Different Types of Foundry Sand
Foundry sand plays a pivotal role in the metal casting process, serving as a medium that shapes the final product. The choice of sand is crucial, as it affects both the quality of the cast and the efficiency of production. This article explores various types of foundry sand, their characteristics, and applications within the industry.
1. Silica Sand
Silica sand is the most commonly used foundry sand, primarily due to its abundance and ideal properties. It consists predominantly of silicon dioxide (SiO2) and is known for its high melting point, excellent thermal conductivity, and ability to withstand high temperatures. Silica sand is often used for making molds and cores because it can be easily shaped and provides fine detail in the final casting. However, it has limitations when it comes to its ability to hold moisture, which can impact the surface finish.
2. Green Sand
Green sand, or clay-bound sand, is a mixture of silica sand, clay, and water. It is called green because it is used in a damp state, retaining moisture that allows for easy molding. This type of sand is highly favored for its ability to form molds that are both strong and reusable. It is extensively used in iron and aluminum casting due to its excellent compressive strength and ability to produce intricate designs. The clay component helps in binding the grains, which enhances the durability of the mold. However, the preparation and recycling of green sand can be labor-intensive.
3. Resin Sand
different types of foundry sand
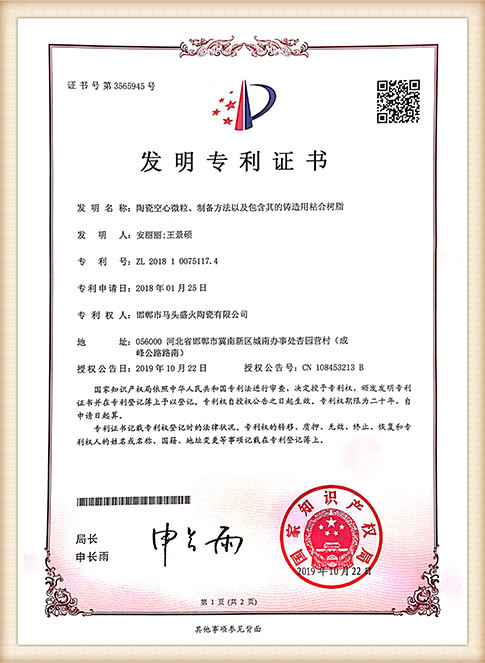
Resin sand is a mixture of silica sand and a thermosetting resin binder, which gives it superior strength and precision. This type of sand is gaining popularity due to its ability to withstand high temperatures and moisture without breaking down. It offers improved surface finishes and is particularly suitable for complex and intricate designs. Resin-coated sands can be easily reused, making them economical in the long run. Nonetheless, the cost of resin materials can be higher compared to traditional green sands.
4. Shell Sand
Shell sand is created by coating a silica sand grain with a thermosetting resin and is typically used in the shell molding process. This method involves heating the sand mixture, which forms a thin shell around the mold. The resulting molds have excellent surface finishes and fine details, making them ideal for precision castings in mechanical and automotive applications. While shell sand provides high accuracy, the production process can be more complex and cost-effective than other traditional methods.
5. Chromite Sand
Chromite sand, composed of chromium oxide, is known for its high thermal stability and low expansion rate. It is often used in steel and iron casting applications where high high temperatures are a concern. One of its primary advantages is its resistance to metal penetration, making it suitable for producing high-quality castings in demanding applications. However, chromite sand is often more expensive, limiting its use to applications that absolutely require its unique properties.
Conclusion
The type of foundry sand selected can significantly influence both the production process and the properties of the final casting. From traditional silica sand to advanced resin and shell sands, each type offers unique benefits and challenges. Understanding these differences is essential for foundry engineers and manufacturers aiming to optimize casting quality and production efficiency. As the industry continues to evolve, innovations in foundry sand technology may lead to even more sustainable and effective options in the future.
Post time:dec . 03, 2024 20:14
Next:The Evolution and Significance of Sand Casting Through the Ages