The Advantages of Sand Casting Why It Remains a Preferred Method in Manufacturing
Sand casting is a widely used metal casting process that has been around for centuries. It involves the creation of a mold from sand and a binding agent, into which molten metal is poured to create a final product. Despite the advancement of various modern casting techniques, sand casting continues to be a popular choice among manufacturers for several compelling reasons.
Versatility of Materials
One of the primary advantages of sand casting is its versatility. This method can accommodate a wide range of metals, including aluminum, bronze, iron, and steel. This flexibility makes it suitable for a variety of applications, from small components to large industrial parts. Additionally, sand casting is adaptable to different alloys, allowing manufacturers to modify properties such as strength, ductility, and corrosion resistance to meet specific project requirements.
Cost-Effectiveness
In comparison to other casting methods, sand casting is often more cost-effective, particularly for low to medium production runs. The materials required for sand molds—primarily sand and a binder—are relatively inexpensive and readily available. Furthermore, the simple production process does not demand expensive machinery or technology, making it an accessible option for small to medium-sized enterprises. This economic advantage allows businesses to save on initial investment costs while still producing quality sand-cast products.
Ability to Create Complex Shapes
Sand casting excels in creating complex shapes and intricate designs that might be difficult or impossible to achieve with other manufacturing methods. The use of sand molds allows for significant design flexibility, enabling manufacturers to incorporate detailed features into their products. Whether it’s creating complex geometries for automotive parts or intricate designs for artistic applications, sand casting can easily accommodate these needs without excessive tooling costs.
Durability and Strength
why is sand casting used
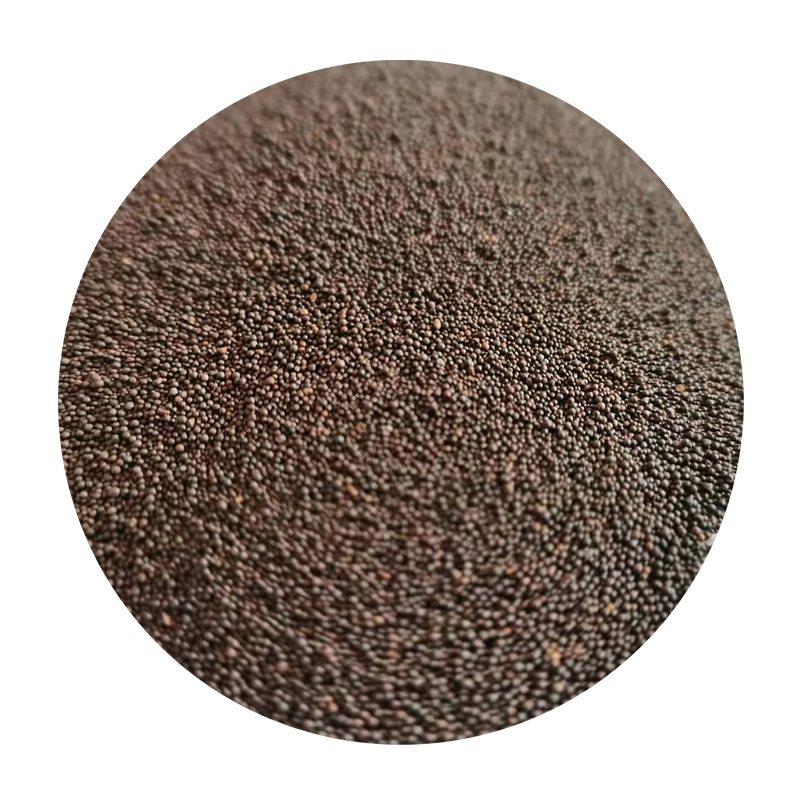
Another reason sand casting remains popular is the durability and strength of the final products. The sand casting process enables the production of components that have high density and structural integrity. The controlled cooling rates associated with the sand mold allow for the development of favorable microstructures in the finished metal, which can enhance the mechanical properties of the component. This durability makes sand-cast products suitable for high-stress applications in various industries, including automotive, aerospace, and machinery.
Sustainability
As environmental concerns continue to shape manufacturing practices, sand casting presents a sustainable option. The sand used in casting can be recycled multiple times, reducing waste and the need for new raw materials. Traditional sand casting molds can be reused after the casting process, minimizing environmental impact. Additionally, advancements in the use of eco-friendly binders may further enhance the sustainability of sand casting operations.
Short Lead Times
The sand casting process can also offer shorter lead times, particularly for prototype development. Manufacturers can quickly create molds using traditional sand casting techniques, allowing for rapid iterations of design. This agility is particularly beneficial in industries that require quick turnaround times and flexibility to adapt to changing market demands.
Skill and Craftsmanship
Finally, sand casting emphasizes skill and craftsmanship. Skilled workers who understand the nuances of the process can produce high-quality products with consistent properties. This artisan approach adds a level of quality assurance that automated processes may lack. Many manufacturers value the human element that skilled workers bring to the sand casting process, leading to a greater emphasis on quality and attention to detail.
Conclusion
In conclusion, sand casting continues to be a preferred method in the manufacturing world due to its versatility, cost-effectiveness, ability to create complex shapes, and the durability of the final products. As industries evolve and adapt to new technological challenges, sand casting remains a reliable and sustainable option that balances traditional craftsmanship with modern manufacturing needs. Whether for small-scale projects or large industrial applications, the benefits of sand casting ensure its place in the future of manufacturing.
Post time:नोभ . 29, 2024 19:29
Next:Cast of the Enchanted Sand Fortress Revealed in a Magical Tale