Sand Casting Foundry Process An Overview
Sand casting is one of the most widely used metal casting processes, renowned for its versatility and cost-effectiveness. It involves pouring molten metal into a mold made from a sand mixture, which is then allowed to solidify, creating a desired shape. The sand casting process has been employed since ancient times and remains a staple in manufacturing today due to its numerous advantages.
Basic Components of Sand Casting
The sand casting process essentially consists of several key components the pattern, the mold, the core, the base, and the molten metal.
1. Pattern A pattern is a replica of the object to be cast. It is often made from metal, wood, or plastic and serves as a template for creating the mold. Patterns are typically slightly larger than the final product to account for shrinkage during cooling.
2. Sand Mold The mold itself is composed of sand mixed with a bonding agent (commonly clay) and water to form a cohesive structure. The sand is packed around the pattern to create a cavity that mirrors the shape of the object.
3. Core In cases where the final product features hollow sections, cores are used. These are additional sand structures placed within the mold to form these internal shapes.
4. Molt Metal Once the mold is completed, metal is heated to its melting point and poured into the mold cavity. Common metals used in sand casting include aluminum, iron, and bronze due to their favorable properties.
The Sand Casting Process
The sand casting process can be broken down into several steps
1. Pattern Making The first step is creating the pattern, which is crucial for the accuracy of the final product. The choice of material for the pattern can significantly affect the ease of mold creation and the quality of the final casting.
2. Mold Setup The pattern is placed in a sandbox and covered with a mixture of sand, clay, and water. After molding, the sand is compacted around the pattern to form two halves of the mold. The pattern is then removed, leaving a cavity. If required, cores are added at this stage.
sand casting foundry process
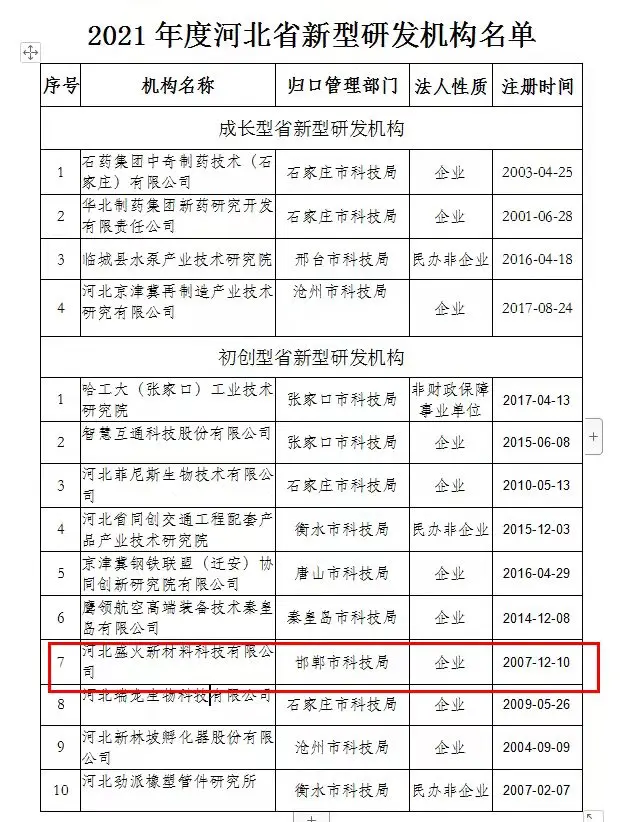
3. Pouring The next step involves heating the metal until it becomes molten. This molten metal is then poured into the prepared mold through a pouring spout. Care must be taken during this process to avoid any impurities that might affect the quality of the casting.
4. Cooling Once the mold is filled, the metal is allowed to cool and solidify. Cooling times can vary based on the type of metal and the thickness of the casting.
5. Mold Cleanup After the casting has solidified, the sand mold is broken apart to reveal the finished product. This rough casting typically requires additional finishing processes, including sanding, machining, and surface treatment to achieve the desired specifications.
Advantages of Sand Casting
The sand casting process offers several advantages, making it a popular choice in various industries
- Cost-Effective The materials used in sand casting are relatively inexpensive, and the process does not require high-cost equipment.
- Flexibility Sand molds can be easily modified, allowing for quick adjustments in design. This adaptability is particularly beneficial for prototypes and custom parts.
- Wide Range of Shapes Sand casting can produce a diverse array of shapes and sizes, from small intricate designs to large components like engine blocks.
- Suitable for Various Metals Unlike some other casting methods, sand casting is compatible with a variety of metals, making it highly versatile.
Conclusion
The sand casting foundry process is a time-honored technique that continues to play a vital role in modern manufacturing. Its ability to produce complex shapes with a wide range of materials at a low cost ensures its place as a fundamental process in the world of metalworking. As technology advances, the methods and efficiency of sand casting continue to evolve, promising even greater innovation and application in the future.
Post time:des . 16, 2024 20:00
Next:Exploring the Properties and Applications of Sand Casting Alloys in Modern Manufacturing