Why Sand Casting is Preferred
Sand casting, one of the oldest and most versatile metal casting processes, continues to be a preferred method in the manufacturing industry for various reasons. This traditional technique enables the production of complex geometries and large components, making it especially valued in industries such as automotive, aerospace, and heavy machinery. In this article, we will explore the key reasons why sand casting remains a favorable choice for manufacturers.
Cost-Effectiveness
One of the primary advantages of sand casting is its cost-effectiveness. The raw materials required for sand casting—primarily sand, clay, and water—are abundant and inexpensive. Additionally, the process does not require expensive tooling or machinery compared to other casting methods, such as investment casting or die casting. This significantly lowers the initial setup costs, making it an attractive option for small to medium-sized production runs as well as large-scale manufacturing.
Versatility
Sand casting is incredibly versatile in terms of the materials that can be used. It can accommodate a wide range of metals, including aluminum, iron, and bronze. This flexibility allows manufacturers to select the most suitable material for their specific application, optimizing performance and material properties. Moreover, sand casting can produce intricate shapes and sizes, from small components to large engine blocks, catering to diverse industry needs.
Complexity and Detail
The ability to create complex designs is another reason why sand casting is preferred. The use of sand allows for the creation of intricate patterns and details that might be challenging to achieve with other casting methods. Sand molds can be easily manipulated to incorporate cores or features like undercuts, enabling the production of detailed internal passages—key in industries such as aerospace where weight reduction and aerodynamic efficiency are paramount.
Adaptability to Changes
why sand casting is preferred
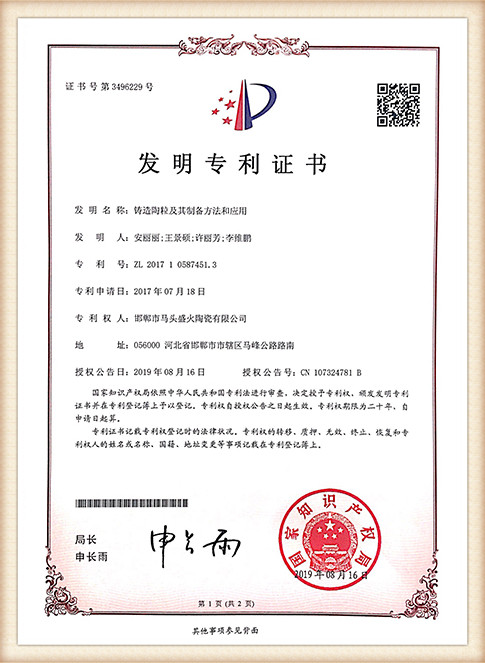
In today's fast-paced manufacturing environment, adaptability is crucial. Sand casting allows for rapid adjustments and changes in design without incurring significant costs or delays in production. If the need arises to modify a component or accommodate design changes, mold patterns can be easily altered, allowing for quick turnaround times. This responsiveness is vital in competitive markets where time-to-market can determine success.
Ease of Use and Learning Curve
The sand casting process is relatively simple, which makes it easier for new technicians and engineers to learn and master. The foundational skills required for sand casting can be acquired more quickly than those needed for more complex processes like investment casting or die casting. Consequently, companies can train their workforce more efficiently, ensuring they maintain productivity and quality while minimizing onboarding costs.
Robustness and Repeatability
Sand casting is known for its robustness and ability to produce reliable parts consistently. Once a pattern is created, it can be reused multiple times to manufacture identical or similar components, ensuring uniformity across production batches. This repeatability is crucial for maintaining quality standards, particularly in industries where precision is critical.
Environmental Benefits
Recent advancements in sand casting technology have also introduced greener practices in the industry. Foundries are increasingly reusing sand as well as utilizing environmentally friendly binders. The ability to recycle materials reduces waste and contributes to more sustainable manufacturing processes. Furthermore, innovations in sand casting have led to a reduction in energy consumption during the production process.
Conclusion
In summary, sand casting remains a preferred method in the manufacturing sector due to its cost-effectiveness, versatility, adaptability, and ease of use. The ability to produce complex geometries with a high degree of detail and repeatability continues to make it an essential process across various industries. As manufacturers seek ways to optimize production while maintaining sustainability, sand casting is likely to remain relevant. With ongoing advancements and innovations in the field, the future of sand casting looks promising, securing its place as a cornerstone of modern manufacturing techniques.
Post time:नोभ . 25, 2024 06:52
Next:Exploring Various Uses of Sand Casting Techniques in Modern Manufacturing Industries