Sand Casting with Resin A Fusion of Tradition and Innovation
Sand casting is a time-honored manufacturing process that has stood the test of time, offering a reliable method to produce metal castings for various applications. While traditional sand casting typically utilizes sand mixed with clay and moisture, the evolution of material science has introduced innovative alternatives, including resin-bound sand. This modern technique combines the benefits of sand casting with the durability and precision of resin, enhancing the overall casting process.
The Basics of Sand Casting
Sand casting involves creating a mold by forming a mixture of sand and a bonding agent, which is then shaped to form the cavity into which molten metal is poured. This process is versatile and can produce complex geometries, making it a popular choice across industries, from automotive to aerospace. The traditional method relies heavily on the properties of the sands used and often requires a significant amount of finishing work post-casting.
Introduction of Resin
In recent years, resin has been increasingly incorporated into sand casting processes. Unlike traditional sand casting methods which depend heavily on moisture and clay for molding strength, resin-bonded sand offers enhanced durability and creates molds that can withstand higher temperatures. The use of resin as a binder provides more precise dimensions and surface finishes, reducing the amount of post-casting machining required. This is particularly important in industries where tolerance is critical, such as in the production of components for aircraft or precision engines.
Advantages of Resin Sand Casting
1. Increased Strength and Durability Resin-bonded sand molds exhibit superior strength and durability compared to traditional sand molds. This means that they can withstand the heat and pressure of molten metal more effectively, leading to fewer defects in the final casting.
2. Better Surface Finish The resin enables a smoother surface finish compared to traditional mold-making methods. This results in parts that require less finishing work, translating to reduced production times and costs.
sand casting resin
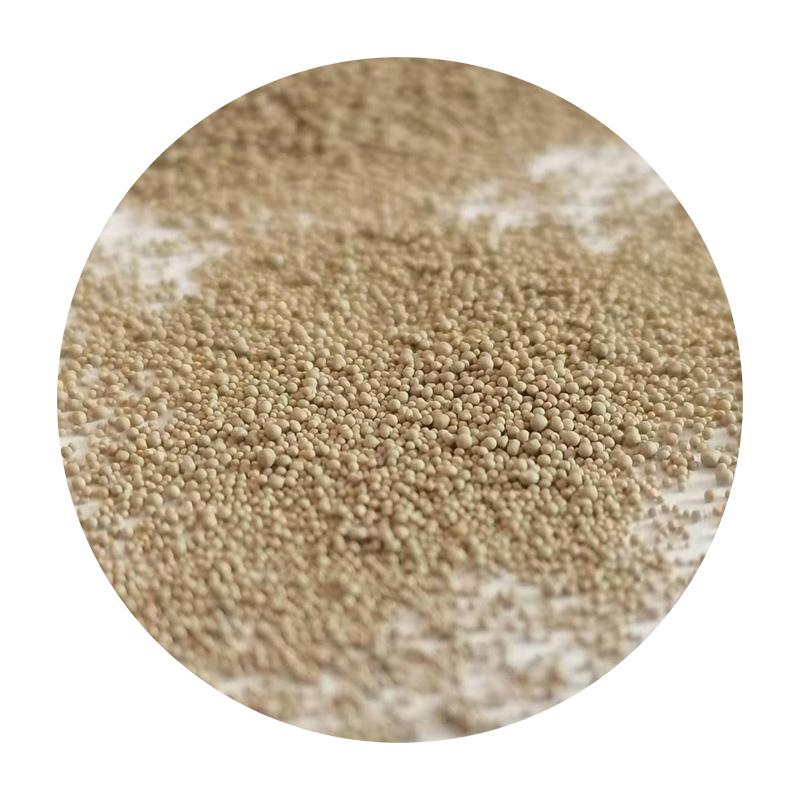
3. Dimensional Accuracy The precise nature of resin-bound sand allows for tighter tolerances, making it possible to achieve intricate designs that would be challenging with conventional methods.
4. Reduced Environmental Impact Traditional sand casting can produce significant waste and pollutants, particularly from the silica dust involved. Many resin systems have been developed to minimize harmful emissions, offering a more environmentally friendly alternative.
5. Versatility Resin sand casting can accommodate a broader range of metals, including aluminum, bronze, and iron. This versatility makes it suitable for various applications, from artistic sculptures to industrial components.
Applications of Resin Sand Casting
Resin sand casting is prevalent in several key industries. In the automotive sector, manufacturers use this technique to create engine blocks, transmission cases, and other critical components. In the aerospace sector, precision castings for turbine blades and structural elements benefit greatly from the accuracy and detail that resin sand casting can provide. Additionally, the art and sculpture industries are turning to this method for creating intricate and durable artistic pieces.
Future of Resin Sand Casting
As technology continues to advance, the potential for resin sand casting grows exponentially. Innovations in resin formulations and the introduction of 3D printing technologies are leading to even greater precision and customization in sand casting processes. Researchers are exploring bio-based or eco-friendly resins that could reduce the environmental impact of casting processes, thereby promoting sustainability within the manufacturing industry.
In conclusion, the integration of resin with sand casting processes has revolutionized the traditional craft, offering numerous advantages that cater to the needs of modern manufacturing. As industries continue to evolve and demand higher quality, more intricate designs, resin sand casting stands out as a formidable technique that harmonizes innovation with traditional practices. The future of this casting method is bright, promising advancements that will further enhance efficiency, precision, and sustainability in the manufacturing landscape.
Post time:Nov . 08, 2024 17:31
Next:sand casting steel