Making Sand Casting A Comprehensive Guide
Sand casting is one of the oldest and most widely used metal casting processes in the manufacturing industry. It involves creating a mold from sand to produce metal parts. This method is favored for its versatility, cost-effectiveness, and suitability for both small and large production needs. In this article, we will explore the basics of sand casting, its advantages, the steps involved in the process, and its applications.
What is Sand Casting?
Sand casting is a process where sand is used as a mold material to shape molten metal into desired forms. The primary components of sand casting include the sand mold, the metal to be cast, and various tools and equipment that aid in the casting process. Typically, a mixture of sand and a bonding agent (usually clay) is compacted into a mold cavity. Once the metal is poured into the mold, it solidifies, and the mold is broken to retrieve the finished product.
Advantages of Sand Casting
Sand casting offers numerous advantages
1. Cost-Effectiveness Sand is an inexpensive material, and the molds can be made quickly, making this process economical for a wide range of applications.
2. Versatility This method can accommodate a variety of metals, including iron, steel, aluminum, bronze, and magnesium, making it suitable for diverse industries.
3. Complex Geometries Sand casting can produce complex shapes that would be challenging to achieve with other casting techniques.
4. Low Production Volume It is particularly advantageous for low to medium production volumes due to its lower tooling costs.
The Sand Casting Process
make sand casting
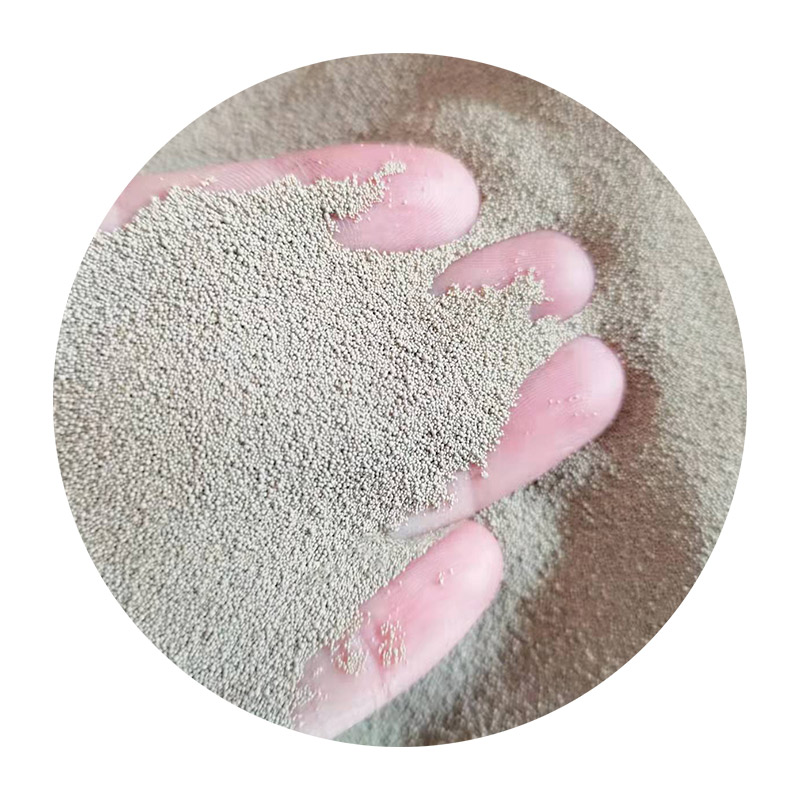
The sand casting process consists of several steps
1. Pattern Making The first step involves creating a pattern that represents the final product. Patterns are typically made from wood, metal, or plastic and are slightly larger than the intended casting to account for shrinkage during cooling.
2. Mold Preparation The next step is to prepare the mold by mixing sand with a binding agent. The sand is then packed around the pattern to create a mold, ensuring it is tightly compacted to withstand the molten metal’s heat and pressure.
3. Core Making For complex designs with internal cavities, cores made of sand may be created and placed in the mold before pouring in the metal.
4. Pouring Once the mold is ready, molten metal is poured into the mold cavity. This step requires precision to avoid defects such as air pockets or defects in the casting.
5. Cooling After pouring, the metal is allowed to cool and solidify, which can take anywhere from a few minutes to several hours, depending on the metal and the size of the casting.
6. Mold Breaking and Finishing Once the metal has cooled, the sand mold is broken apart to reveal the cast object. The cast is then cleaned to remove any sand and excess material. Additional finishing processes, such as machining or surface treatment, may be applied to achieve the desired specifications.
Applications of Sand Casting
Sand casting is widely used in various industries. It is commonly employed in
- Automotive Producing engine blocks, transmission cases, and other critical components. - Aerospace Manufacturing parts that require complex shapes and lightweight materials. - Industrial Machinery Creating components for equipment and machinery used in various sectors. - Art Artists and sculptors often utilize sand casting for creating sculptures and decorative objects.
Conclusion
Sand casting remains an essential method in the manufacturing of metal components due to its cost-effectiveness, versatility, and ability to produce complex shapes. Understanding the sand casting process allows manufacturers to leverage its advantages to meet the growing demands of various industries. As technology continues to evolve, innovations in sand casting techniques will likely enhance its efficiency and capabilities, ensuring its relevance in modern manufacturing for years to come.
Post time:Nov . 07, 2024 18:30
Next:Enhancing 3D Printed Models Through Effective Sanding Techniques and Tips