Sand Casting Definition and Overview
Sand casting, also known as sand mold casting, is a versatile and widely-used manufacturing process for producing metal parts. This method involves creating a mold from a mixture of sand, clay, and water, into which molten metal is poured to create desired shapes and structures. The simplicity and cost-effectiveness of sand casting make it a preferred choice in various industries, including automotive, aerospace, and machinery.
The Sand Casting Process
The sand casting process begins with the creation of a pattern, which is typically made of metal, plastic, or wood and reflects the shape of the final product. This pattern is used to form a mold in sand. The mold is developed in two halves known as cope (the top half) and drag (the bottom half). To create the mold, sand is packed around the pattern, and a binder, usually clay or resin, helps the sand grains stick together.
Once the mold is formed, the pattern is removed, leaving a cavity in the shape of the desired part. The two halves of the mold are then assembled, and if necessary, additional components such as cores (which create internal features) are added to the mold assembly. After this, the mold is ready to receive molten metal.
The next step is pouring the molten metal into the mold. The metal is usually heated in a furnace until it reaches a liquid state, then carefully poured into the mold cavity. After cooling and solidification, the mold is broken apart, and the casting is removed. The final step involves finishing processes such as trimming, grinding, and machining to achieve precise dimensions and surface quality.
Advantages of Sand Casting
One of the primary benefits of sand casting is its flexibility in terms of part design and size. The process can produce both small and large components, making it suitable for a wide range of applications. In addition, sand molds can be easily modified for different designs, allowing manufacturers to iterate on product designs without significant overhead costs.
sand casting definition
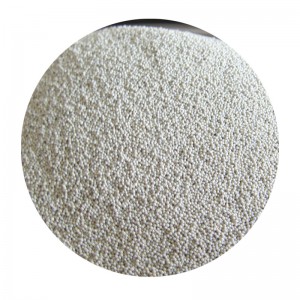
Moreover, sand casting is compatible with various metal alloys, including aluminum, iron, steel, and bronze. This adaptability enables industries to select materials best suited for their specific applications, ranging from lightweight components to those requiring high strength and durability.
Cost efficiency is another significant advantage of sand casting. The materials used for the sand molds are relatively inexpensive, and the process can be scaled to meet production needs, from single-item prototypes to large-batch manufacturing. Additionally, because sand is abundant and recyclable, the environmental impact of sand casting is comparatively low.
Limitations of Sand Casting
Despite its advantages, sand casting does have certain limitations. The surface finish achieved through sand casting may not be as smooth as that attained through other manufacturing processes like die casting or investment casting. This can necessitate additional machining to achieve the desired surface quality.
Furthermore, since sand casting relies on the formation of a mold, the dimensional accuracy might not be as tight as in other processes. The shrinkage of metal during cooling can also lead to variations in the final product's dimensions.
Additionally, the sand casting process is generally slower than more high-speed manufacturing methods, making it less suitable for industries requiring rapid mass production of uniform parts.
Conclusion
Sand casting remains a vital method in the realm of metal manufacturing due to its versatility, cost-effectiveness, and ability to work with various materials and part sizes. Although it has some drawbacks, its capacity to produce intricate shapes and structures makes it invaluable in industries where customization and unique designs are essential. The continuous advancements in sand casting techniques and materials promise to enhance its efficiency and application scope, ensuring its relevance in future manufacturing processes. As such, it continues to hold its ground as a fundamental manufacturing process that meets the varying demands of different sectors.
Post time:Dec . 31, 2024 17:25
Next:Exploring the Benefits and Applications of Ceramic Sand in Modern Industries