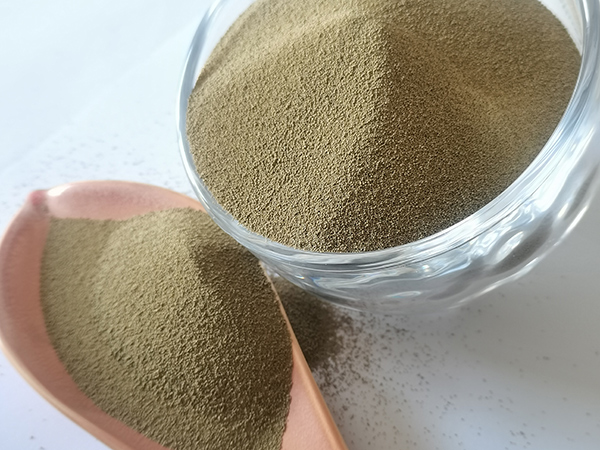
4. Sustainability The additive nature of 3D printing produces less waste compared to traditional subtractive manufacturing processes. Additionally, using 3D-printed molds can reduce the need for raw materials, aligning with global sustainability efforts in manufacturing.
Case Studies and Industry Adoption
Several companies have begun to incorporate 3D printing into their sand casting processes. For instance, GE Aviation uses 3D-printed sand molds for their jet engine components, resulting in quicker turnaround times and the ability to produce more complex parts. Similarly, Ford has experimented with 3D printing to create prototypes and castings for automotive components.
The adoption of this technology is not limited to large corporations; smaller foundries are also embracing 3D printing due to its accessibility and affordability. The introduction of user-friendly 3D printing systems tailored for the foundry industry allows smaller businesses to engage in rapid prototyping and customization without a significant investment.
Challenges Ahead
Despite the numerous benefits, the integration of 3D printing in sand casting is not without challenges. Material compatibility remains a concern, as the selection of suitable printing materials that can withstand high temperatures during the casting process is crucial. Furthermore, certain regulatory standards must be adhered to, particularly when dealing with industries such as aerospace and automotive.
Conclusion
3D printing technology has the potential to revolutionize the sand casting industry by improving efficiency, reducing costs, and enabling greater design freedom. As the technology continues to evolve, and with the growing adoption of additive manufacturing, we can expect to see a shift in the capabilities of foundries worldwide. Embracing this technology not only positions companies as leaders in innovation but also helps them meet the rising demands for sustainable and efficient manufacturing solutions. The future of sand casting is undoubtedly intertwined with the advancements in 3D printing, heralding a new era for this age-old technique.
Post time:ਦਸੰ. . 21, 2024 02:18
Next:Innovative Applications of 3D Printing Technology in Sand Casting and Sculpture Creation