Understanding Sand Casting A Comprehensive Overview for Manufacturers
Sand casting is one of the oldest and most versatile manufacturing processes used today. Often referred to as sand mold casting, this method involves the creation of a mold from sand and then pouring molten metal into that mold to create a desired shape. It is particularly favored for its ability to produce intricate designs and large components, making it a popular choice among manufacturers across various industries.
The Basics of Sand Casting
The process begins with the design and preparation of the mold. Manufacturers typically use mixtures of sand, clay, and water, which help bind the sand grains together. The first step is to create a pattern, usually made from metal or plastic, which serves as a positive model for the mold. This pattern is pressed into the sand mixture, creating a cavity that mirrors the desired final product.
Once the mold is prepared, it is divided into two halves the cope (upper half) and the drag (lower half). The two halves are carefully assembled to ensure a precise fit, which is crucial for achieving accuracy in the final casting. After the mold is formed, the next step involves pouring molten metal into the cavity. The metal used can vary widely, from aluminum to iron to brass, depending on the application's requirements.
Advantages of Sand Casting
Sand casting offers several key advantages that make it an attractive option for manufacturers. First and foremost, it is cost-effective, especially for low to medium production runs. The materials used (sand, clay, and metal) are relatively inexpensive compared to other casting processes, such as die casting or investment casting. Additionally, sand molds can be reused multiple times, further minimizing costs.
Another significant advantage is the flexibility in design. Sand casting allows for the production of complex shapes that might be difficult or impossible to achieve with other methods. This flexibility is particularly beneficial in industries such as automotive and aerospace, where custom parts are often required.
Furthermore, the thermal characteristics of sand molding materials provide excellent heat retention, making it suitable for casting metals with high temperatures. As a result, sand casting can accommodate a wide range of alloys and materials, broadening its applicability across various sectors.
sand casting manufacturer
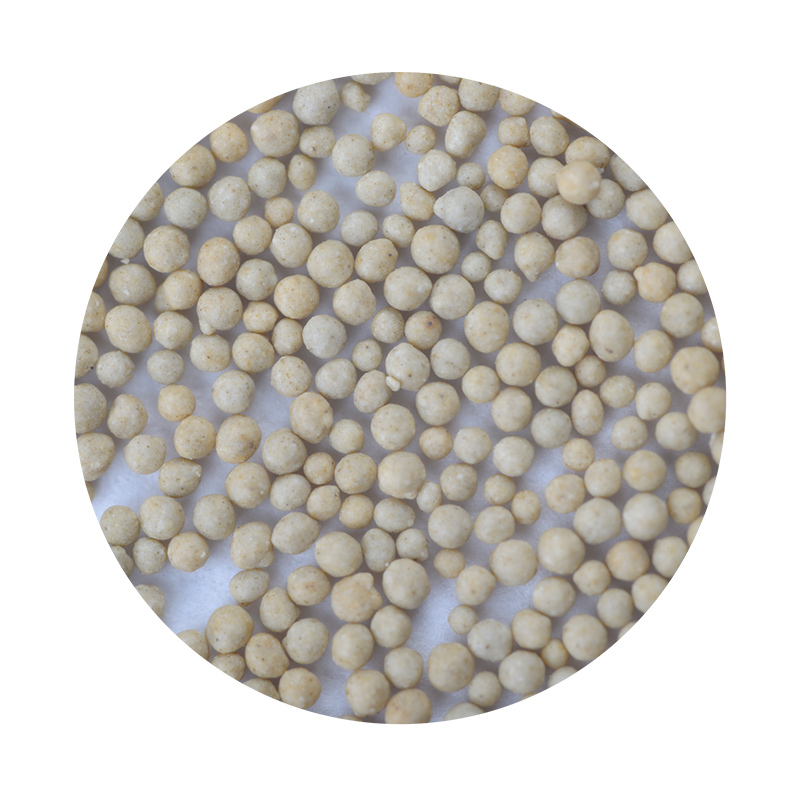
Challenges in Sand Casting
Despite its many advantages, sand casting does come with its challenges. One notable issue is the potential for defects in the final product, such as air pockets, sand inclusions, or uneven surfaces. To mitigate these risks, manufacturers must invest in quality control measures and ensure that the mold design and assembly are meticulously executed.
Moreover, the surface finish achieved through sand casting is typically rougher compared to other casting processes. This may necessitate additional machining or finishing processes to meet aesthetic and functional requirements, which can add time and cost to the production cycle.
The Future of Sand Casting
As technology advances, the sand casting industry is also evolving. Innovations in 3D printing technology are beginning to play a significant role in mold creation, allowing for faster and more precise production of complex molds. This can drastically reduce lead times and increase the efficiency of the manufacturing process.
Additionally, there is a growing emphasis on environmentally friendly practices in the sand casting industry. Some manufacturers are exploring the use of eco-friendly sand materials and recycling processes to minimize waste, aligning with global sustainability efforts.
Conclusion
In summary, sand casting remains a vital manufacturing process that combines tradition with innovation. Its cost-effectiveness, design flexibility, and ability to produce intricate parts make it a staple in many industries. While challenges such as potential defects and surface finish requirements exist, ongoing advancements in technology and sustainability practices are poised to enhance the future of sand casting. Manufacturers that embrace these changes will not only meet the demanding needs of their customers but will also contribute positively to the environment.
Post time:Nov . 08, 2024 18:35
Next:types of sand casting