Physical Properties of Foundry Sand
Foundry sand is a crucial material in metal casting processes, playing an essential role in producing high-quality metal components. Its unique physical properties are fundamental to the effectiveness and efficiency of foundry operations. Understanding these properties enables foundries to select the appropriate type of sand for specific applications, thus optimizing casting performance, reducing defects, and improving overall quality.
One of the primary physical properties of foundry sand is its grain size distribution. The size and shape of the sand grains significantly affect the quality of the mold and the final casting. Generally, foundry sands are composed of silica, which has a high melting point and excellent thermal stability. The grain size of foundry sand typically ranges from fine to coarse, with finer sands providing better detail and smoother surface finishes, while coarser sands improve the flow of molten metal and reduce the risk of gas entrapment during casting.
Another important property is the sand's permeability, which refers to its ability to allow gases to escape during the molding and casting process. High permeability is essential to prevent gas buildup that can lead to defects such as blowholes or pinholes in the final casting. This property is influenced by both the grain size and the composition of the sand. Well-graded sands that contain a mix of different grain sizes generally offer optimal permeability.
The angularity and roundness of the sand grains also influence the mold-making process. Angular grains interlock better and provide higher compressive strength, making them preferable for producing molds that can withstand the pressure from pouring molten metal. In contrast, rounded grains flow more easily and produce molds with superior surface finishing, which can be beneficial for certain casting applications. Thus, the selection of grain shape needs to align with the specific requirements of the job at hand.
physical properties of foundry sand
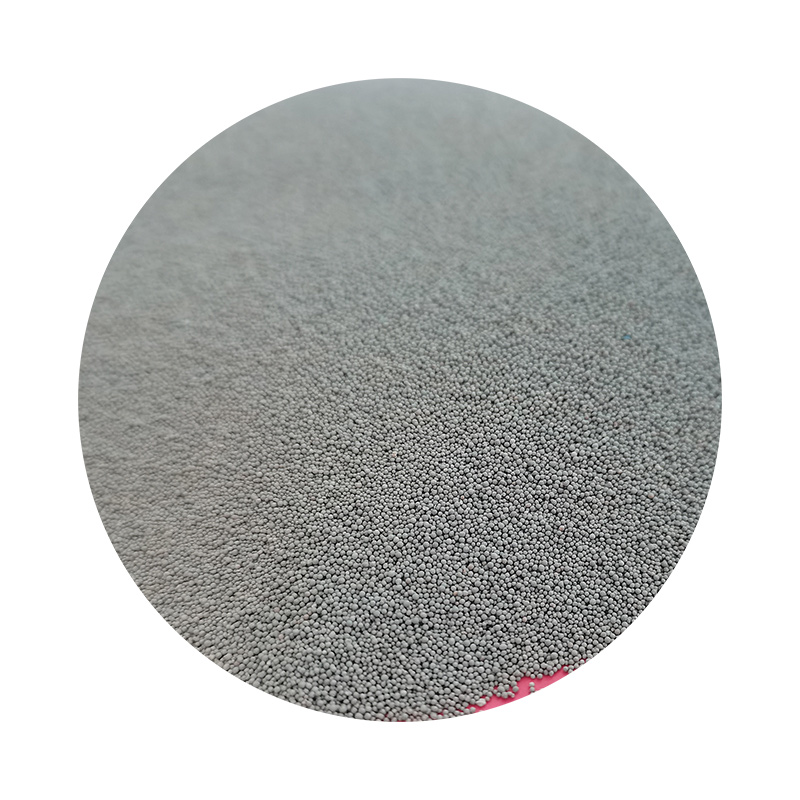
Moisture content is another critical factor affecting the physical properties of foundry sand. The right level of moisture improves the sand’s bonding characteristics and enhances its strength. However, excessive moisture can lead to clumping and hinder the molding process. Foundry operators often perform tests to determine the optimal moisture content, using tools such as the sand moisture meter.
Moreover, the thermal stability of foundry sand is vital as it must withstand high temperatures without degrading. Silica sand exhibits excellent thermal properties, enabling it to maintain its integrity during the casting process. In addition to thermal stability, the refractoriness of foundry sand, or its ability to resist melting, is a critical property for achieving defects-free castings.
Lastly, the reclamation properties of foundry sand cannot be overlooked. Used foundry sand can often be cleaned and reused, making it an economical and environmentally friendly choice. The ability to maintain the physical properties of sand after reuse is essential for sustaining both cost-efficiency and quality in foundry operations.
In summary, the physical properties of foundry sand—including grain size, permeability, angularity, moisture content, thermal stability, and reclamation ability—are crucial factors that impact the overall quality of the casting process. By carefully selecting and managing these characteristics, foundries can optimize their operations and produce high-quality castings that meet stringent industry standards.
Post time:Aug . 30, 2024 16:00
Next:how to sand 3d prints