The Process of Sand Casting
Sand casting is a widely used manufacturing process that utilizes sand as the primary mold material to create complex metal parts. This versatile technique is ideal for producing both small and large quantities of components, ranging from simple shapes to intricate designs. In this article, we will explore the process of sand casting, its advantages, applications, and the factors that contribute to its popularity in the manufacturing industry.
Steps in the Sand Casting Process
1. Pattern Making The first step in sand casting is the creation of a pattern, which is a replica of the final product. Patterns are typically made from materials such as wood, metal, or plastic and are designed to be slightly larger than the actual part due to the shrinkage of metal as it cools. The patterns may also include core prints, which align with additional parts called cores to create internal cavities in the final product.
2. Mold Creation Once the pattern is ready, a mold is created by packing sand around it. The sand used in this process is usually a mixture of silica sand, clay, and water that gives it the ability to hold shape when compacted. The sand is pressed tightly against the pattern, and once it is formed, the pattern is removed, leaving a cavity that will shape the final metal part.
3. Core Making For parts that require internal features, cores made of similar sand mixtures are constructed. Cores are placed in the mold cavity before the molten metal is poured in, allowing for hollow spaces in the final casting.
4. Melting and Pouring The next step is to melt the chosen metal in a furnace. Commonly used metals include aluminum, iron, and bronze. Once the metal reaches its required temperature, it is poured into the mold through a sprue, allowing it to fill the cavity. The timing of this step is critical, as the metal must be poured while it is still in a liquid state, but not so late that it begins to solidify.
5. Cooling and Shakeout After pouring, the metal cools and solidifies within the mold. The cooling time varies depending on the size and thickness of the casting. Once the metal has cooled, the sand mold is broken apart in a process called shakeout, revealing the newly formed casting.
6. Finishing Processes The casting often requires further finishing operations, such as grinding, sanding, or machining, to remove any imperfections, excess material, or sand residue. This ensures that the final product meets the required specifications and surface finish.
how sand casting is done
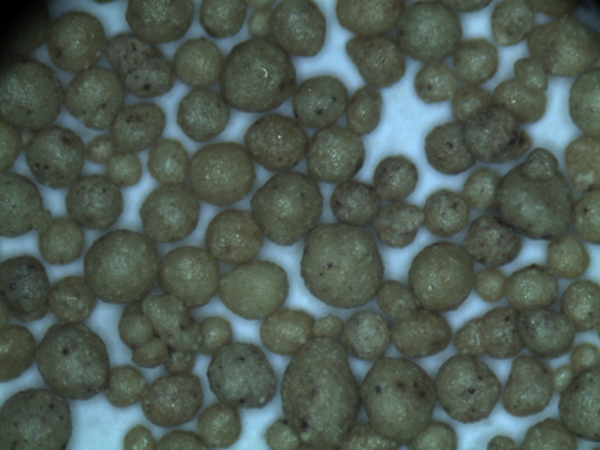
Advantages of Sand Casting
- Cost-Effectiveness Sand casting is relatively inexpensive compared to other casting processes, especially for small production runs. The materials used for molds are affordable, and modifications to patterns or molds can be made without incurring significant costs.
- Design Flexibility This method allows for a wide variety of shapes and sizes, making it suitable for diverse applications across many industries, including automotive, aerospace, and general manufacturing.
- Large Component Capability Sand casting can accommodate a wide range of casting sizes, from small machine parts to large structural components, giving it an edge in producing heavy industrial items.
Applications of Sand Casting
Sand casting is utilized in numerous industries for manufacturing components such as engine blocks, cylinder heads, and intricate mechanical parts. Its ability to create complex geometries makes it invaluable in producing custom parts and prototypes for various engineering applications.
Conclusion
In conclusion, sand casting is a fundamental manufacturing process that combines simplicity with versatility. Its steps—from pattern making to finishing—demonstrate the effectiveness of this technique in producing high-quality metal components. With its numerous advantages and wide-ranging applications, sand casting continues to be a go-to method in the world of manufacturing. Whether for industry giants or small workshops, sand casting remains a critical element in the creation of diverse metal parts.
Post time:dec . 05, 2024 01:47
Next:Affordable Sand Casting Solutions for Budget-Friendly Manufacturing Processes