The Sand Foundry Process An Overview
The sand foundry process remains one of the oldest and most prevalent methods for metal casting, widely utilized across various industries for producing complex metal components. This method's popularity stems from its cost-effectiveness, versatility, and ability to produce intricate designs with high precision. This article aims to elucidate the essential steps involved in the sand foundry process, along with its advantages and common applications.
Understanding Sand Casting
At its core, sand casting involves creating a mold from sand, which then allows molten metal to solidify into the desired shape. The major components of this process include pattern creation, mold making, metal pouring, cooling, and finishing.
1. Pattern Creation
The first step in the sand foundry process is creating a pattern, which is a replica of the object to be cast. Patterns can be made from various materials such as wood, metal, or plastic. They are typically designed slightly larger than the final product to account for metal shrinkage during cooling. Patterns can be single-use or reusable, depending on the production volume and economic requirements.
2. Mold Making
Once the pattern is ready, it is used to create a mold. The most common method involves mixing sand with a binding agent such as clay and water. This mixture is packed around the pattern to form a mold. The sand is pressed tightly to ensure it takes the shape of the pattern, which helps achieve the desired dimensional tolerances. After the pattern is removed, two halves of the mold are combined, creating a hollow cavity that matches the shape of the pattern.
After the mold has been prepared and assembled, it is time to pour the molten metal into the mold cavity. The metal is typically heated in a furnace until it reaches a liquid state, often exceeding temperatures of 1,500 degrees Celsius, depending on the specific metal being used. Once the metal is molten and has been thoroughly mixed, it is poured into the mold through a gating system, which directs the flow of metal and minimizes turbulence.
4. Cooling and Solidification
Post pouring, the molten metal needs to cool and solidify within the mold. The cooling time varies based on the metal type, the thickness of the casting, and the mold material. Proper cooling is crucial, as it ensures that the casting develops the desired mechanical properties. Once the metal has solidified, the mold is broken away to reveal the cast part.
sand foundry process
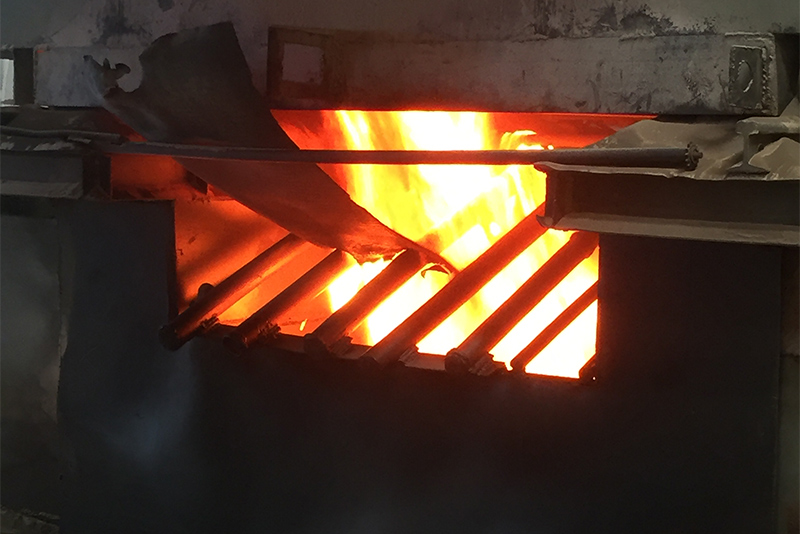
5. Finishing
After the casting is removed, it typically requires several finishing processes to achieve the final specifications. These processes may include trimming excess material, grinding, polishing, or machining to achieve tight tolerances and surface finishes. Additionally, quality inspection is often conducted to ensure that the final product meets industry standards.
Advantages of Sand Casting
The sand foundry process has several advantages that contribute to its ongoing relevance in manufacturing
- Cost-Effectiveness Sand casting is relatively low-cost, primarily due to the materials involved and the uncomplicated setup required, making it suitable for both small and large production runs.
- Material Versatility This process can accommodate a wide variety of metals, including aluminum, iron, and bronze, which broadens its application across different industries.
- Complex Geometries The capability to produce intricate shapes and designs is a significant benefit of sand casting, allowing manufacturers to meet diverse design requirements.
- Scalability Sand casting can be adapted for both small-scale productions, such as artisan crafts, and large-scale industrial applications, offering great flexibility.
Applications of Sand Casting
The applications of sand casting are vast, spanning industries such as automotive, aerospace, construction, and art. Common products include engine blocks, custom sculpture pieces, and components for heavy machinery. The ability to produce high-quality, complex metal parts makes sand casting an invaluable process in modern manufacturing.
In conclusion, the sand foundry process is a time-tested method that continues to thrive due to its numerous advantages. Its ability to produce intricate shapes, combined with its cost-effectiveness, ensures its ongoing utilization in various sectors. As technology advances, the sand foundry process is likely to evolve, integrating new methodologies that enhance efficiency and precision in metal casting.
Post time:Nov . 10, 2024 13:24
Next:Understanding Sand Casting Techniques for Cast Iron Manufacturing Processes